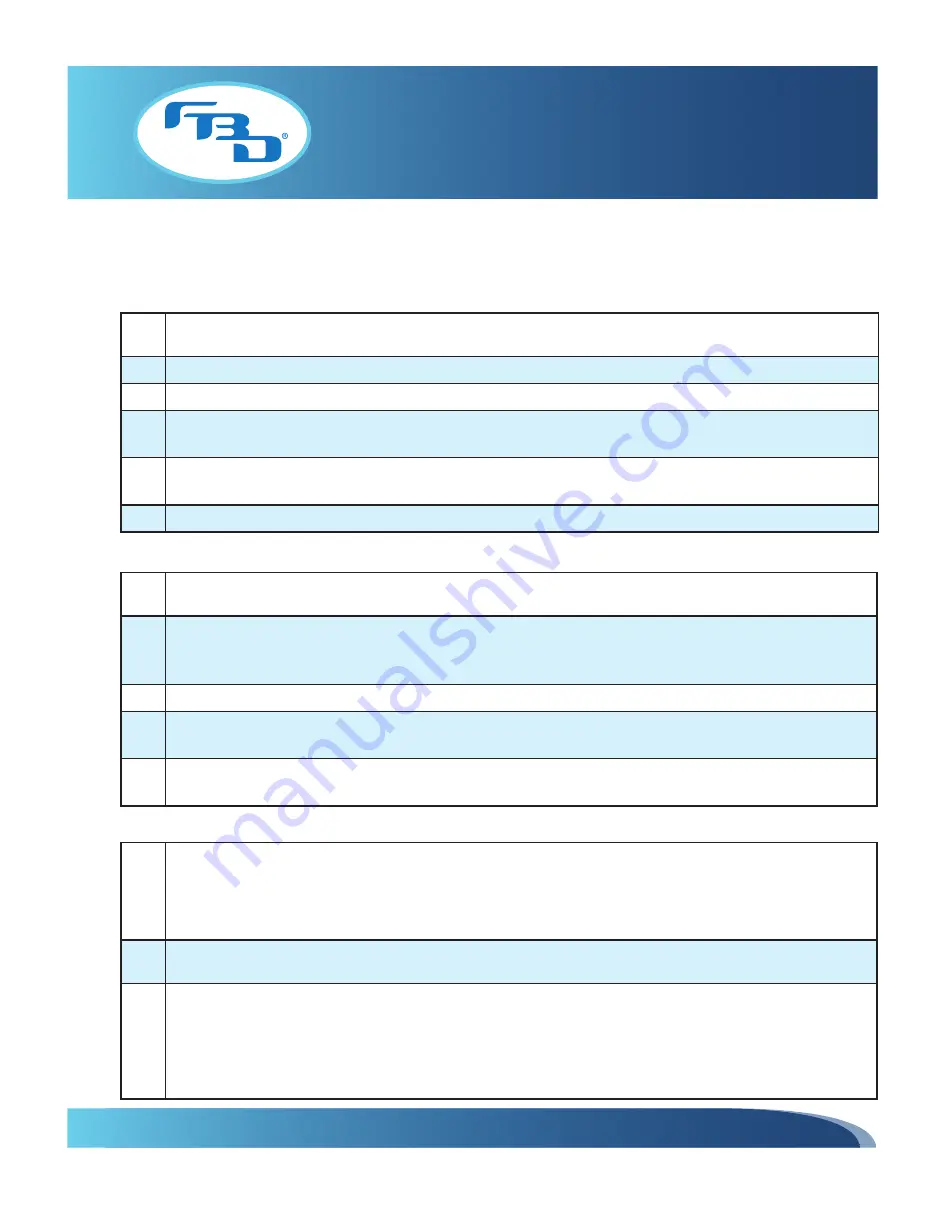
77X INSTALLATION & OPERATION MANUAL
771/772/773/774 MODELS
48
10.3 Diagnostic Fault Codes
The following codes are faults that can be displayed after running a diagnostic sequence.
Error #500: Fan Not Turning On
Error #510: Compressor Not Turning On
If compressor still won’t start:
1
Remove control board and check for a blown fan fuse (F1 and F2).
A fan or capacitor malfunction may be caused by a blown fuse.
2
If fuses are OK, reinstall control board.
3
Disconnect wiring harnesses at fan capacitor.
4
Manually turn fan on and check for line voltage (230V) between the connectors removed from the
capacitor. If no voltage is present then replace control board.
5
If correct voltage is present then substitute a “known to be good” capacitor and try to operate fan
again.
6
If fan fails to start with working capacitor then replace both fan and capacitor.
1
Manually turn on the compressor using the menu and ensure the contactor located in the
electrical box engages.
2
If contactor does not engage, check for 24 VAC at the contactor coil (the voltage will read ~19 VAC
when not powered). Refer to the wiring schematic for details. If no voltage, install a new control
board and check for 24 VAC again.
3
If 24 VAC is present at the contactor coil but it does not engage, then replace the contactor.
4
If contactor engages, check to make sure the voltage at contactor terminals T1 and T2 is above
187V when the compressor is starting. If below 187V, the line voltage supply needs to be corrected.
5
If voltage at T1 and T2 is good, substitute a “known to be good” run capacitor. If compressor starts,
replace the original run capacitor.
6
Remove the wires from the compressor and check for continuity between the C-R, C-S and R-S
terminals of the compressor. If the compressor is hot, a lack of continuity can indicate a tripped
thermal protector. It may take considerable time for the compressor to cool down and reset the
protector. If continuity cannot be established through all motor windings when cooled down, the
compressor should be replaced.
7
Check the compressor motor for a ground fault by conducting a continuity check between the
common terminal (C) and the compressor shell. If there is continuity then replace the compressor.
8
Check the compressor motor windings for proper resistance using the “Compressor Winding
Resistance” table in this section. The specifications are provided for a compressor at 75° F (24
°
C). If
the compressor has been recently running or has recently overheated, then the resistance readings
will be higher. Wait until the compressor cools down (this may take over an hour) before using the
resistance read out for any diagnostic purpose. If the cold resistance is out of spec, then replace
the compressor.