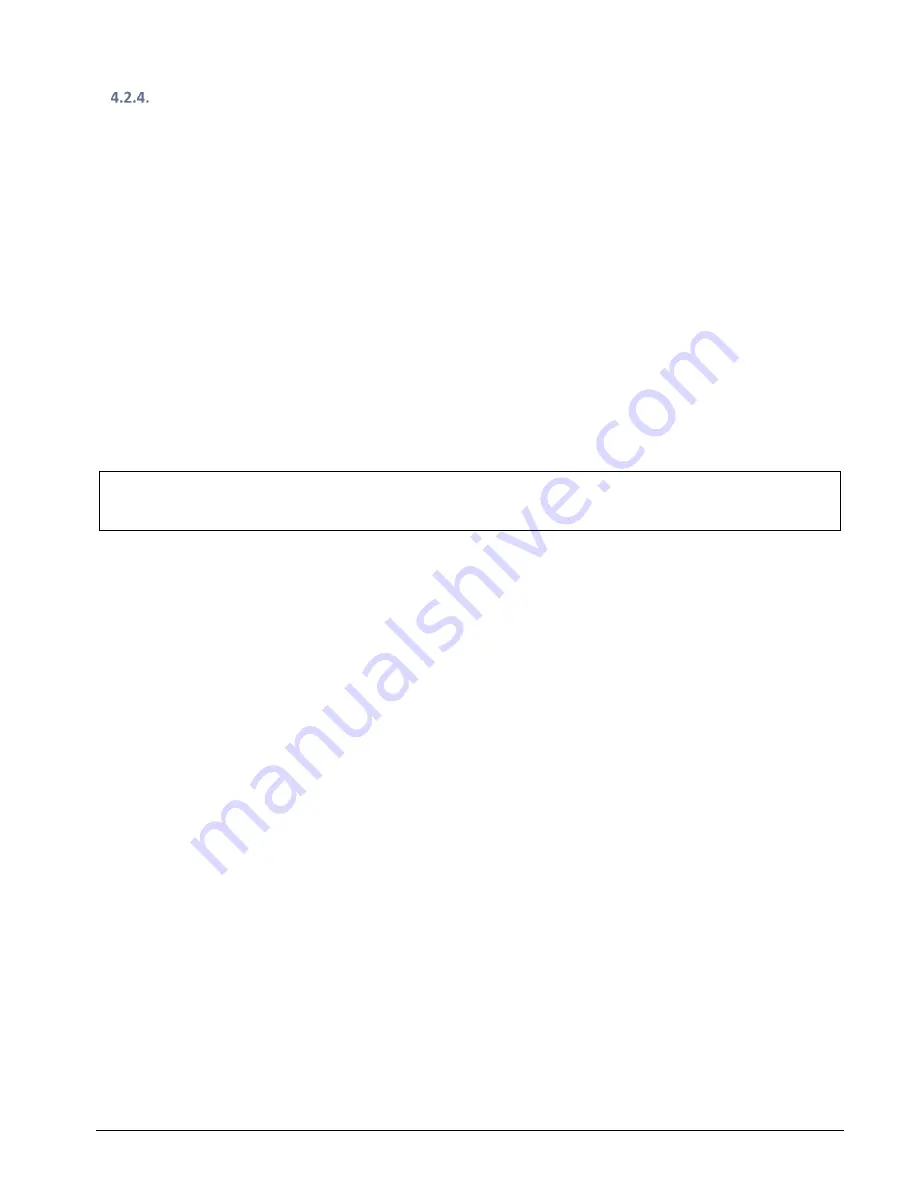
P/N
06
‐
791
‐
4
(Rev.
4)
Page
59
704
SW
10
th
Street,
P.O.
Box
610,
Blue
Springs,
Missouri
64013
‐
0610
U.S.A.
●
Phone:
(816)
229
‐
3405
●
www.fike.com
Frost
Protection
Water
filled
pipes
and
reservoirs
located
in
locations
with
risks
of
frost
shall
be
trace
heated,
and
the
trace
heating
system
shall
be
monitored
by
an
FM
Approved
alarm
system.
The
pipes
leading
up
to
the
water
mist
nozzles
shall
be
installed
in
a
frost
free
location.
4.3.
Wet
Alarm
Control
Valve
The
Wet
Alarm
Check
valve
(WAC)
shall
be
installed
as
shown
on
the
system
design
documentation,
and
in
accordance
with
the
manufacturer’s
instructions.
Where
the
WAC
valve
is
used,
refer
to
Fike
document
06
‐
791
‐
3
for
installation
instructions.
The
valve
shall
be
installed
so
it
is
accessible
for
operation,
inspection,
and
maintenance,
but
shall
not
be
installed
where
it
will
be
subject
to
damage
that
would
prevent
proper
operation.
4.4.
Automatic
Bypass
Valve
Every
DuraQuench
pump
skid
is
equipped
with
an
automatic
bypass
valve
that
ensures
a
continuous
flow
through
the
pump
when
running
by
diverting
a
portion
or
all
of
the
pump
discharge
back
to
the
pump
suction
based
on
the
process
flow.
The
bypass
valve
is
closed
when
the
process
flow
is
greater
than
the
control
set
point
(that
is,
minimum
flow
rate
required),
opens
gradually
as
the
process
flow
is
reduced
and
pressure
increases,
and
is
fully
open
when
the
process
flow
is
reduced
or
stopped
resulting
in
an
increase
in
pressure
greater
than
the
bypass
valve’s
set
point.
NOTE:
The
bypass
valve
is
factory
set
to
begin
opening
when
the
inlet
pressure
to
the
valve
reaches
250
psi
(17.2
bar).
Should
the
operating
set
point
or
opening
and
closing
speed
of
the
bypass
valve
need
to
be
adjusted,
refer
to
Appendix
A
for
instructions.
4.5.
Nozzles
The
OH
‐
VSO
nozzles
shall
be
installed
in
strict
accordance
with
the
design
documentation
prepared
for
the
specific
installation
and
in
accordance
with
the
following
guidelines.
Any
required
deviations
must
be
approved
prior
to
installation.
1.
Great
care
shall
be
given
when
handling
the
nozzles.
The
handler
shall
be
very
cautious
around
the
bulb
of
the
nozzles
as
the
bulb
is
a
very
sensitive
and
crucial
component
on
the
nozzles.
2.
Upon
arrival,
it
is
advised
that
the
nozzles
and
other
components
are
subjected
to
thorough
visual
inspections.
Should
the
original
packaging
appear
to
have
been
breached,
dented
or
in
any
way
harmed
or
compromised,
the
compromised
package(s)
shall
be
returned
to
Fike.
3.
Nozzle
shall
only
be
installed
in
smooth
ceilings
having
a
slant
coefficient
of
less
than
or
equal
to
8.3%.
4.
Nozzles
shall
be
installed
in
a
pendent
(downward)
position,
recessed
into
the
ceiling
with
the
rosette
(trim
ring)
flush
to
the
ceiling
surface
and
the
nozzle
cover
plated
3/8”
to
5/8”
(10
to
15
mm)
below
the
ceiling
as
shown
in
Figure
52.
5.
The
02
‐
15267
spanner
wrench
(See
Figure
53)
must
be
used
to
correctly
install
the
nozzle(s).
The
nozzle
to
be
installed
shall
be
placed
in
the
spanner
wrench
and
then
screwed
onto
the
pipe
system.
The
nozzle
is
correctly
positioned
when
the
circular
spanner
mark
is
flush
to
the
ceiling
surface.
The
spanner
wrench
requires
a
mounting
hole
of
1
‐
7/8”
(48
mm)
diameter
in
the
ceiling
surface
for
nozzle
installation.
6.
Nozzles
shall
be
installed
in
locations
where
the
nozzle
is
not
likely
to
sustain
physical
damage.
7.
Nozzles
shall
be
installed
below
construction
beams
and
major
obstructions
to
provide
a
homogenous
water
mist
distribution
in
the
enclosure.
See
Section
3.12.1.3.
8.
Nozzle
shall
be
installed
in
one
level
at
the
maximum
height
indicated
on
the
design
documentation.
Summary of Contents for DuraQuench
Page 93: ......