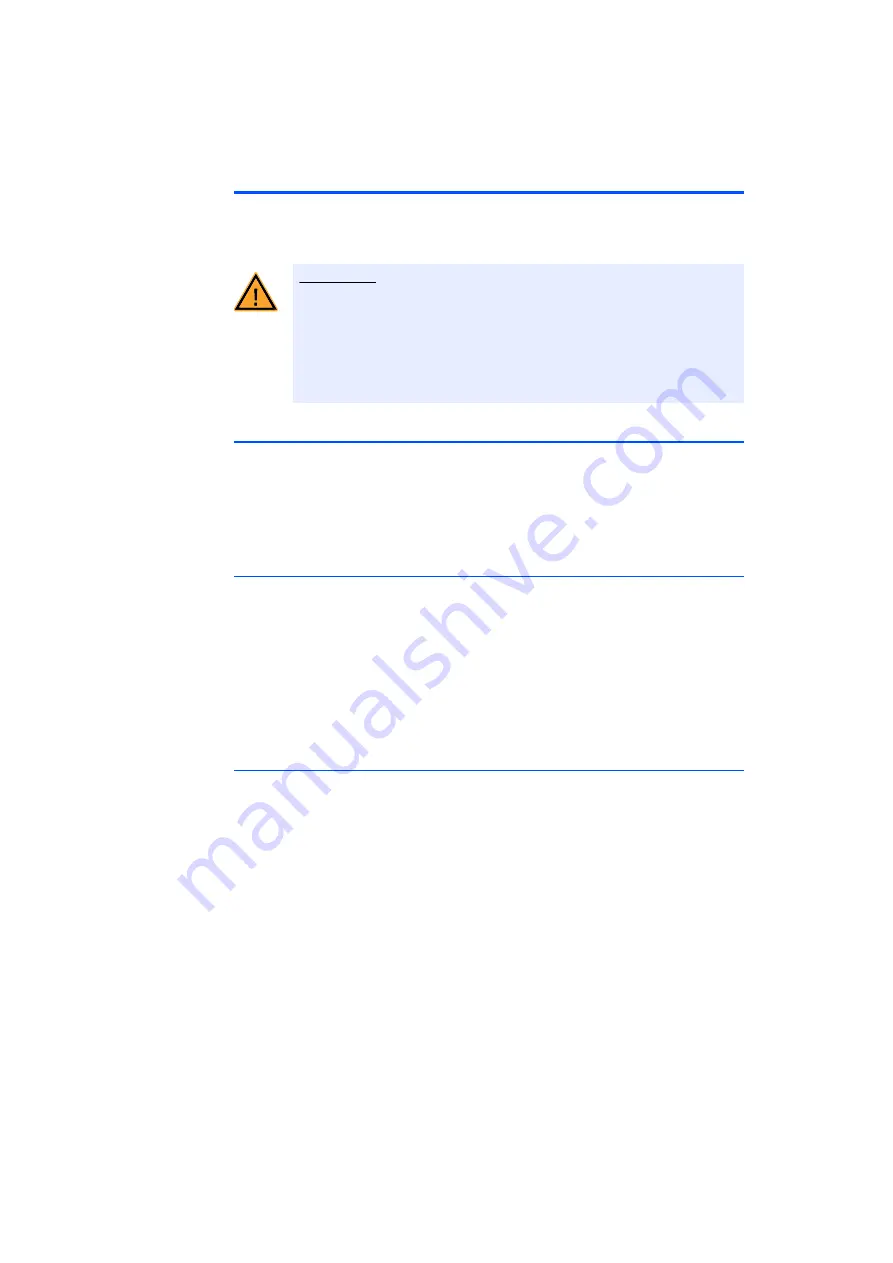
ES5340.2 Electric Drive Simulation Board - User’s Guide
7
ETAS
Introduction
1
Introduction
This User's Guide contains the description of the ES5340.2 Electric Drive Simula-
tion Board. In this chapter, you can read information about the basic functions
and application area of the ES5340.2 Electric Drive Simulation Board.
1.1
Properties
The ES5340.2 Electric Drive Simulation Board with PCI-Express interface is used
to test ECUs for inverters/electric motors on the signal level. The ES5340.2 is
designed for applications with extremely high speed and accuracy requirements.
It enables simulation of an inverter with electric motor, either on the Real-Time
PC or directly on the FPGA of the board.
1.1.1
Signals
The ES5340.2 measures the inverter control signals from the ECU – using the
measuring results, an inverter/electric motor model can be simulated on the
RTPC, the output variables of which (current and voltage signals and angle and
speed information) are returned to the ECU via the ES5340.2.
The sensor signals can be displayed in analog or digital form. All common posi-
tion sensors, such as resolvers, sine and digital encoders, can be displayed.
Other analog and digital signals are also possible, such as fault signals, battery
charge levels or DC/DC converter control.
1.1.2
Inverter/PMSM
1
Model
For the ES5340.2 Electric Drive Simulation Board, a configurable FPGA-based
inverter/PMSM model is offered. It models a 6-gate inverter and a permanent
magnet synchronous machine (PMSM) with mechanical system.
The FPGA model generates all electrical and mechanical values for the inverter
and the electric motor and takes into account all important physical effects, such
as saturation and temperature effects.
Its distinguishing feature is a highly balanced ratio of speed to accuracy. With the
FPGA-based model, the model run times are reduced significantly from approxi-
mately 10 μs with a C code model (see "Real-Time PC Model" on page 9) gen-
erated from Simulink
®
to 800 ns.
CAUTION!
Some components of the ES5340.2 Electric Drive Simulation Board
can be damaged or destroyed by electrostatic discharge. Leave the
board in the transport packaging until it is installed.
The ES5340.2 Electric Drive Simulation Board must always be
removed from the transport packaging, configured and installed at a
workstation that is protected from electrostatic discharge.
1.
P
ermanent
M
agnet
S
ynchronous
M
achine
Summary of Contents for ES5340.2
Page 1: ...ES5340 2 Electric Drive Simulation Board User s Guide...
Page 6: ...ES5340 2 Electric Drive Simulation Board User s Guide 6 Contents ETAS...
Page 22: ...ES5340 2 Electric Drive Simulation Board User s Guide 22 Introduction ETAS...
Page 116: ...ES5340 2 Electric Drive Simulation Board User s Guide 116 ETAS Contact Addresses ETAS...
Page 118: ...ES5340 2 Electric Drive Simulation Board User s Guide 118 Figures ETAS...