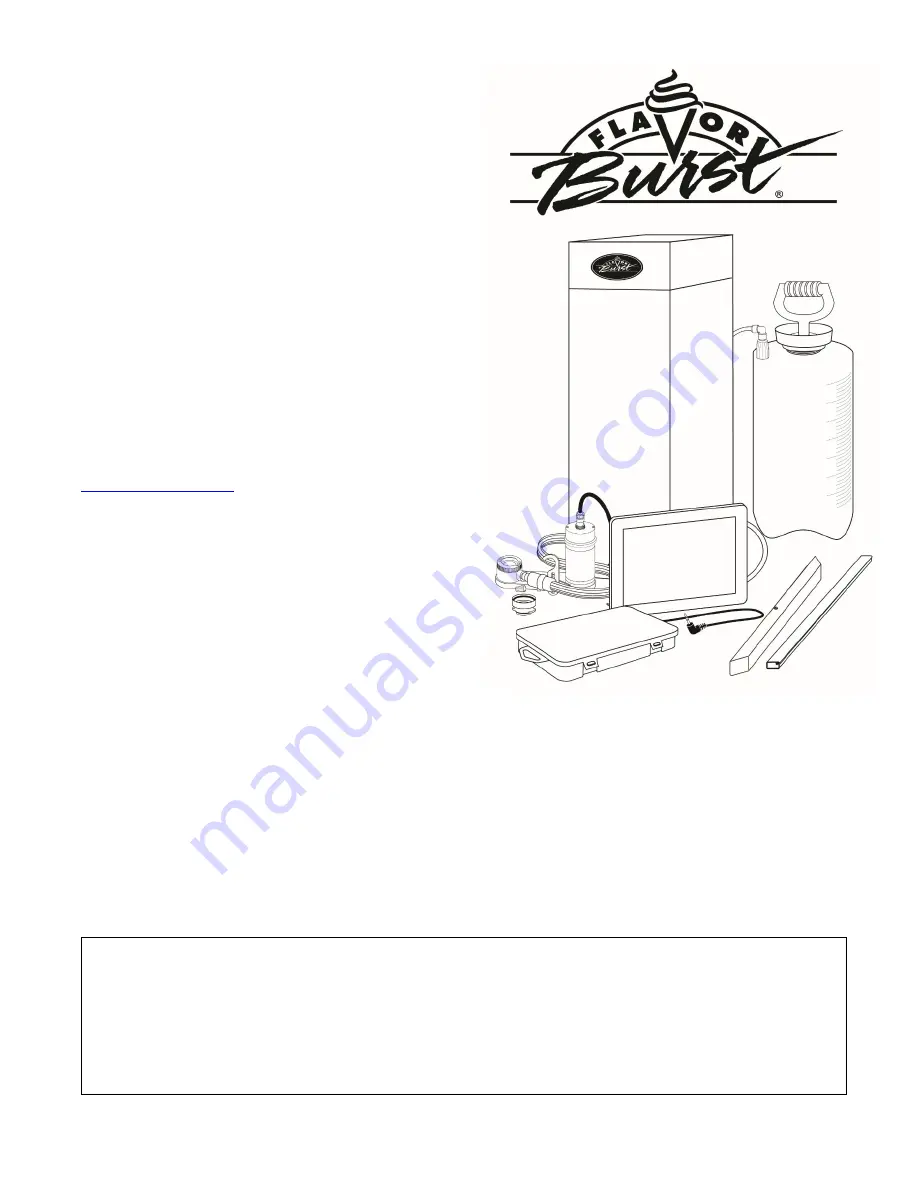
©2021 Flavor Burst Company Printed in September
Printed in
All Rights Reserved
The United States of America
Flavor Burst
®
Frozen Beverage System
Model CTP 80BEV
Equipment, Maintenance and
Operations Manual
Manufactured by
Flavor Burst Company
499 Commerce Drive
Danville, IN 46122
For general information and to locate a
distributor near you, call or visit our website:
Phone: (317) 745-2952
Toll Free Number: (800) 264-3528
Fax: (317) 745-2377
www.flavorburst.com
For pricing, ordering and support, contact one
of our qualified distributors.
Warranty
An installation and warranty form is provided with every CTP 80BEV system, located inside the CTP
80BEV unit with this manual. It is important that the operator carefully review the warranty and
installation documents accompanying the unit before using this system. Any questions or concerns
regarding the warranty should be clarified upon delivery or installation. For more information, contact
your local authorized Flavor Burst
®
distributor.
Summary of Contents for CTP 80BEV
Page 7: ...6 PAGE INTENTIONALLY LEFT BLANK...
Page 9: ...8 General System Overview Figure 1...
Page 14: ...13 PAGE INTENTIONALLY LEFT BLANK...
Page 15: ...14 Blending Assembly and Related Parts Figure 3...
Page 17: ...16 Syrup Pump and Related Parts Figure 4...
Page 19: ...18 Sanitizer Pump and Related Parts Figure 5...
Page 22: ...21 PAGE INTENTIONALLY LEFT BLANK...
Page 23: ...22 Electronic Parts and Connections Figure 6...
Page 25: ...24 Spare Parts Kit Figure 7...
Page 26: ...25 PAGE INTENTIONALLY LEFT BLANK...
Page 38: ...37 PAGE INTENTIONALLY LEFT BLANK...
Page 50: ...49 PAGE INTENTIONALLY LEFT BLANK...