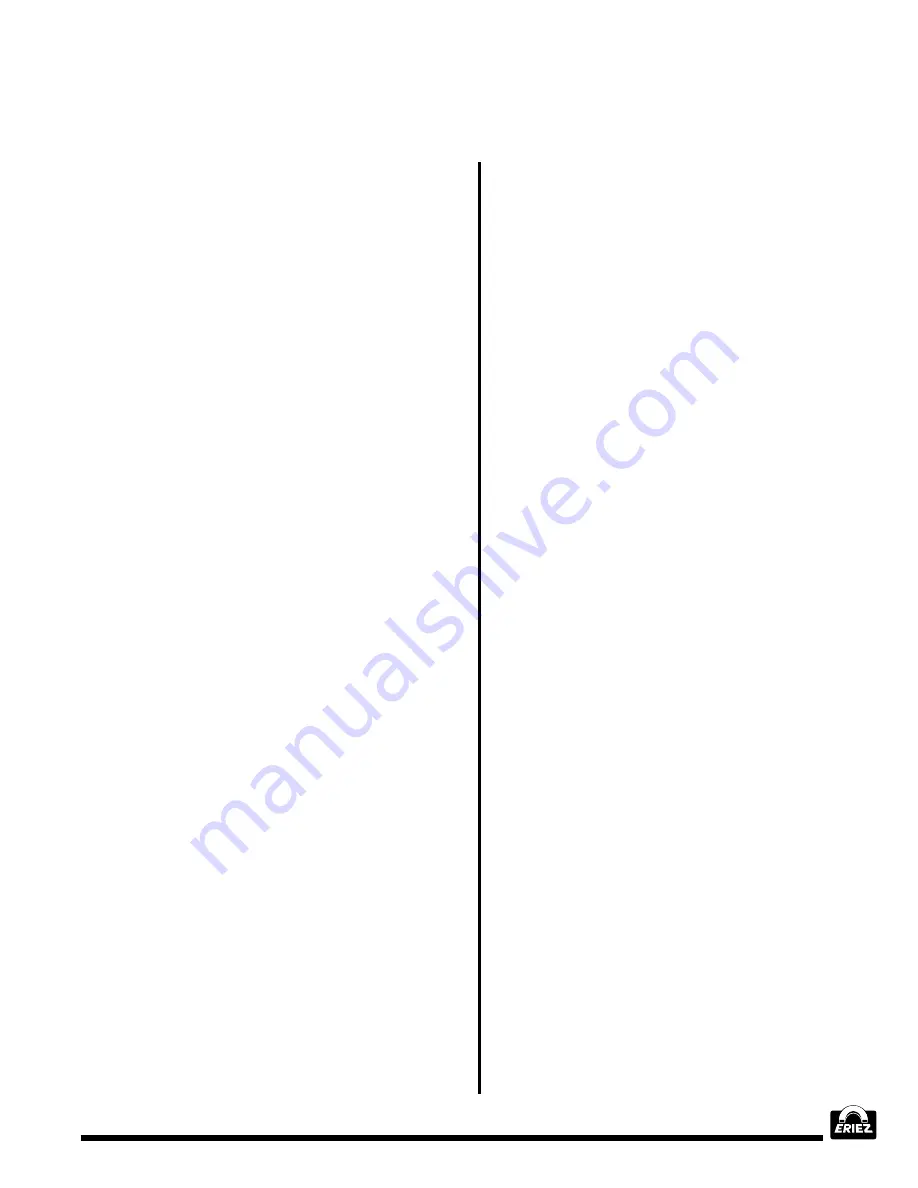
®
17
METAL FREE AREA
The metal detector monitors an electromagnetic
field to detect metal. This field is predominantly
contained within the metal detector sensing
aperture but some fringing of the field exists at
the entrance and exit openings. The fringing field
will allow the metal detector to detect metal in
the vicinity of the entrance and exit. For this
reason, metal must not be located in this area.
The required metal-free area depends on the size
of the smaller dimension of the aperture. Normally
1.5 times the smaller aperture dimension is
sufficient clearance for non-moving metal. If
space allows, a 1.75 multiplier on the smaller
aperture dimension should be used. Applications
which involve relative movement between the
sensing head and adjacent metal should use a 2.0
multiplier. (For example, stationary metal should not
be located closer than 6 to 7 inches (150 to 175mm)
from either the entrance or exit opening of a metal
detector with a 4 x 8 inch aperture. Moving metal
should not be closer than 8 inches (200mm) from
the entrance or exit of such a detector.) Please refer
to Figure 8 for details.
ELECTRICAL CURRENT LOOPS
By far the most frequent trouble experienced with
metal detector installations is false tripping
caused by electrical current loops. As was
explained in the previous section, some
electromagnetic field extends from the metal
detector aperture. The field dissipates in strength
with distance, to a point that metal contained
outside the metal-free area defined above will not
cause false detections. However, since the field
is time-varying, small electrical currents are set
up in conveyor conduction paths (i.e. metalwork)
quite some distance from the aperture. These
currents and others (e.g. ground currents from
other nearby equipment) are not harmful as long
as they are constant, but if they change, the metal
detector will false trip. Figure 9 shows a simplified
aerial view of a typical metal detector and
conveyor. The arrows located within the conveyor
framework, head pulley, tail pulley and return
idlers represent electrical currents. The bearings
supporting the pulleys and idlers represent
potential switches. As they turn, the bearings
make and break contact with their respective
races through the lubricant within. Likewise the
cross-members of the conveyor framework
represent potential switches if they are attached
to the conveyor with bolts or rivets. Through time,
connections such as these work loose or corrode
and make and break electrical connections as a
result of normal conveyor vibrations. Potential
switches of both these types must be eliminated.
INSULATING THE CONVEYOR
SHAFTS
In the case of pulleys and idlers there is no way
to make the electrical path constant enough to
prevent changes in the currents. These currents
must be eliminated by introducing an insulating
medium within the conduction path. Figure 10
shows two common methods.
The method shown in Figure 10-A is
accomplished by machining the end of the shaft
which rides in the bearing to a small diameter
and inserting an Ultra-High Molecular Weight
(UHMW) plastic sleeve over it. The outside
diameter of the sleeve is the same as the inside
diameter of the bearing. This sleeve breaks the
electrical connection between the bearing and the
shaft, thus permanently preventing current flow.
WARNING: Do not cut through the sleeve when
tightening the bearing set screw.
Figure 10-B shows a method of insulating the
complete bearing block from the conveyor frame.
This requires drilling the bolt holes through the
bearing block to a larger diameter to accept an
insulating shoulder washer. The shoulder washer
wall thickness should be at least 1/32" (1 mm).
Alternatively the shoulder washer can be
replaced with a plastic washer and a length of
plastic pipe or hose. Insulating the bolt with
tape is not recommended. The bearing block
is insulated from the conveyor frame with a
UHMW insulator extending entirely across the
base of the block as shown.
Mechanical Installation (cont.)
Summary of Contents for E-Z TEC IV
Page 58: ...58 Figures cont Figure 5 Detect Modes...
Page 62: ...62 Figures cont Figure 12 Metal Detector Mounting Feet Figure 13 Conveyor Belt Splices...
Page 63: ...63 Figures cont Figure 14 Electrical Connections...
Page 64: ...64 Figures cont Figure 15 Analog Version Control Panel...
Page 67: ...67 Figures cont Figure 19 Flowchart of MPC Menu Structure...
Page 98: ...98 This Page Intentionally Left Blank...