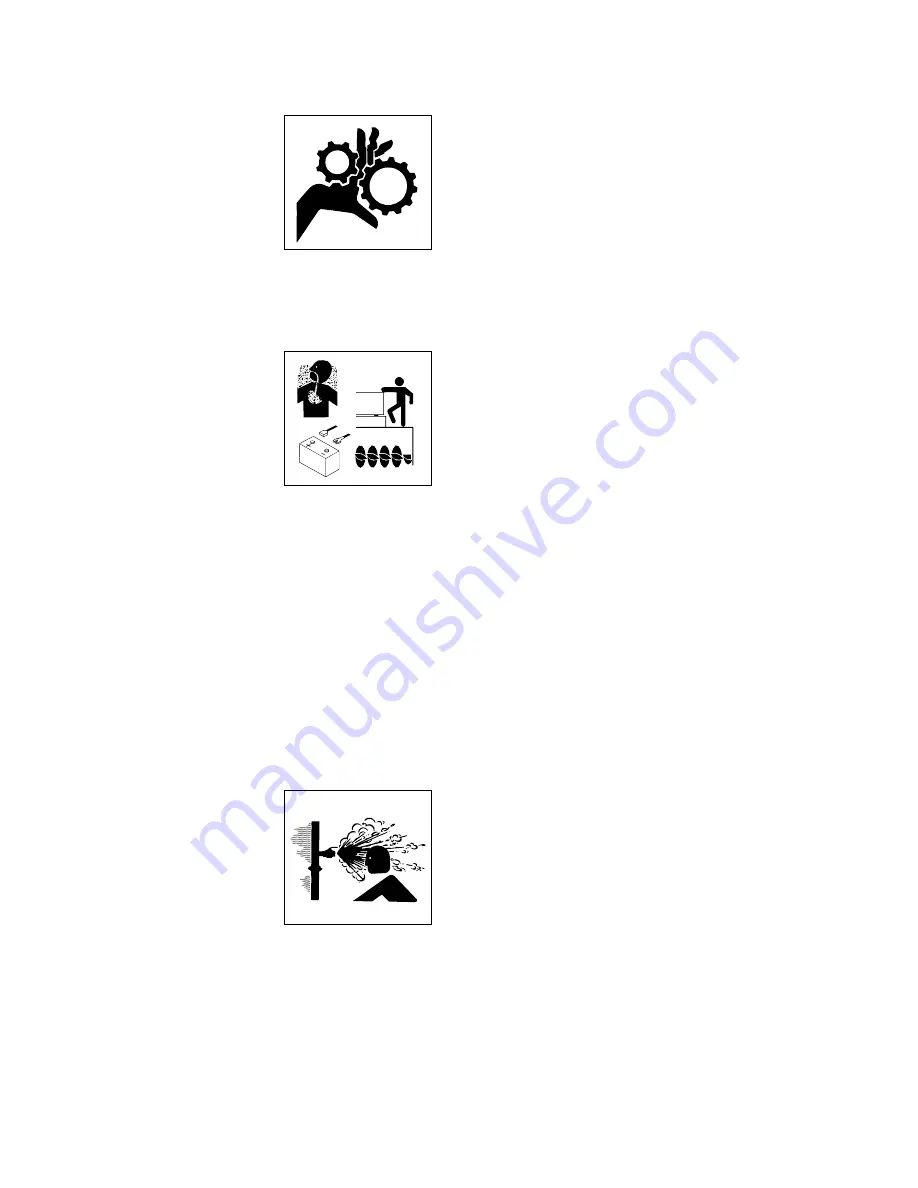
4
MAINTENANCE:
1. Before servicing the
machine, turn off engine
and allow all moving parts
to stop. To prevent acci-
dental starting disconnect
battery cables. Tag the
engine operating area to
show that the machine is
being serviced. Use lock-
out/tagout procedure (OSHA 29 CFR 1910.147).
2. Certain hydroseeding amendments, when combined
with or without the addition of water or heat or the ele-
ment of time, may react causing harmful or deadly
gasses! Consult your mate-
rial suppliers regarding
reactivity information. The
slurry tank must be flushed
and drained after each day
of operation.
3. Your slurry tank may be
considered a confined
space by OSHA under 29 CFR 1910.146. Before
entering any confined space, your company must
develop a procedure for safe entry. Make sure your
company’s plan meets all the requirements of 29 CFR
1910.146. including the following:
a)
Drain, flush and ventilate tank interior.
b)
Turn off engine and disconnect battery cables
and perform lockout/tagout procedures. (29 CFR
1910.147)
c)
Provide continuous ventilation or proper breath-
ing apparatus.
d)
If tank must be entered, personnel entering the
tank must be tethered to a lifeline.
e)
Provide stand-by individual outside of tank able to
communicate with person inside and able to haul
him out with lifeline if necessary.
4. Before loosening any
clamps or opening any
valves, determine if material
in the line is hot by feeling
the pipe. Do NOT allow
material to come in contact
with personnel. Severe bod-
ily injury could result.
5. On trailer units perform general maintenance such as
checking the safety chains, hitch and hitch bolts, tires,
brakes. Repair or replace if worn or broken. Never
operate machine on improperly inflated or damaged
tires. Always use a safety cage or cable restraints
when re-inflating a repaired tire.
6. Radiator maintenance: Liquid cooling systems build
up pressure as the engine gets hot. Before removing
radiator cap, stop the engine and let the system cool.
Remove radiator cap only after the coolant is cool.
7. Battery maintenance: Lead-acid batteries contain sul-
furic acid, which damage eyes of skin on contact.
Always wear a face shield to avoid acid in the eyes. If
acid contacts the eyes, flush immediately with clean
water and get medical attention. Wear rubber gloves
and protective clothing to keep acid off skin. Lead
acid batteries produce flammable and explosive
gasses. Keep arcs, sparks, flames and lighted tobac-
co away.
8. Filling of fuel: Never fill the tank with the engine run-
ning, while smoking or when near an open flame.
Never smoke while handling fuel or working on the
fuel system. The fumes in an empty container are
explosive. Never cut or weld on fuel lines, tanks or
containers. Move at least 10 feet (3 meters) away
from fueling point before starting engine. Wipe off any
spilled fuel and let dry before starting engine.
NOTE:
Be careful not to allow fuel, lubricant,
hydraulic fluid or cooling fluids to penetrate into the
ground or be discharged into the water system.
Collect all fluids and dispose of them properly.
9. It is recommended that only authorized genuine FINN
replacement parts be used on the machine.
10. Do not use either cold start fluid if engine is equipped
with glow plug type preheater or other intake manifold
type preheater. It could cause an explosion or fire and
severe injury or death.
11. Diesel fuel or hydraulic fluid under pressure can pen-
etrate the skin or eyes and cause injury, blindness or
death. Pressure may build up in the hydraulic system;
use caution when removing the cap.
12. Make certain that all decals on the machine are main-
tained in good legible condition. Replacement decals
are available through Finn Corporation by specifying
part number shown in the lower right hand corner of
the decal. See page 5 for the current safety decals
mounted on the unit. See pages 72-73 in the Parts
Manual for the location and quantity of all decals on
this unit.
Summary of Contents for HydroSeeder T120
Page 2: ...BLANK...
Page 26: ...Figure 4 22...
Page 38: ...NOTES 34...
Page 39: ...NOTES 35...
Page 40: ...NOTES 36...
Page 41: ...NOTES 37...
Page 42: ...NOTES 38...
Page 43: ...NOTES 39...
Page 44: ...NOTES 40...
Page 45: ...41 T90 120 II HydroSeeder Parts Manual Model SS LBT90 SS...
Page 79: ...75...