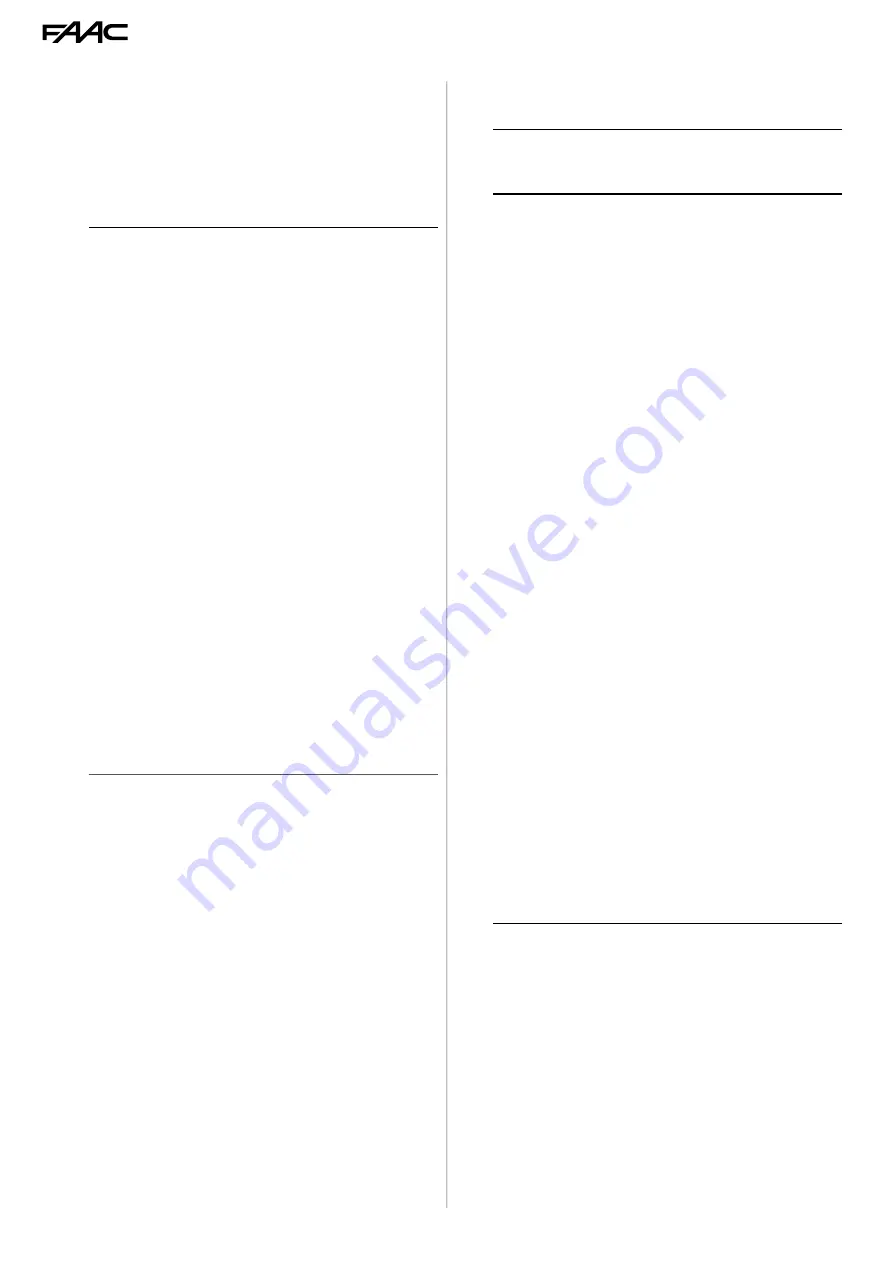
422 10
732870 - Rev.C
4.1 MECHANICAL REQUIREMENTS
4. INSTALLATION REQUIREMENTS
4.2 ELECTRICAL SYSTEM
The mechanical structural components must comply with the require-
ments of EN 12604. Before installing the automation, the suitability
of the mechanical requirements must be established and any work
that is necessary in order to meet them carried out.
The essential mechanical requirements are as follows:
!
Flat, horizontal paving in the area of movement of the leaf.
The structure (columns, hinges and leaves) must be solid and there must be
no risk of detachment or collapse, (considering the weight of the leaf and
the forces applied by the door actuator and wind action). Perform structural
calculations where necessary.
The structure must show no signs of corrosion or cracking.
The hinges must be in good condition, lubricated and with no play or friction.
The leaf must remain vertical throughout the entire length of travel, with a
regular, smooth and uniform movement.
Appropriate devices must be installed to prevent the leaf from falling.
Presence of external mechanical limit stops to limit the travel of the leaf when
opening and closing. The stops must be suitably sized and solidly fastened
so that they resist any impact of the leaf in the event of improper use (leaf
pushed and left to slide freely). The thresholds and protrusions of the paving
must be appropriately shaped in order to prevent the risk of sliding or slipping.
Presence of a safety area between the wall (or other fixed element) and the
furthest protruding part of the open leaf, to protect against the risk of persons
becoming trapped/crushed. Alternatively, check that the opening force
required falls within the maximum permissible limits according to applicable
standards and legislation.
Presence of safety areas between the fixed and moving parts, to protect
against the risk of hands being trapped. Alternatively, apply protective
elements that prevent fingers from being introduced.
Presence of a safety area between the floor and lower edge of the leaf, along
its entire stroke, to protect feet from becoming caught and crushed. Alterna-
tively, apply protective elements preventing the introduction of feet.
No sharp edges or protruding parts should be present to ensure there are no
cutting, hooking or perforation hazards. Alternatively, eliminate or protect
any sharp edges and protruding parts.
For the minimum dimensions to prevent crushing/shearing of body parts,
refer to EN 349. For the safety distances required to prevent danger zones
being reached, refer to ISO 13857.
F
Always shut off the power supply before performing any work. If the
disconnect switch is not in view, apply a warning sign stating “WARNING -
Maintenance in Progress”.
!
The electrical system must comply with applicable legislation in the country
of installation.
Use components and materials with CE marking which are compliant with the
Low Voltage Directive 2014/35/EU and EMC Directive 2014/30/EU.
The power supply line for the automation must be fitted with a multi-pole cir-
cuit breaker, with a suitable tripping threshold, a contact opening distance of
at least 3 mm and a breaking capacity that complies with current regulations.
The power supply for the automation must be fitted with a 30 mA differential
switch.
The metal parts of the structure must be earthed.
Check that the protective earthing system complies with applicable regula-
tions in the country of installation.
The electrical cables of the automation system must be of a size and insulation
class that is compliant with current legislation and laid in appropriate rigid
or flexible conduits, either above or below ground.
Use separate conduits for the power supply and the 12-24 V control devices
/ accessories cables.
Check buried cable plans to ensure that there are no other electrical cables
in proximity to the planned digging/drilling locations to prevent the risk of
electrocution.
Check that there are no pipes in the vicinity as well.
The external electronic board must be housed in an enclosure that has a
minimum IP 44 protection rating and fitted with a lock or another type of
device to prevent access by unauthorised persons. The enclosure must be
located in an accessible and non-hazardous area and at least 30 cm from the
ground. The cable outlets must face downwards.
The conduit fittings and the cable glands must prevent the entry of moisture,
insects and small animals.
Protect extension connections using junction boxes with an IP 67 protection
rating or higher.
It is recommended to install a flashing light in a visible position to indicate
when it is moving.
The control accessories must be positioned in areas that are always accessible
and not dangerous for the user. It is recommended to position the control
accessories within the field of view of the automation.
If an emergency stop button has been installed, it must be EN13850 compliant.
Comply with the following heights from the ground:
- control accessories = minimum 150 cm
- emergency buttons = maximum 120 cm
If the manual controls are intended to be used by disabled or infirm persons,
highlight them with suitable pictograms and make sure that these users are
able to access them.
Summary of Contents for 422 Standard
Page 1: ...422 Translation of the original instructions...
Page 26: ...422 24 732870 Rev C...
Page 27: ...422 25 732870 Rev C...