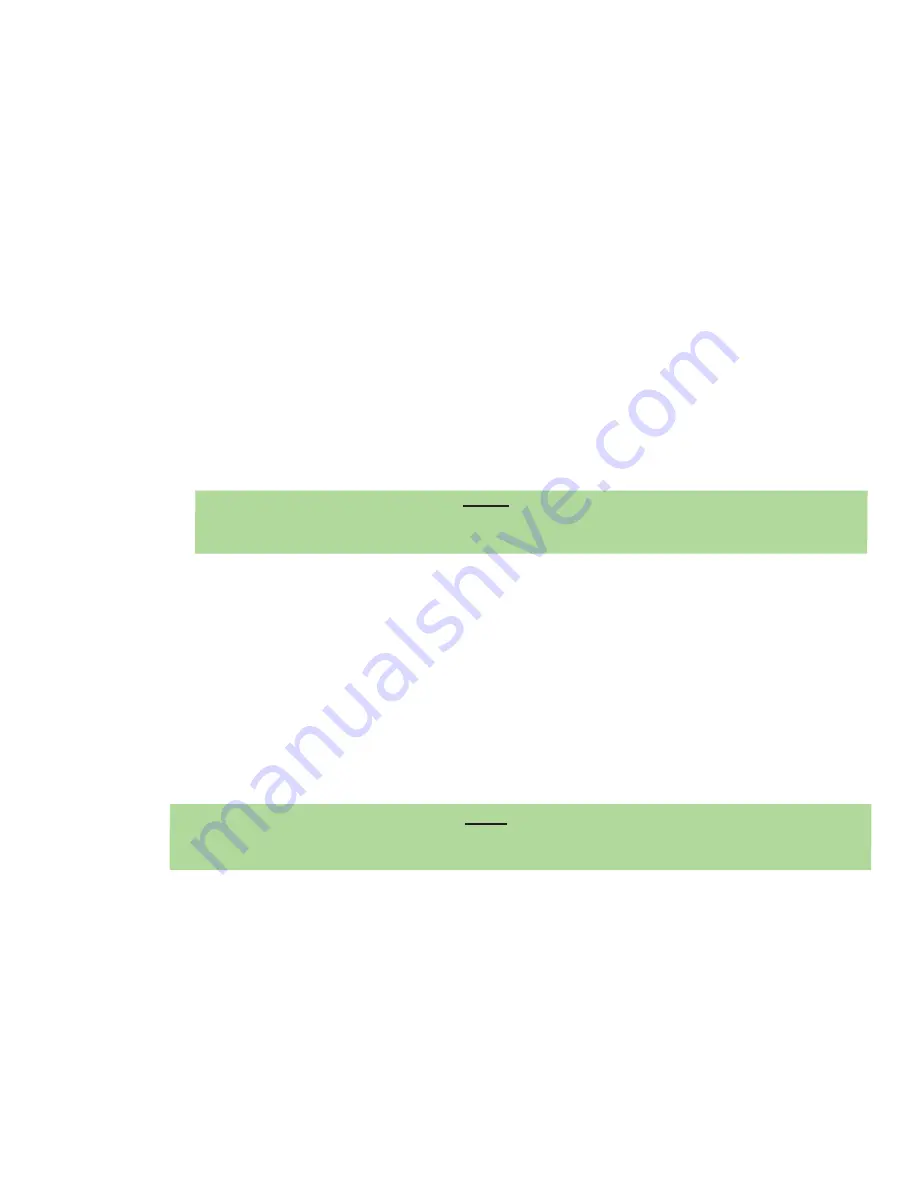
23
L. Again, activate the solution solenoid and allow the chamber to fill
1/2 full
of sanitizing solution.
Deactivate the solution solenoid and turn on beaters. Let solution agitate for
three (3) minutes
.
M. Activate the CO
2
solenoids and evacuate the sanitizing solution from chamber. Then turn off beater,
deactivate the CO
2
solenoids and purge pressure from chamber.
N. Remove sanitizing adapters from the BIB lines and reconnect the lines to the syrup supplies.
O. Turn on water at source.
P. Partially refill the chambers (1/3 full) with syrup and water by activating the solution solenoids. Turn
off the solenoids. Run the beaters for a few seconds.
Q. Drain the product by activating the CO
2
solenoids.
R. Partially refill the chamber again and test the product for off taste. Repeat the drain/fill process until
no off taste exists.
S. When there is no more off taste, fill the unit following the procedure outlined in Section 6.3.
8.5 PREVENTIVE
MAINTENANCE
An annual Preventive Maintenance schedule is recommended by FBD and should include the
following steps.
A. Clean Air Filter – refer to Section 8.6.
B. Check Brix – refer to Section 6.2.
C. Replace rear seals (seals are replaced from the front and do not require removal of the beater
motor).
D. Inspect and replace scraper blades if necessary.
E. Sanitize according to manufacturer’s recommended procedure in Section 8.4.
F. Check all fittings and components for leaks. Repair if necessary.
G. Verify Time, Date, Sleep, and Defrost settings. Adjust as necessary.
NOTE:
Refer to the 56X Series Training Seminar for detailed Preventive Maintenance instructions and
checklist.
8.6
CLEANING THE AIR FILTER
The air filter should be cleaned every 90 days, or more frequently as required by the installation environ-
ment. A dirty air filter can reduce performance of the machine.
A. Open
merchandiser.
B. If the filter protrudes from a slot in the front cover, remove the filter by grasping the edge and sliding
it out. If there is not a slot in the front cover, remove the cover by first removing the screws and then
with the cover removed, use the same procedure listed above to remove the filter.
C. Wash filter with clean water, shake off excess.
D. Allow filter to dry.
E. Reinstall filter and front cover as necessary.
F. Close
merchandiser.
9. BASICS
OF
OPERATION
NOTE
On an initial freeze down, products must be given adequate time to stabilize. Making adjustments too quickly
may negatively affect drink quality.
9.1
MAKING ADJUSTMENTS TO THE FBD56X SERIES UNITS
A. In order to produce a consistent, quality beverage with the FBD56X Series Frozen Beverage
Dispensers, there are a few critical settings that must be maintained. These settings are preset
when you receive the machine from the factory, but, due to variations that occur (e.g., in operating
environments, syrups, and individual machines, etc.), it may be necessary to make minor
adjustments to these critical settings. Adjustments are easily made using the keypad located behind
the door at the front of the machine, or by adjusting the CO
2
regulator located behind the access
panel below the keypad.
B.
The settings that control product quality and production rate are:
1. Beverage Syrup Content or Brix Level (Set on Syrup Flow Control)
2. Chamber “Level Control”
3. Regulated
CO
2
Injection Pressure
4. Freeze and Thaw Settings
Summary of Contents for FBD562
Page 49: ...49 14 8 LOWER BOARD SCHEMATIC FBD 562 562 ELECTRICAL BOX SCHEMATIC ...
Page 50: ...50 14 9 UPPER BOARD SCHEMATIC FBD 563 563 SCHEMATIC UPPER BOARD ...
Page 51: ...51 14 10 LOWER BOARD SCHEMATIC FBD 563 563 ELECTRICAL BOX SCHEMATIC ...
Page 52: ...52 14 11 UPPER BOARD SCHEMATIC FBD 564 564 SCHEMATIC UPPER BOARD ...
Page 53: ...53 14 12 LOWER BOARD SCHEMATIC FBD 564 564 ELECTRICAL BOX SCHEMATIC LPB1 ...