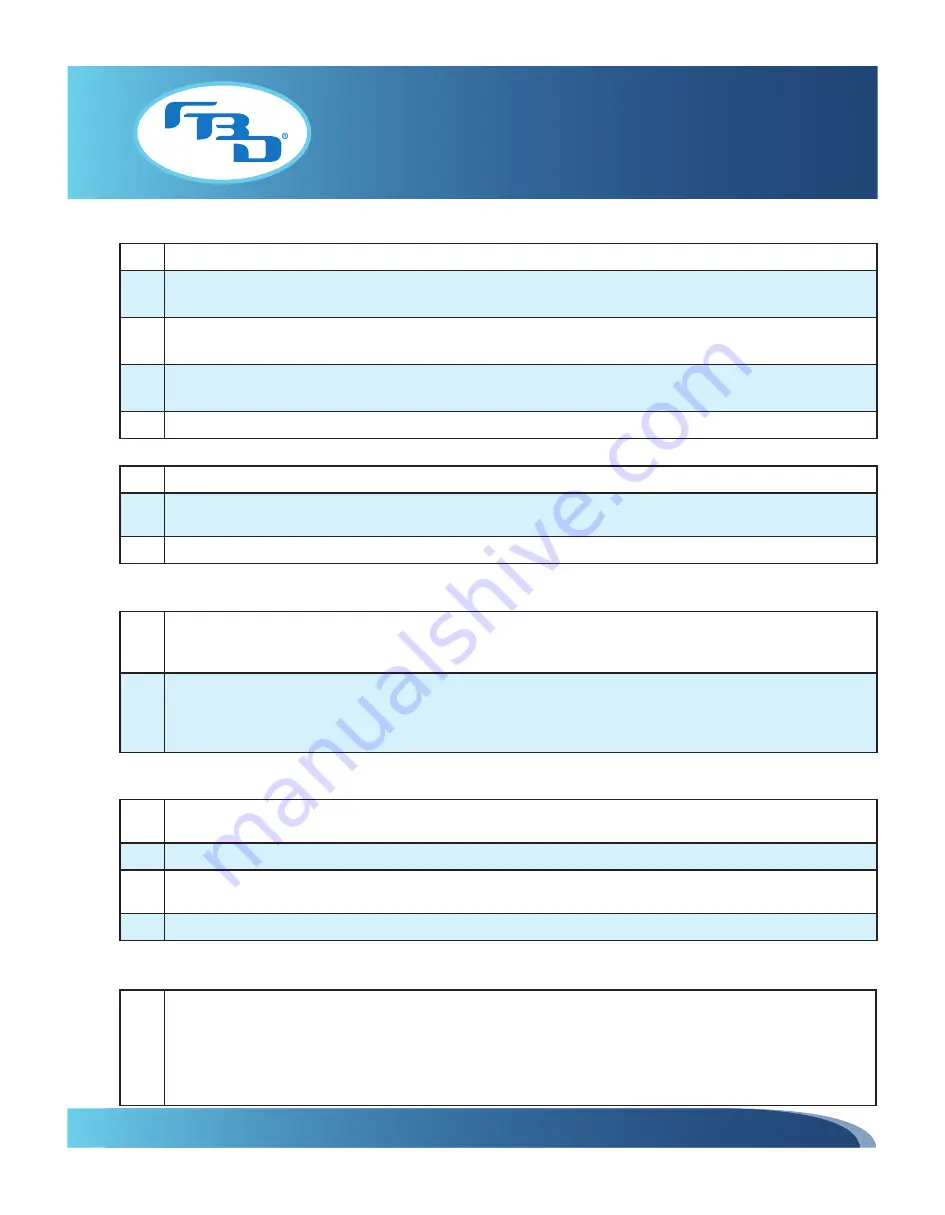
77X INSTALLATION & OPERATION MANUAL
771/772/773/774 MODELS
50
Error #591, 592, 593, 594: Gas Solenoid Not Opening
Error #601, 602, 603, 604: Solution Solenoid Not Opening
Error #611, 612, 613, 614: Gas or Solution Leak
The barrel pressure is rising during a fill circuit diagnostic test.
Error #621, 622, 623, 624: Barrel Leak
The barrel pressure is dropping during a fill circuit diagnostic test.
Error #630: Refrigeration Pressure Transducer Offset
The pressure transducers were not reading correctly during the refrigeration diagnostic test.
1
Disconnect the electrical harness from the gas solenoid for the barrel in question.
2
Manually activate the solenoid and check to make sure there is 12 VDC at the connection (the
voltage will read ~2 VDC when not powered). If no voltage, then replace the control board.
3
If correct voltage is present, replace the solenoid. Be sure to turn off the gas supply before
disconnecting the gas line from the solenoid.
4
If solenoid is functioning properly, then a leak may be present in the product delivery system.
Check the relief valve, dispensing valve, rear seal and tubing in the product tray for leaks.
5
If no leaks are found, then the tank pressure transducer may be defective.
1
Disconnect the electrical harness from the suspect solution solenoid.
2
Manually activate the solenoid and check for 24 VAC at the connection (the voltage will read ~19
VAC when not powered). If no voltage, then replace the control board.
3
If correct voltage is present, remove the solution module and replace the solenoid.
1
Determine if the barrel is filling with gas or liquid. If the barrel liquid level is low enough, use a
flashlight to look at the back of the barrel and see if liquid is entering the barrel. Replace a leaking
solenoid.
2
Ensure the solenoids are not manually turned on by going to the MANUAL ON/OFF menu. Check
to see if either solenoid is receiving power by removing the leads and testing with a voltmeter. If 12
VDC is measured on the gas solenoid, or 24 VAC is measured on the solution solenoid, then replace
the control board.
1
Look for any obvious leaks by searching for liquid along the product line from the solution module
to the back of the barrel.
2
Inspect the rear seal to determine if the leak is originating from it.
3
Inspect the relief valve in the faceplate to determine if the leak is originating from it. Press and turn
the relief valve to firmly seat.
4
Inspect the dispensing nozzle to determine if the leak is originating from it.
1
The low side pressure on the gauges should be within approximately 5 PSIG (34 kPag) of the
readout on the LCD screen. The high side pressure on the gauges will typically read 20 PSIG (138
kPag) higher (while the compressor is running) than the readout on the LCD screen due to the
pressure drop through the condenser. Replace the pressure transducer that is reading incorrectly;
however, do note that the high side pressure transducer is used for diagnostic purposes only (it is
not necessary for the standard operation of the dispenser).