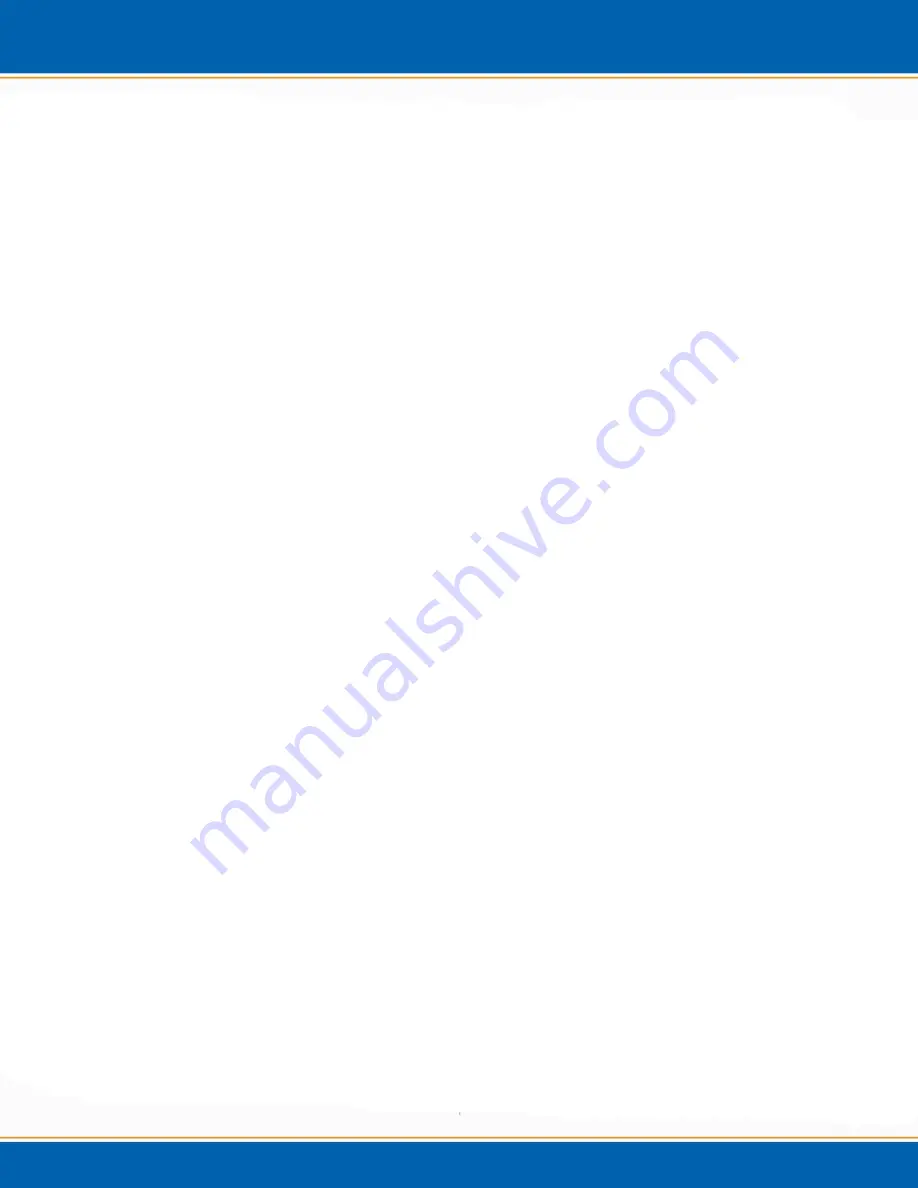
1.1 Product
Description
Over the past several years, the Encon has proven itself to be an extremely reliable instrument
providing 24/7 hours of operation. EST Analytical is now introducing the Encon Evolution with
features such as: the Foam Sensor, Modular Pressure/Flow Control for programmable flow rates
and an automated leak/pressure check. The modular design of the flow controller allows the user
to replace individual components in case of failure instead of the expense of replacing the entire
Mass Flow controller. Moisture control is performed during the purge cycle to reduce the
sample desorb pathway. Optional touch screen interface along with easy trap access from the
front of the instrument make daily use and operation very simple. With superior
chromatographic resolution, the Encon has evolved with features that will make the laboratory
more productive and ensure data integrity.
As limits are pushed lower in many states, carryover within the purge and trap system is
becoming a greater concern. In the past, efforts have been to reduce carryover with new sample
pathway materials and programmable flow rates during the bake cycle, but little has been done to
deal with the primary cause of the carryover, the sparge vessel itself. If an analyst runs a high
level sample, followed by a blank, a certain level of carryover can be seen on all purge and trap
systems. If an analyst runs a high level sample, replaces the glassware, then runs a blank a 70-
90% reduction in carryover can be seen. The new Encon Evolution employs a mode where
during the bake cycle of the concentrator, the sparge vessel is heated (Patent Pending). The result
is the lowest level of carryover of any concentrator today.
Other features like; DPC – Desorb Pressure Control (Patent Pending) can help provide superior
chromatographic resolution. There are many different parameters that can affect peak shape,
especially with the early eluting compounds. The peak shape of these compounds can be greatly
affected by flow rates and pressure changes within the trap. One of the problems is that the trap
pressure is often different than the GC column head pressure. When the concentrator goes into
desorb, the multiport valve turns to allow GC carrier flow to travel through the trap. If the trap is
at a pressure lower than the column head pressure, the trap will experience a surge in gas flow to
adjust to the new pressure causing poor peak shape and/or recovery of the light compounds. The
Encon Evolution allows the user, after purge, to establish a set pressure within the trap. Users
can adjust this setting depending upon the column head pressure they are using to optimize peak
shape.
EST Analytical was the first to introduce a foam sensor to purge and trap. Fritted sparge vessels
improve purging efficiency but they also increase the frequency of samples foaming. With the
Encon Evolution, if a foamed sample is detected the sample will be drained; the GC will be sent
a start signal to perform a blank run, ensuring the GCs sequence table is accurate. The sample
pathway is then baked out and a notification is written to the instrument’s sample log.
Windows XPe Graphical Display is the new EST Analytical user interface. This is an easy to use
programming environment that provides total system information. Basic status screens display
real time pressure and flow paths. Modes and times of operation give the user an easy way to
review overall system parameters and current status. System maintenance screens give users
complete control of the entire system. Click on each valve to manually actuate solenoids or the
multi-port valve, perform automated leak and flow checks or condition a new trap with the press
Summary of Contents for Encon Evolution
Page 1: ...Encon Evolution User Manual Original Operating Instructions Rev 4 5 ...
Page 2: ......
Page 8: ...User Manual Introduction Chapter 1 ...
Page 15: ...User Manual Installation and Setup Chapter 2 ...
Page 20: ...User Manual Operation Chapter 3 ...
Page 47: ...User Manual Maintenance and Troubleshooting Chapter 4 ...
Page 61: ...User Manual Flow Diagrams Chapter 5 ...
Page 62: ...Figure 5 1 Standby Dry Purge Flow Diagram ...
Page 63: ...Figure 5 2 Purge Flow Diagram ...
Page 64: ...Figure 5 3 Desorb Ready Flow Diagram ...
Page 65: ...Figure 5 4 Desorb Flow Control Flow Diagram ...
Page 66: ...Figure 5 5 Desorb Auto Drain Flow Diagram ...
Page 67: ...Figure 5 6 Desorb Flow Diagram ...
Page 68: ...Figure 5 7 Bake with Bake Gas Bypass Flow On Flow Diagram ...
Page 69: ...Figure 5 8 Bake with Bake Gas Bypass Flow Off Flow Diagram ...
Page 70: ...Figure 5 9 Leak Check Flow Diagram 1 ...
Page 71: ...Figure 5 10 Leak Check Flow Diagram 2 ...
Page 72: ......