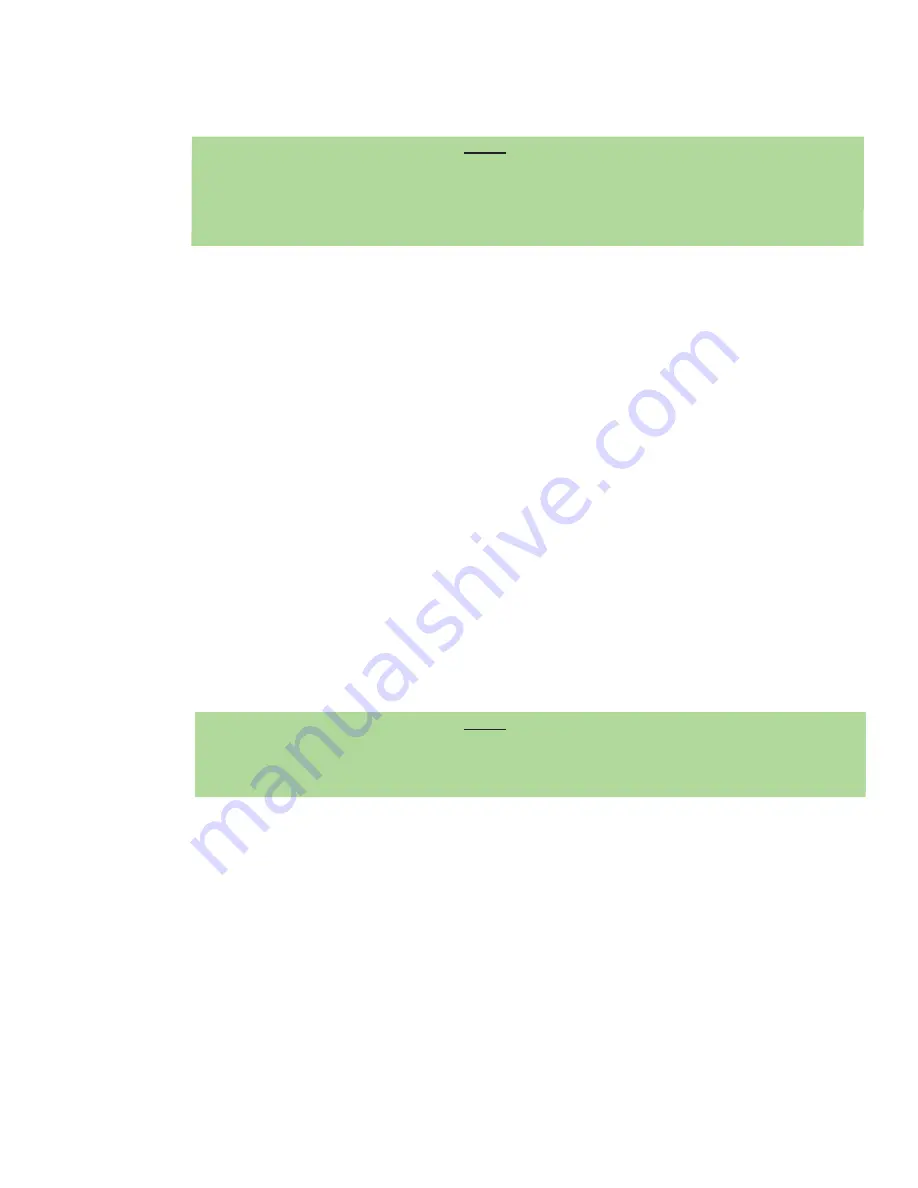
13
K. Measure the brix with a refractometer. Set brix to between 13.5 and 15.0 by adjusting the syrup
brix flow controller
clockwise to increase brix level or counter-clockwise to decrease brix level. If
the brix requires adjustment, discard a sample before checking the brix again.
NOTE
Do not adjust the brix with the water flow control setting unless you are unable to obtain the desired
brix with adjustments to the syrup flow control.
Brix reading is affected by temperature. Samples taken from the chamber should be at the same
temperature as from the sample valve.
L. Repeat steps I, J, and K for other chambers.
6.3
FILLING THE CHAMBER
A. Access “CO
2
SOL” by going to the “SERVICE MENU\MANUAL ON/OFF” section of the service
menu.
B. Displace the air in the chamber with CO
2
by activating the CO
2
solenoid.
1. Pull and hold the relief ring until the escaping, rushing air sound almost stops; then release the
ring. Allow the pressure to rebuild in the tank.
2. Repeat this procedure at least two more times until the air has been displaced by the CO
2
.
Remember to deactivate the CO
2
solenoid upon completion.
C. Repeat steps A and B above for the other chambers.
Remember to deactivate the CO
2
solenoid
upon completion.
D. With CO
2
in the chamber, press a “FILL” button to begin filling the chamber with product. If the
chamber does not fill, gently pull the Relief Ring until filling begins and then release. As the cham-
ber fills, the pressure in the chamber will increase until it rises above the psi fill point. At this point,
the chamber will stop filling and the LCD will readout “Fill Hold”. It will then be necessary to pull
the relief ring to relieve the pressure and allow filling to continue. Slowly pull the relief ring until the
pumps activate, then release. Repeat the venting process
until the chamber is 90% full (level
with relief valve), then press Fill button to turn OFF. Fill one (1) chamber at a time.
E. Repeat steps A, B, C, and D for the remaining chambers.
F. Press the “DEFROST” and then the “RUN” buttons on both sides of the control panel to begin
the freezing process. The beater motors will begin to run but the compressor
will wait for
two (2) minutes before starting.
After the two (2) minute waiting period, the machine will defrost
and then begin the freeze cycle.
G. After an initial freeze down, the product will be frozen and ready to dispense.
NOTE
On an initial freeze down, products must be given adequate time to absorb CO
2
. Until CO
2
is
properly and adequately absorbed, drinks could be too “wet” or too “heavy”. If adjustments are
necessary, refer to section 9.
H. Re-check
CO
2
, Water, and Syrup lines for leaks.
Summary of Contents for FBD562
Page 49: ...49 14 8 LOWER BOARD SCHEMATIC FBD 562 562 ELECTRICAL BOX SCHEMATIC ...
Page 50: ...50 14 9 UPPER BOARD SCHEMATIC FBD 563 563 SCHEMATIC UPPER BOARD ...
Page 51: ...51 14 10 LOWER BOARD SCHEMATIC FBD 563 563 ELECTRICAL BOX SCHEMATIC ...
Page 52: ...52 14 11 UPPER BOARD SCHEMATIC FBD 564 564 SCHEMATIC UPPER BOARD ...
Page 53: ...53 14 12 LOWER BOARD SCHEMATIC FBD 564 564 ELECTRICAL BOX SCHEMATIC LPB1 ...