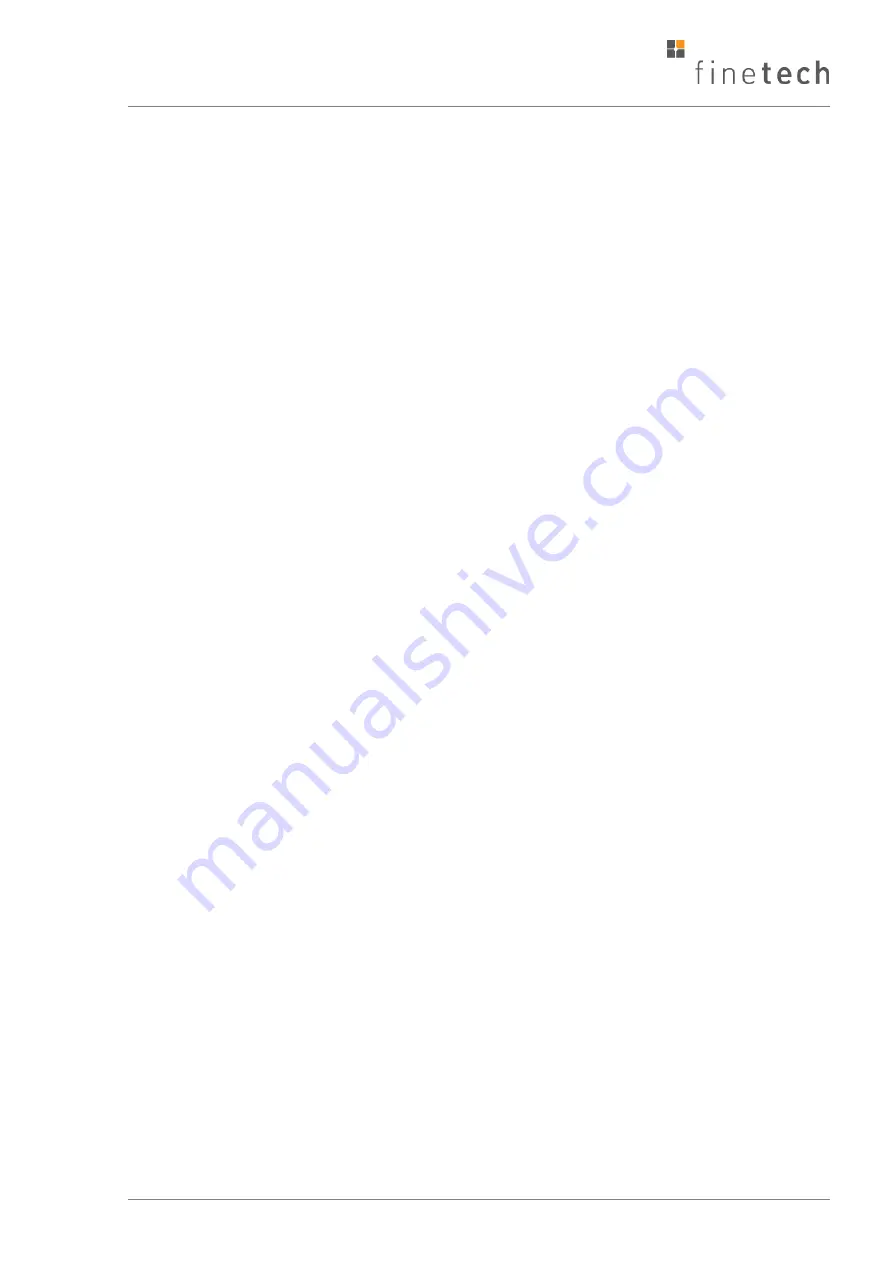
FINEPLACER
®
lambda
Rev-Nr. 1.1
13
3
The FINEPLACER
®
System
3.1
Introduction
Like every FINEPLACER
®
, the lambda has been designed for versatile use and ease
of operation and maintenance, and is made up of functional modules. The operator
should thoroughly understand the function and control of each module and tool in
the system before using it.
The numbers of machine parts given in brackets correspond to the numbers in table
2 of this text.
The Flip Chip Bonder consists of the following parts:
•
Base Module with base plate (70), support arm (71), stationary beam splitter
optics (30), illumination, camera (18) and positioning table (29), further placer
Control Box (39), table foot switch (64) and vacuum foot switch, as well as
cables and hoses.
•
Vision modules, e.g. or MIRAGE (37) or side camera with common video
monitor.
•
Process Modules, e.g. placer arm (27) with positioning head (20), Ultrasonic
or ACF Module.
•
Auxiliaries, e.g. optional pipette (24) or Target Finder.
FINEPLACER
®
s may be additionally equipped with various optional modules, mostly
to be retrofitted easily to adapt to customer's requirements.
3.2
Major Assemblies of the Basic Equipment
3.2.1.1
Base Plate (70)
The base plate carries the support arm (71) and the pivot bearing with the pivot arm
(27). Optionally it is possible to add an ultrasonic transducer to the pivot arm.
The base plate serves as the highly precise finished gliding plane for the positioning
table (29), and also contains an electromagnet which holds the table in position
when the air cushion is deactivated and allows the
θ
fine rotation.