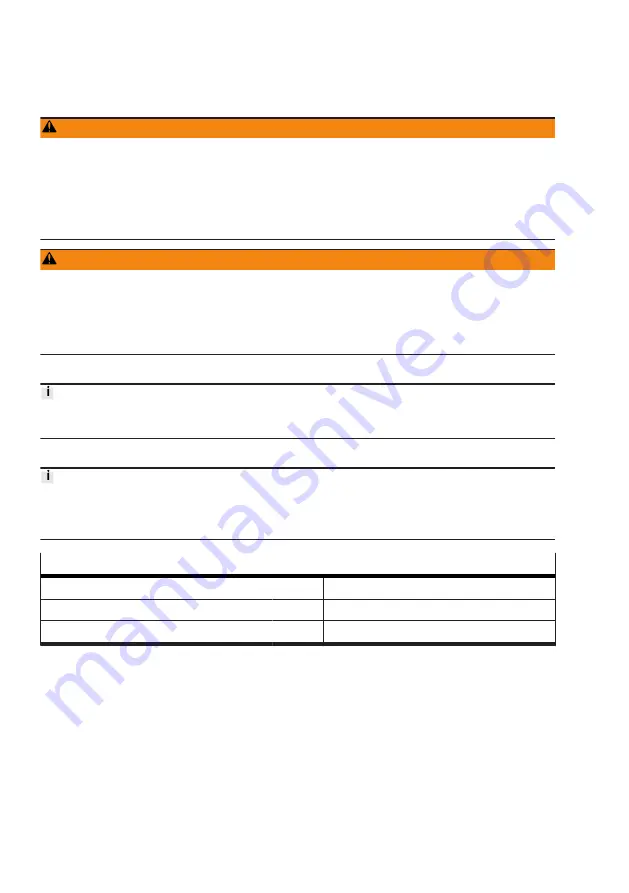
78
Festo — EXCH — 2022-03b
Maintenance
11
Maintenance
WARNING
If the planar surface gantry is mounted vertically
If the toothed belt breaks, the Y-axis (cross-brace) will fall down uncontrolled with the tool load.
Danger of death and property damage by falling Y-axis (cross-brace)
• At every lubrication and every 6 months:
Inspect the toothed belt for damage, increased abrasion and missing teeth.
• Contact Festo Service if signs of wear or damage are found
WARNING
Serious injuries due to uncontrolled movements of the planar surface gantry.
• Maintenance work may only be conducted by qualified personnel with corresponding qualifications
in accordance with this description.
• The personnel assigned to perform maintenance must be familiar with commissioning and manual
operation of the planar surface gantry.
11.1
Cleaning
Clean the product only in exceptional cases with non-abrasive cleaning agents and soft cloths.
• Do not clean the guide components, e.g. guide rails.
11.2
Lubrication
The product is lubricated initially upon delivery. Proper lubrication is required for trouble-free opera-
tion and to increase the service life of the linear guides.
• Use suitable Festo equipment
Specifications
Lubricant
ISOFLEX TOPAS NB52
1)
Lubrication interval per axis
[km]
2500
Volume of lubricant per lubrication nipple
[g]
1
1) Klüber Lubrication, Munich
Tab. 16: Lubrication requirements