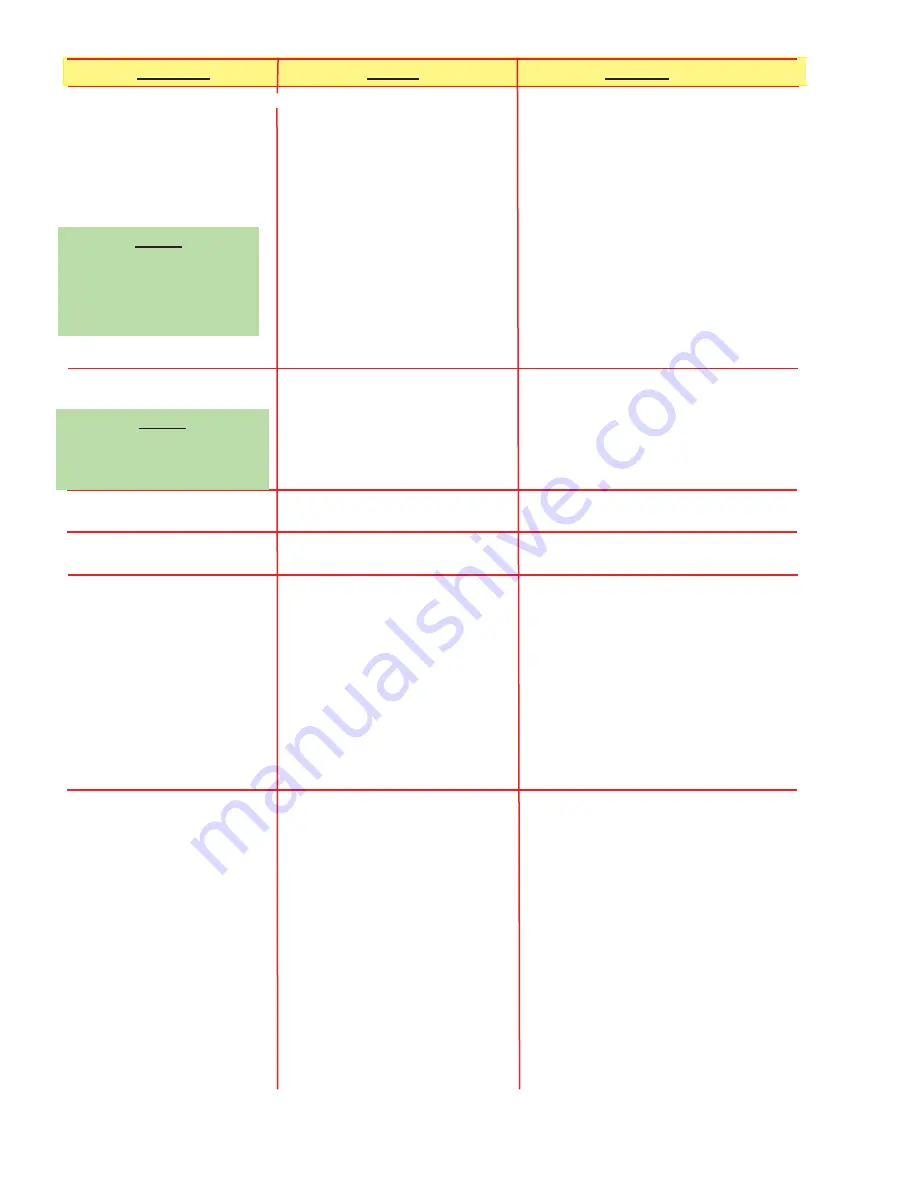
36
(Item 13.29 continued from previous page.)
E. Level Control too low.
E. Level Control settings may need to
be raised due to excessive CO
2
in
the chamber. Raise the Level
Control settings using the
instructions in Section 10.2 of
this
manual.
F. “Regulated CO2” transducer
F. Insure that the tank transducers
reading inaccurately.
are reading the CO
2
regulated
pressure correctly [i.e., filling about
5-7 psi (34.5-48.3 kPa) below
“REG
CO2”].
G. Secondary regulator pressure G. Insure CO
2
regulator has not
creeping up.
climbed above preset 28-32 psig
(193.1-220.6
kPag).
H.
CO
2
check valve problem.
H. Inspect CO
2
check valve. Clean
or replace if necessary.
13.30
MaxFil,
A.
Secondary
CO
2
pressure is
A. Check Secondary CO
2
for correct
Maximum Fill
set above 40 psig.
setting of 28-32 psig (193.1-220.6
kPag).
B. Secondary
regulator
B. Insure
CO
2
regulator has not
pressure creeping up.
climbed above 32 psig
(220.6 kPag). Clean or repair
or replace regulator, if necessary.
13.31
DefPMax,
Defrost
A. Tank pressure above 55 psig. A. See Section 13.29.
Pressure
Maximum
13.32
DefPrO,
Defrost
A. Product supply is out during
A. Replenish product supply
Product Out
defrost stage.
(i.e., water, CO
2
, syrup).
13.33
BTR-LO,
A. Product freezing too hard.
A. 1. Check brix and correct, if
Beater Count Low
Beater % below 450.
necessary.
2. Check Level Control and
correct,
if
necessary.
3. Check for restriction of beater
blades.
4. Check for failed beater motor.
B. Bad capacitor on motor.
B. Check capacitor and replace as
required.
C. Motor control board failure.
C. 1. Check connector from Beater
Motor to lower control board.
2. Change lower control board if
necessary.
13.34
SYROUT,
Syrup Out
A. Unit receiving no syrup.
A. Check to see that syrup container
is not empty and is hooked up.
B. Restriction in lines.
B. Assure all lines are free of crimps
or
restrictions.
C. Regulator pressures (unit
C. Check Syrups pressure readouts
and syrup pumps) too low.
for 70-72 psig. Adjust regulators, if
necessary.
D. Syrup Pump failure.
D. Check pump and replace,
if
necessary.
E. Excessive pressure drops
E. Observe “Syrup Press” readouts
in syrup lines.
as chamber fills to verify. Increase
line diameter or relocate syrup
source closer to unit. Syrup
pressures may only be raised (by
increasing
pump
CO
2
pressure) if
separate regulators are installed for
unit and syrup pumps. Never
exceed
pump
manufacturer’s
recommended
maximum
CO
2
inlet
pressure (see Section 12.3).
(Item 13.34 continued on next page.)
TROUBLE CAUSE
REMEDY
NOTE:
For low carbonation applica-
tions, see Quick Reference
Sheet on page 4 for settings
information.
NOTE:
For low carbonation applications,
see Quick Reference Sheet on
page 4 for settings information.
Summary of Contents for FBD562
Page 49: ...49 14 8 LOWER BOARD SCHEMATIC FBD 562 562 ELECTRICAL BOX SCHEMATIC ...
Page 50: ...50 14 9 UPPER BOARD SCHEMATIC FBD 563 563 SCHEMATIC UPPER BOARD ...
Page 51: ...51 14 10 LOWER BOARD SCHEMATIC FBD 563 563 ELECTRICAL BOX SCHEMATIC ...
Page 52: ...52 14 11 UPPER BOARD SCHEMATIC FBD 564 564 SCHEMATIC UPPER BOARD ...
Page 53: ...53 14 12 LOWER BOARD SCHEMATIC FBD 564 564 ELECTRICAL BOX SCHEMATIC LPB1 ...