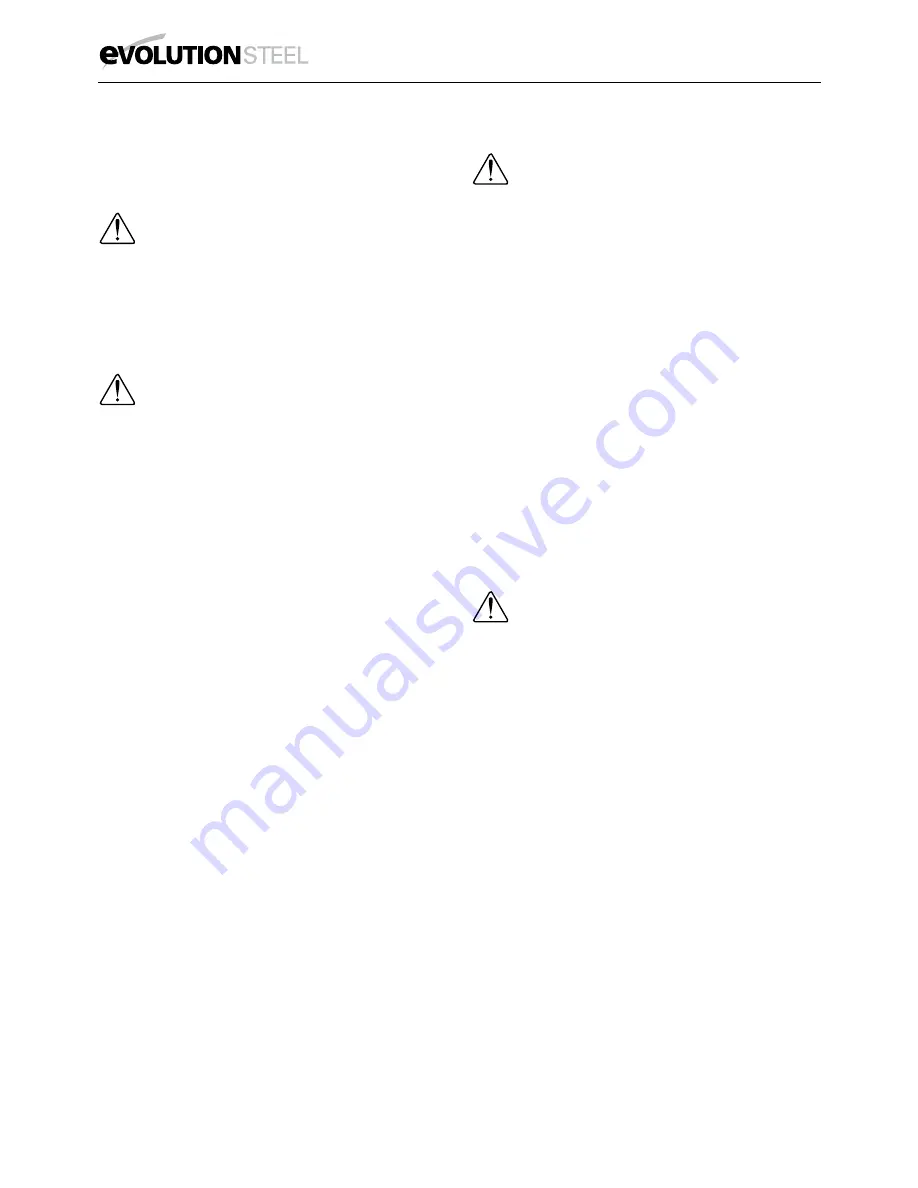
10
www.evolutionsteel.com
5) PREPARATION and SETTING UP.
The Electromagnet on this machine is designed
to adhere to ferrous metallic surfaces only.
WARNING: The electro magnet fitted
to this machine is a two stage magnet.
With the machine positioned, and the magnet
switched ‘ON’ but the motor switched ‘OFF’ the
magnet is at 50% strength. The magnet only
reaches full strength when both the Magnet and
Motor switches are in the
‘
ON’ position.
WARNING: The use on any material
whose thickness is less than that
specified in this Instruction Manual will
progressively reduce the magnetic performance,
and could result in a potentially dangerous
condition arising.
• Always prepare the material surface
before
attaching the machine. The material surface
must be clean, flat and free from rust, protective
coatings, grease or other debris such as
chippings or swarf from previously drilled holes.
• Always check the surface of the magnetic
base ensuring that it is not damaged and is
clear of debris such as chippings or swarf from
previously drilled holes.
• Never use this machine on a structure where
arc welding is taking place. Damage to the
machine will result as the welder will ground
through the power tools ground or earth cable.
6) DURING CUTTING OPERATIONS.
WARNING:
The swarf and the slug
produced will be hot and sharp.
• When using annular cutters ensure that the
slug ejected at the end of the cut will not
endanger anyone in the vicinity.
• If working at height some form of collection
device for the ejected slug may be necessary.
• Care should be taken with the ejected slug,
this will be both hot and sharp, gloves should
be worn when handling the slug.
• This power tool can be used on a vertical
surface or upside down provided there is
sufficient magnetic adhesion, extra care should
be taken when drilling vertically or inverted .
When using the machine vertically or inverted
it is possible hot and sharp swarf or chips
may fall. Always wear appropriate personal
protective equipment.
7) SAFETY STRAP OR SAFETY CHAIN.
WARNING:
The electro-magnet base
on this power tool can deactivate if
the power supply is interrupted or suffers an
electrical malfunction.
• To prevent possible operator
injury, the safety
strap or chain supplied should be used at all
times to provide extra security in the event of
supply failure or electrical malfunction.
Note:
When drilling some very large flat,
horizontal plates, the fitting of the safety strap
or chain may be inapplicable. Consult the
responsible person for guidance.
• The safety strap or chain should be attached
to the fixing points provided and checked for
security before commencing any and every
drilling operation.