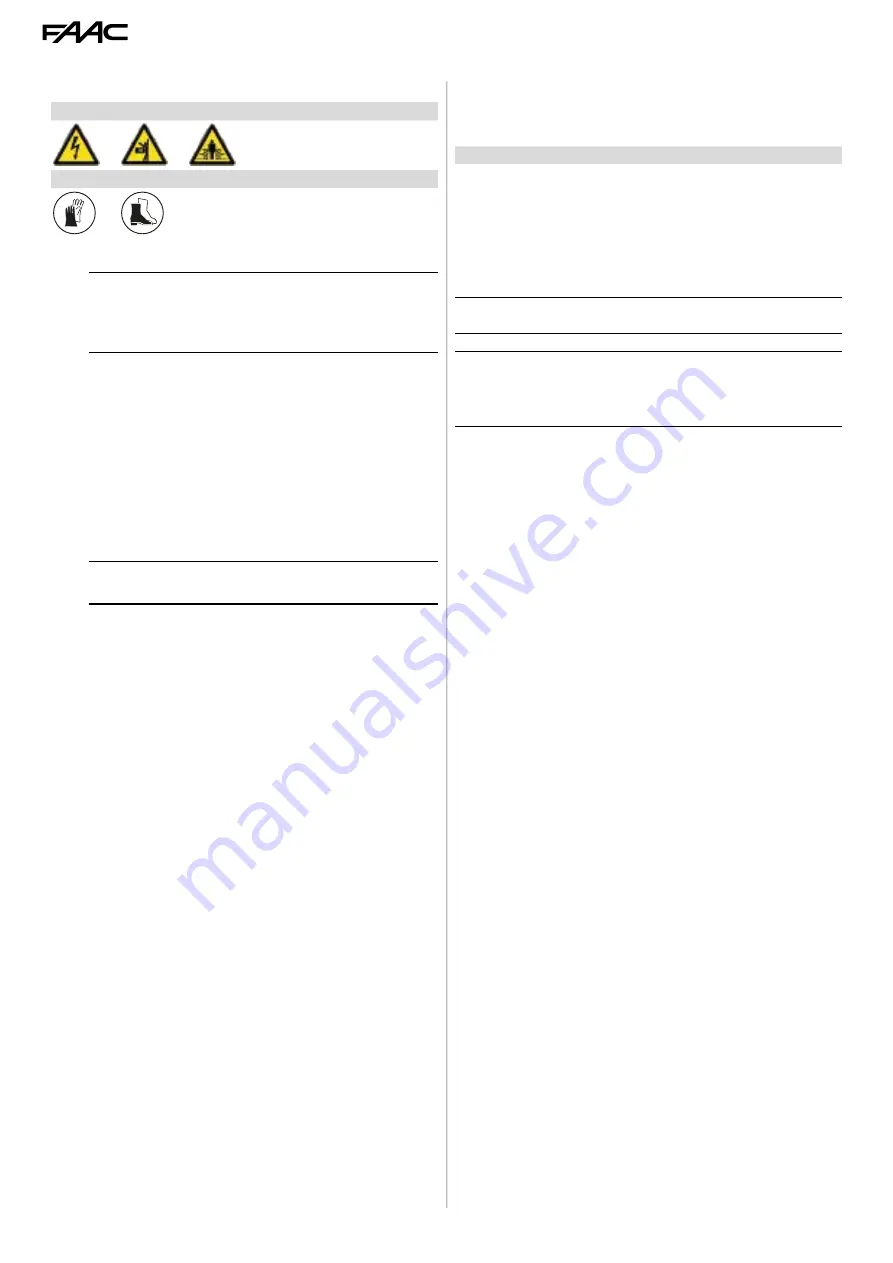
422 18
732870 - Rev.C
9. MAINTENANCE
RISKS
PERSONAL PROTECTIVE EQUIPMENT
9.2 OPERATIONAL PROBLEMS
8
Troubleshooting
CONDITION
FINDING SOLUTIONS
No movement
Check that the actuator is not released
Check that there is power
Check the motor connection
Check the adjustment of the by-pass screws
Check the connection and operation of the thrust
capacitor
Check the operation of the electronic equipment
The gate CLOSES rather than OPEN-
ING and vice versa
Invert the phases of the motor connection
Slow movement
Check the adjustment of the by-pass screws
Irregular movement
Check that the breather screw has been removed
Move the gate several times to purge any air that
may be present in the piston
Check the installation measurements
F
Before performing any maintenance, disconnect the mains power supply. If
the disconnecting switch is not visible, apply a "ATTENTION - Maintenance in
progress" sign. Restore the power supply once maintenance is complete
and after tidying up the area.
!
Maintenance must be performed by the installer/maintenance technician.
Comply with all the safety instructions and recommendations provided in
this manual.
Close off the work site and prevent access/transit. Do not leave the work site
unattended.
The work area must be kept tidy and clear upon completing maintenance.
Before starting activities, wait for the components subject to heating to
cool down.
Do not modify the original components in any way.
FAAC S.p.A. disclaims any liability for damage caused by components that are
modified or tampered with.
L
i
The warranty shall be forfeited in the event of tampering with components.
For replacements, use only original spare parts FAAC.
9.1 ROUTINE MAINTENANCE
The Scheduled Maintenance table
(
1 9
) lists the operations
that must be performed on a regular basis in order to keep the auto-
mation system working reliably and safely; these are given purely as
a guideline and should not be considered exhaustive. The installer/
machine manufacturer is responsible for drawing up the maintenance
plan for the automation, supplementing this list or modifying the
maintenance intervals according to the machine characteristics.
Summary of Contents for 422 Standard
Page 1: ...422 Translation of the original instructions...
Page 26: ...422 24 732870 Rev C...
Page 27: ...422 25 732870 Rev C...