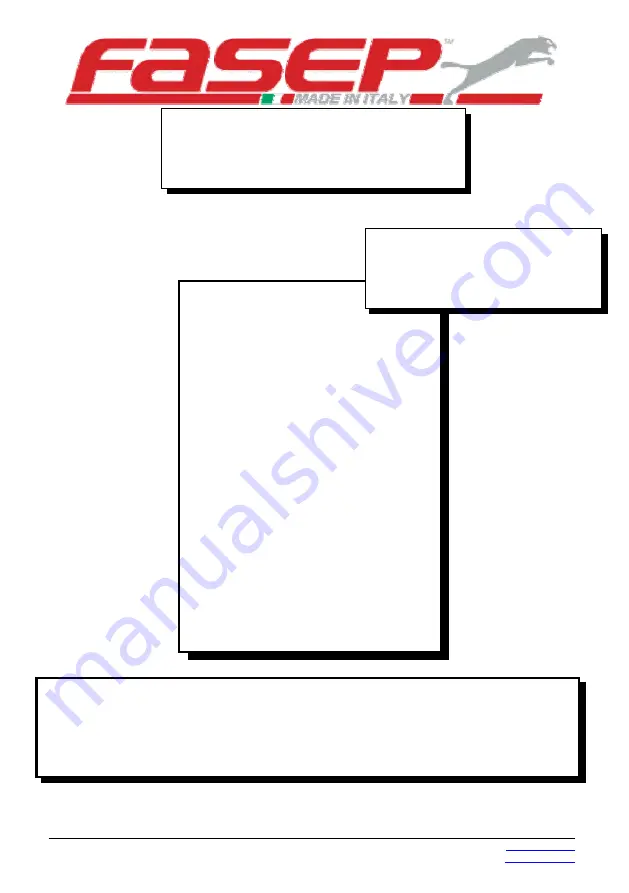
Qualcuno di cui ti puoi fidare
(Someone you can trust)
{
FASEP 2000 srl
Via Faentina, 96
50030 Ronta (Fi) Italy
Sistema Qualità Certificato ISO 9001:2000
Tel
+39 055 8403126
Fax
+39 055 8403354
WWW
www.fasep.it
˜
FASEP 2000 srl
Via Faentina, 96
50030 Ronta (Fi) Italy
Sistema Qualità Certificato ISO 9001:2000
l
i
a
m
-
E
6
2
1
3
0
4
8
5
5
0
9
3
+
l
e
T
W
W
W
4
5
3
3
0
4
8
5
5
0
9
3
+
x
a
F
www.fasep.it
Instruction Manual - ENG
Version 1.0 - January 2014
RASE.3030
TYRE CHANGER
Summary of Contents for RASE.3030
Page 4: ......
Page 18: ...18 User manual 8a Z1 Z6 Z7 Z8 Z2 Z3 Z4 Z5 Optional accessories supplied on request...
Page 19: ...User Manual 19 8b Z2 Z3 Z5 Z4 Z6 Z1 A...
Page 20: ...20 User manual 8c Z2 Z3 Z5 Z4 Z1 B...
Page 21: ...User Manual 21 8d C Z5 8e Z8 Z6 Z7 Z1 D...
Page 22: ...22 User manual 8f E...
Page 23: ...User Manual 23 8g F...
Page 48: ...48 User manual 35 a b c e d x...
Page 58: ...58...
Page 59: ......
Page 60: ......