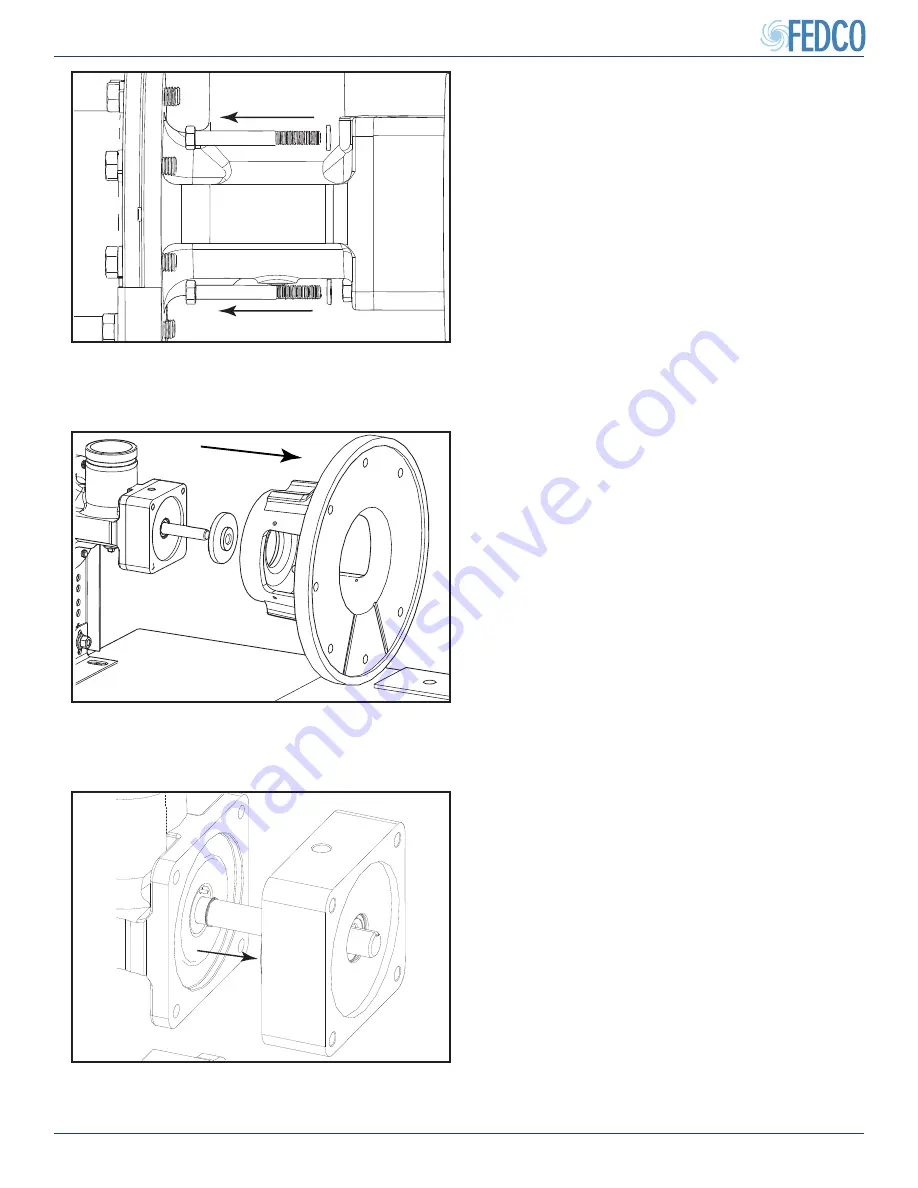
MSS
TM
Series
© Copyright 2022 Fluid Equipment Development Company | www.fedco-usa.com
-
19
-
Figure 27 - Removing High Pressure Seal
Carrier
Figure 26 -
Removing Motor Adapter and
Shipping Plug
Figure 25 - Removing Inlet Housing Bolts
5. Remove the high pressure seal carrier from
the inlet housing.
4. Remove the motor adapter and shipping
plug from the inlet housing.
3.
Remove the bolts and lock washers from the
inlet housing.
Pump Overhaul Continued