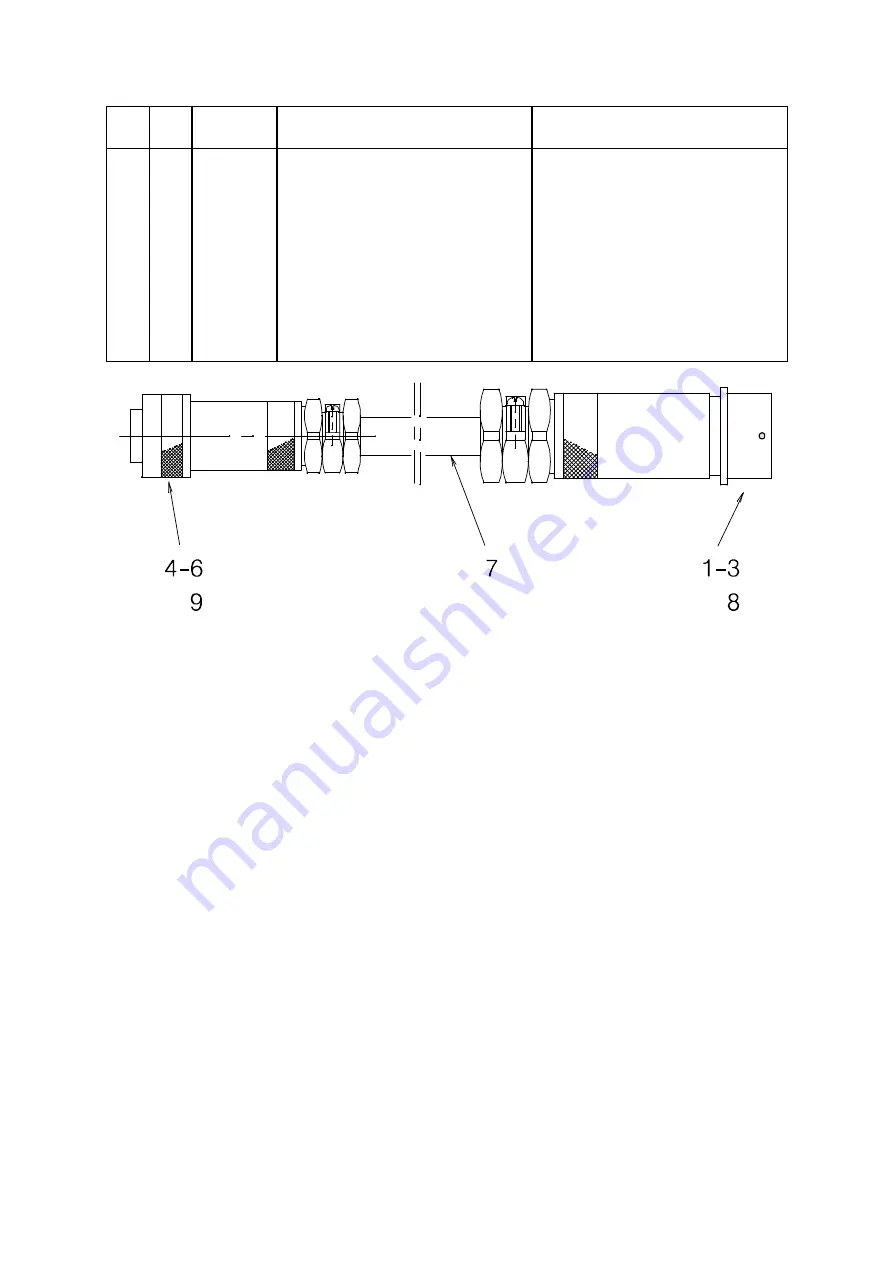
-- 72 --
f449448s
Item
no.
Qty
Ordering no. Denomination
Notes
0449448880
Adapter
28--12POL(PEH--LAF12P)
1
1
0368546106
Sleeve cable socket
28--pol
2
3
0323945003
Connector sleeve
0,52--1,50
3
5
0323945002
Contact sleeve
0,32--0,52
4
1
0368541303
Pin plug burndy
12 pol.
5
5
0323945001
Connector pin
0,32--0,52
6
3
0323945004
Connector pin 0,52--1,50
0,52--1,50
7
1
0193963001
Cable, screened
5x0.5mm2 3x1.5mm2 4x2.5mm2
8
4
0323945007
Contact sleeve
max 2.5mm2
9
4
0323945008
Contact pin
max 2.5mm2