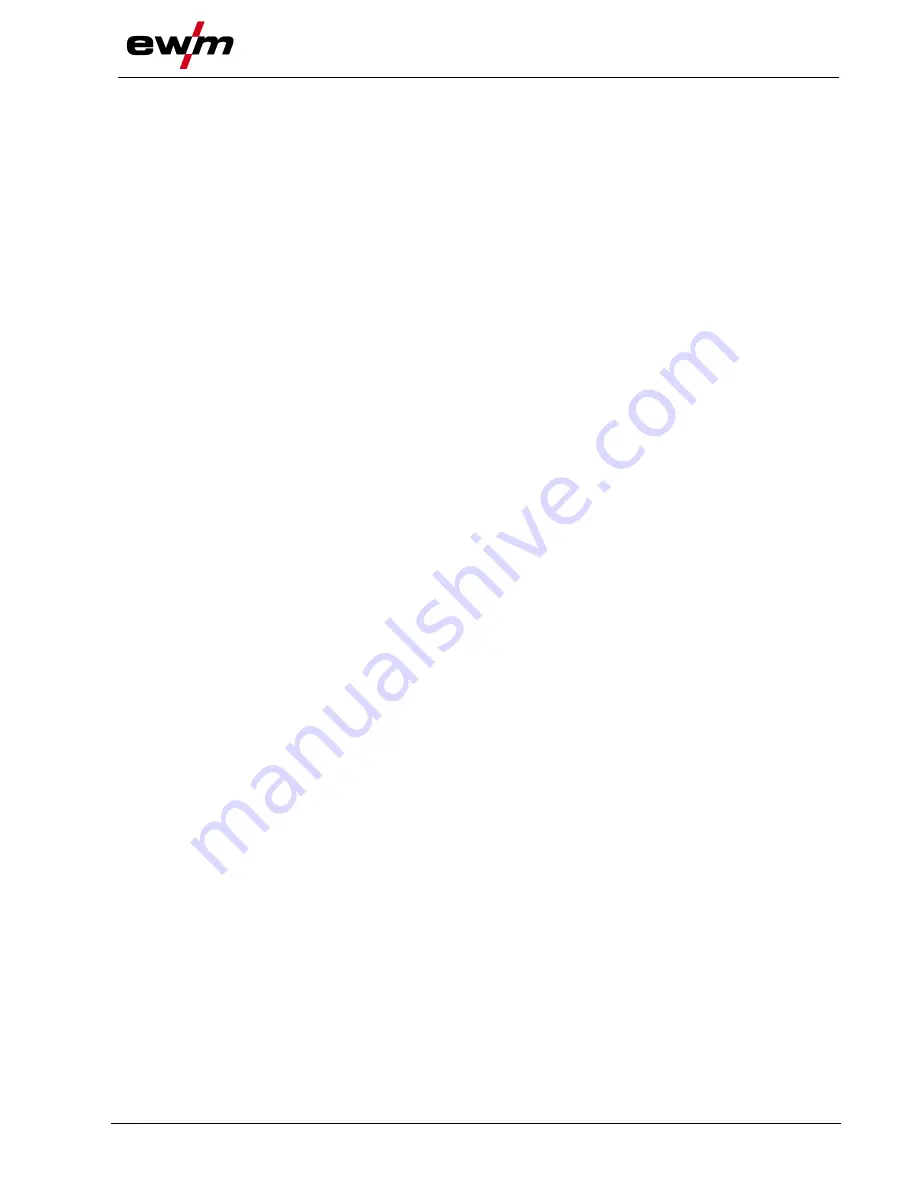
Design and function
Special parameters (advanced settings)
099-005444-EW501
17.03.2015
87
5.17.1.2 The special parameters in detail
Ramp time for wire inching (P1)
The wire inching starts with a speed 1.0 m/min for 2 secs. It is subsequently increased to a ramp function
to 6.0 m/min. The ramp time can be set between two ranges.
During wire inching, the speed can be changed by means of the welding parameter setting rotary dial.
Changing the speed has no effect on the ramp time.
Program "0", releasing the program block (P2)
The program P0 (manual setting) is blocked. Only operation with P1-P15 is possible, irrespective of the
key switch position.
Display mode for Up/Down welding torch with one-digit 7-segment display (P3)
Normal display:
Program operation: Program number
Up/down operation: Up/down setting
Alternating display:
Program operation: Change program number and welding process (pulse/non-pulse)
Up/down operation: Change up/down setting and up/down symbol
Program limit (P4)
Program selection can be limited with the special parameter P4.
• The setting is adopted for all JOBs.
• Program selection depends on the position of the "welding torch function" changeover switch (see
"Machine description"). Programs can only be switched when the changeover switch is in the
"program" position.
• Programs can be switched by means of a connected remote control or special welding torch.
• If a special welding torch or a remote control is not connected, it is only possible to switch programs by
means of the "arc length correction/select welding program" rotary dial (see "Machine description").
Special cycle in the operating modes special latched and non-latched (P5)
With the special sequence activated, the start of the welding process changes as follows:
Sequence for special non-latched mode/special latched mode:
• Start program "P
START
"
• Main program "P
A
"
Sequence for special non-latched mode/special latched mode with custom sequence activated:
• Start program "P
START
"
• Reduced main program "P
B
"
• Main program "P
A
"