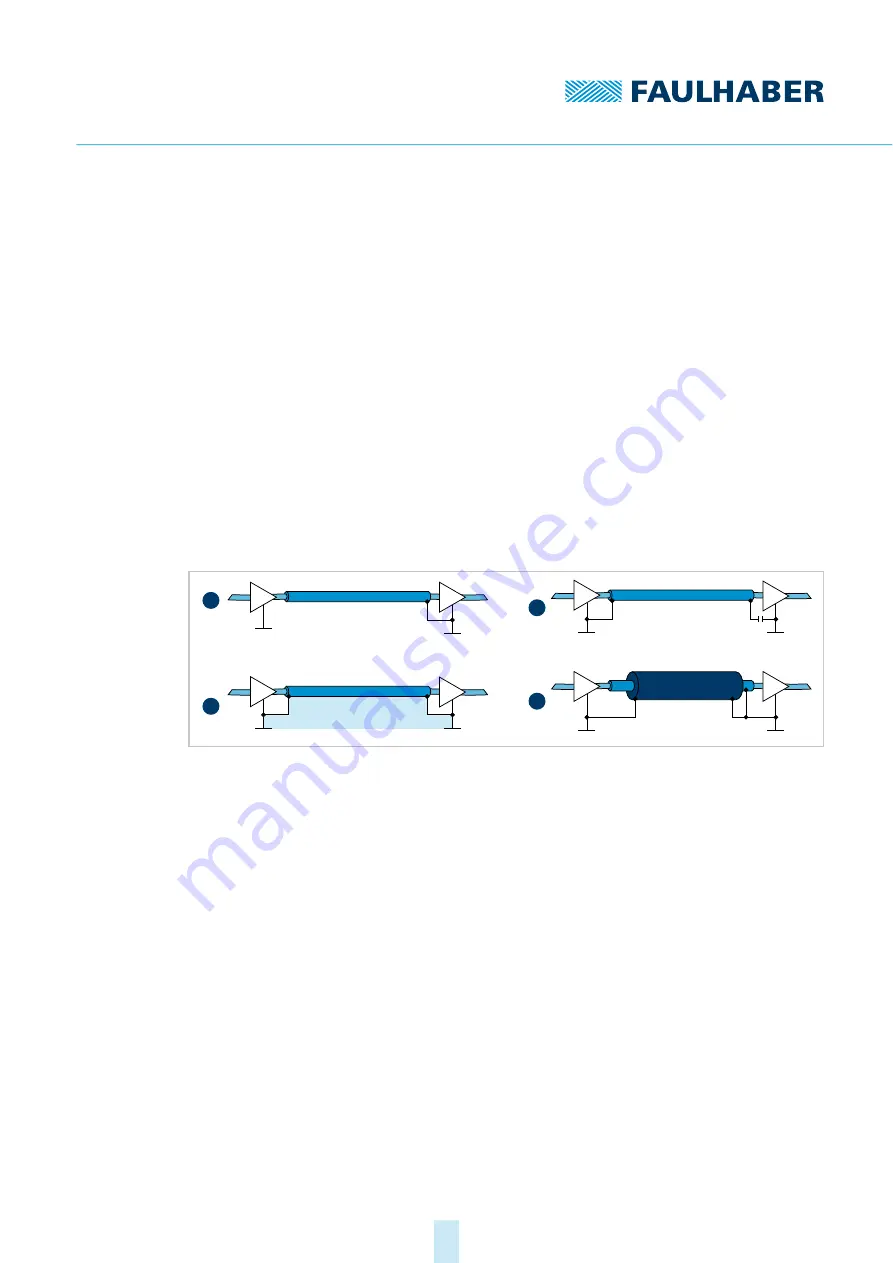
6th edition, 22.05.2023
7000.05060, 6th edition, 22.05.2023
7000.05060
Installation
47
4.3.4
Shielding
Shield cables in all cases.
Shield cables that are longer than 3 m with tightly meshed copper braiding.
Shield all supply lines according to current guidelines/standards (e.g., IPC-A-620B) and
connect using (round) shield clamp.
In special cases (e.g., with pigtail) or after qualification, the shield can be omitted for
the following cables:
Cables with length <50 cm
Cables with low power supplies (e.g., <20 V)
Sensor cables
Connect shield clamps to a low-impedance (<0.3
Ω
) grounding bar or grounding plate.
Establish a star-point earth connection (see chap. 4.3.2, p. 45).
Lay the motor phases in a shield, separate from the sensor or encoder signals, and con
-
nect on at least the motor side (see 1 or 2 in Fig. 33).
Fig. 33: Various possibilities for the shield connection
The sensor signals can optionally be laid with the motor phases in a shared cable/insula
-
tion hose using another outer braided shield. This outer braided shield must be con
-
nected at both ends (e.g., 4 in Fig. 33). A solution such as 2 in Fig. 33 is not functional in
every case for this configuration. If this is not possible by means of a ground offset,
establish the RF connection via specially suited capacitors (e.g., safety capacitors such as
Y1/Y2/X1/X2, see 3 in Fig. 33). In this case, do not connect the shield multiple times
except at the motor connection and controller side.
1
Suppressing electrical fields
2
Alternating magnetic field
3
Interruption of the ground loop for direct currents or low-frequency currents
4
Discharging parasitic currents to the reference potential
1
2
3
4