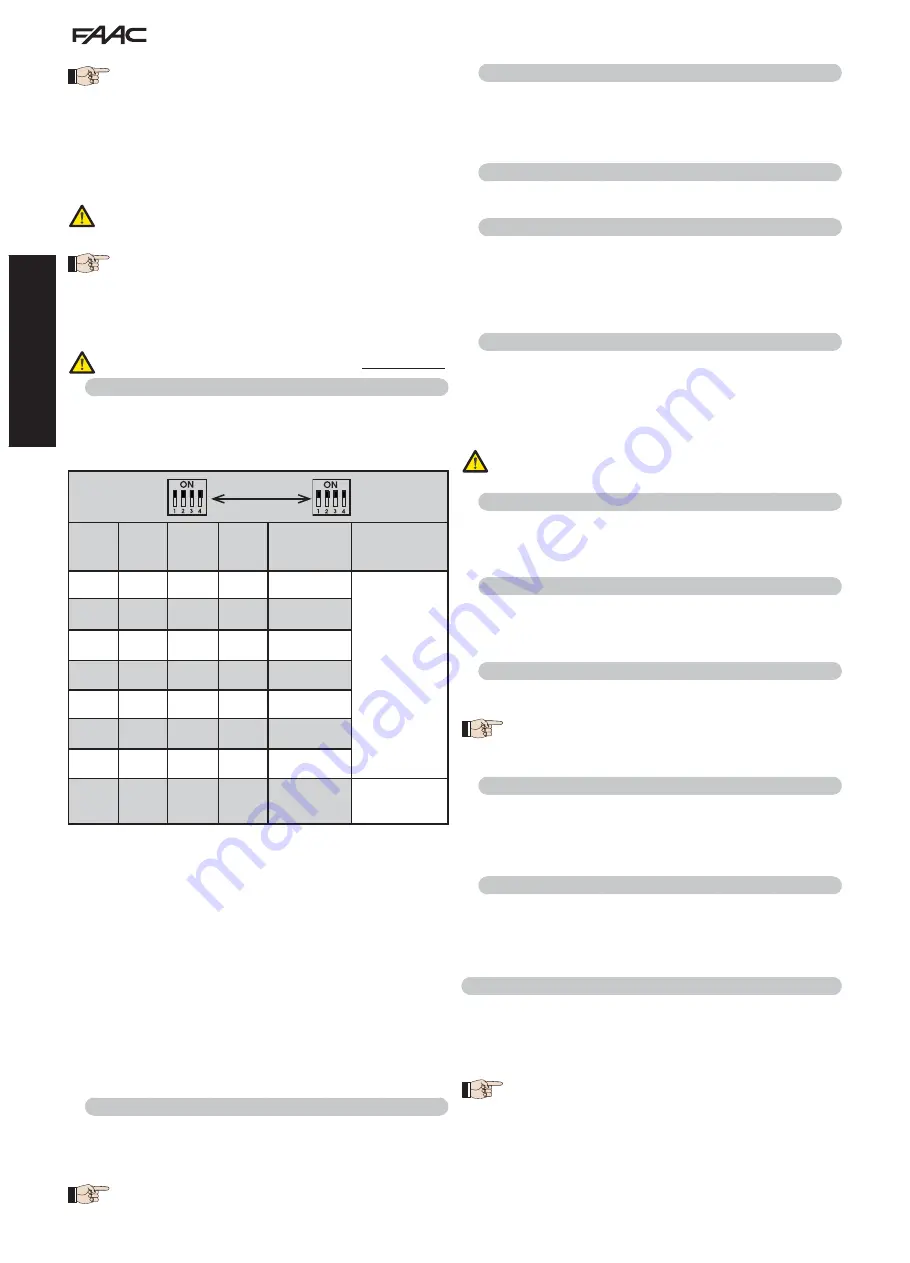
8
ENGLISH
Dip 1 Dip 2 Dip 3 Dip 4
Pair
no.
Type
ON
OFF
OFF
OFF
1° Pair
CLOSE
photocells
ON
OFF
OFF
ON
2° Pair
ON
OFF
ON
OFF
3° Pair
ON
OFF
ON
ON
4° Pair
ON
ON
OFF
OFF
5° Pair
ON
ON
OFF
ON
6° Pair
ON
ON
ON
OFF
7° Pair
ON
ON
ON
ON
Single
OPEN
PULSE
DIP-SWITCH
T X
DIP-SWITCH
R X
SAME
ADDRESS
BUS photocells do not require a matching polarity
connection.
The 8 pairs of photocells feature the following functions:
Pairs of closing photocells:
max 7
Pairs of OPEN pulse photocells:
max 1
After positioning the BUS technology photocells, it is necessary
to proceed with selecting the address for each pair using various
combinations of the DIP-SWITCHES located on each photocell.
Set the SAME DIP-SWITCH ADDRESS chosen both on
the transmitter and receiver of the same pair.
Ensure that two or more pairs of photocells do not have
the same address. If no BUS accessories are used, leave
terminals 1 and 2 free.
The following table describes how to set the dip-switches located
inside the transmitter and receiver of the BUS photocells.
Addressing BUS photocell PAIRS
To allow operation of the installed BUS accessories,
store them on the board as described in paragraph 5.3.
4.2 Terminal board J2 (outputs)
OUT 1 - Output 1 open-collector GND (terminal 13):
The output
can be set in one of the functions described in the Advanced
Configuration (par. 6). The default value is
04
- Beam OPEN or in
PAUSE
.
Maximum load: 24 VDC with 100 mA.
OUT 2 - Output 2 open-collector GND (terminal 15):
The output can
be set in one of the functions described in the Advanced Configuration
(par. 6). The default value is
03
- CLOSED BEAM.
Maximum load:
2
4 VDC with 100 mA.
OUT 3 - Output 3 open-collector GND (terminal 17):
The output can
be set in one of the functions described in the Advanced Configuration
(par. 6). The default value is
19
- WARNING LAMP.
Maximum load:
24 VDC with 100 mA.
OUT 4 - Relay output 4 (terminals 19, 20, 21):
The output can be
set in one of the functions described in Advanced Configuration (par.
6). The default value is
01
- BEAM ILLUMINATION.
Maximum load:
24 VDC with 800 mA.
4.3 Terminal board J3 (external fl ashing lamp)
LAMP:
to these terminals you can connect a 24VDC FAACLED
external flashing lamp.
The integrated flashing traffic light must be
connected independently to connector J15.
The 24V FAACLIGHT with incandescent lamp cannot be
connected to the J3 connector
4.4 Terminal board J4 (loop detector)
LOOP 1:
magnetic loop LOOP 1 (OPEN, terminals 24-25): for
OPENING.
LOOP 2:
magnetic loop LOOP 2 (SAFETY/CLOSE, terminals 26-27):
for
SAFETY/CLOSING.
4.5 Connector J5 (Motor)
Rapid connector for connecting the motor.
4.6 Connector J7 (Encoder)
The B680H barrier is equipped with a device for detecting the opening
angle/bar position to ensure greater anti-crushing safety thanks to
the possibility of reversing the direction of movement the moment in
which an obstacle is detected. This device interfaces with the board
through connector J7.
4.7 Connector J10 (Radio)
Used for the rapid connection of the Minidec, Decoder and RP / RP2
Receivers (see Fig. 28). If a 2-channel receiver is used, like the RP2,
it will be possible to directly command automated system OPEN and
CLOSE from a 2-channel radio control. If a 1-channel receiver is used,
like the RP, it will only be possible to command OPEN.
Boards should be inserted and removed ONLY after
having cut off electrical power
4.8 Connector J11 (Beam break-out sensor)
Designed for connecting the break-out sensor for the pivoting beam
(if present). The sensor is optional. If it is not present,
do not remove
the installed jumper.
4.9 Connector J12 (Emergency battery)
This connector is for connecting a battery (optional) for ensuring
automated system operation in case of temporary cut off of the main
power supply.
4.10 Connector J13 (36VDC Power Supply)
This factory-wired connector powers the E680 board.
The terminal shown in Fig. 1 ref. a must be connected
to the system earth by the installer during the electrical
connection operations.
4.11 Connector J15 (fl ashing traffi c light)
This connector is for connecting the flashing traffic light built into
the barrier head. The flashing traffic light visually signals barrier
movement and, if needed, regulate access to the property using
traffic light signals.
4.12 Connector J16 (beam lights)
Connector which allows the rope light for the rod to be connected,
providing visual warning of barrier movement. The connector has a
common GND connection and two +36V (BLR / BRG) outputs. The
default value is 02 - “BEAM LIGHTING TYPE 2” for OUT 5, 04 - “BEAM
OPEN OR PAUSED” for OUT 6.
5. PROGRAMMING
The E680 board features 3 programming levels that make it entirely
configurable and allow it to adapt the logics to any use.
Each of the three levels can be accessed through a specific key
combination.
Changes to the confi guration parameters become
effective immediately, while final storage occurs
only upon exiting confi guration and returning to the
automated system status display. If the equipment is
powered down before returning to the automated system
status display, all changes made will be lost.
Summary of Contents for B680
Page 1: ...B680H...
Page 2: ......
Page 30: ...28 Fig 17 Fig 17 L...
Page 31: ...29 Fig 18 Fig 18 Fig 19 Fig 19 1 2 Fig 20 Fig 20...
Page 32: ...30 Fig 21 Fig 21...
Page 35: ...33 Fig 31 Fig 31...
Page 36: ...34 Fig 32 Fig 32...
Page 41: ...5 1 2 Fig 18...