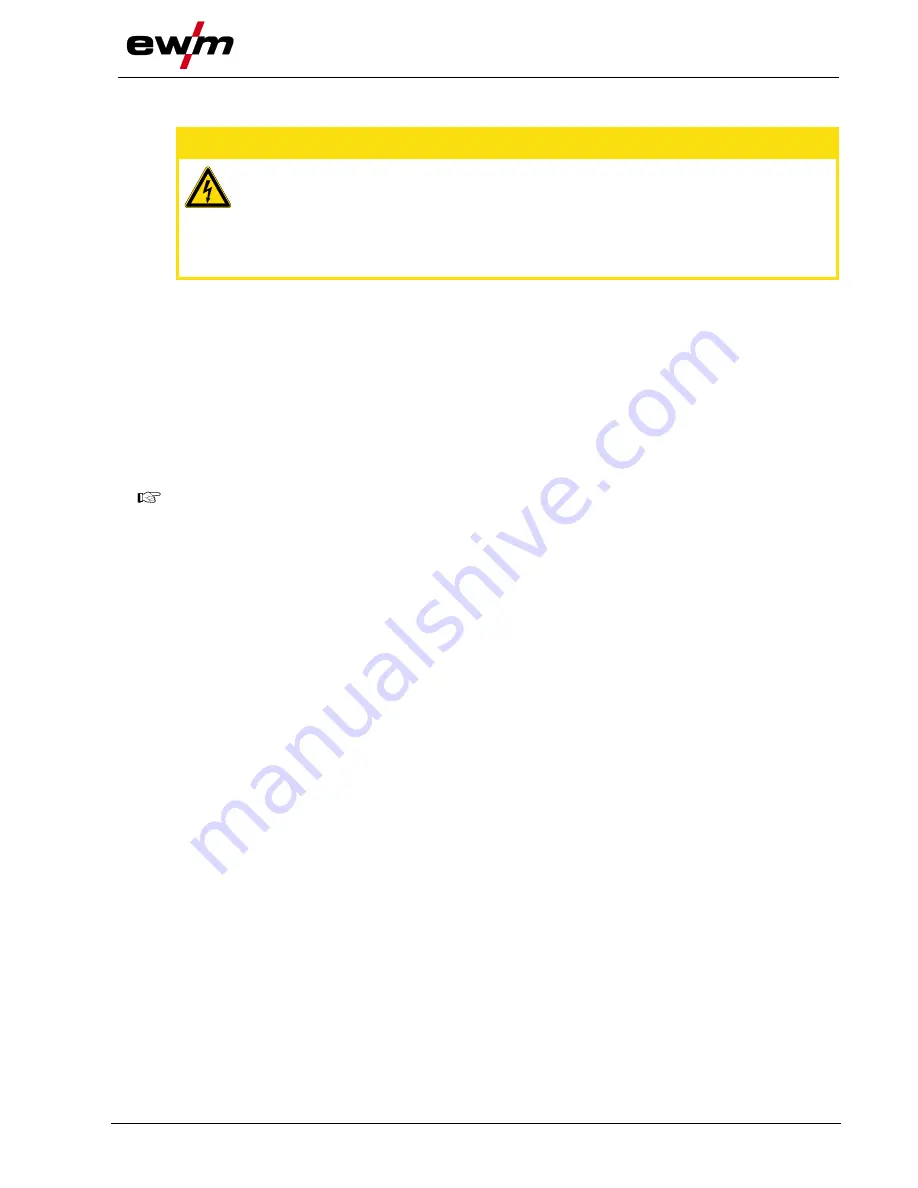
Design and function
PC Interfaces
099-005444-EW501
17.03.2015
83
5.15 PC Interfaces
CAUTION
Equipment damage or faults may occur if the PC is connected incorrectly!
Not using the SECINT X10USB interface results in equipment damage or faults in signal
transmission. The PC may be destroyed due to high frequency ignition pulses.
• Interface SECINT X10USB must be connected between the PC and the welding machine!
• The connection must only be made using the cables supplied (do not use any additional
extension cables)!
PC 300 welding parameter software
Create all welding parameters quickly on the PC and easily transfer them to one or more welding
machines (accessories: set consisting of software, interface, connection leads).
Q-DOC 9000 welding data documentation software
(Accessories: set consisting of software, interface, connection leads)
The ideal tool for welding data documentation of, for example:
welding voltage and current, wire speed and motor current.
WELDQAS welding data monitoring and documentation system
Network-compatible welding data monitoring and documentation system for digital machines
5.16 Protecting welding parameters from unauthorised access
The key switch is only available for machines which are fitted with the "OW KL XX5" option ex
works.
To protect against unauthorised or unintentional adjustment of the welding parameters on the machine,
the control input can be locked with the aid of a key switch.
In key switch position 1 all functions and parameters can be set without restriction.
In key switch position 0 the following functions and parameters cannot be changed:
• No adjustment of the operating point (welding performance) in programs 1–15.
• No change of welding or operating mode in programs 1–15.
• The welding parameters can be displayed but not changed in the control's function sequence.
• No welding task switching (JOB block operation P16 possible).
• No change of special parameters (except P10). Restart required.
5.17 Special parameters (advanced settings)
Special parameters (
P1
to
Pn
) are applied for customer-specific configuration of machine functions. This
allows the user maximum flexibility in optimising their requirements.
These settings are not configured directly on the machine control since a regular setting of the
parameters is generally not required. The number of selectable special parameters can deviate between
the machine controls used in the welding system (also see the relevant standard operating instructions).
If required, the special parameters can be reset to the factory settings.