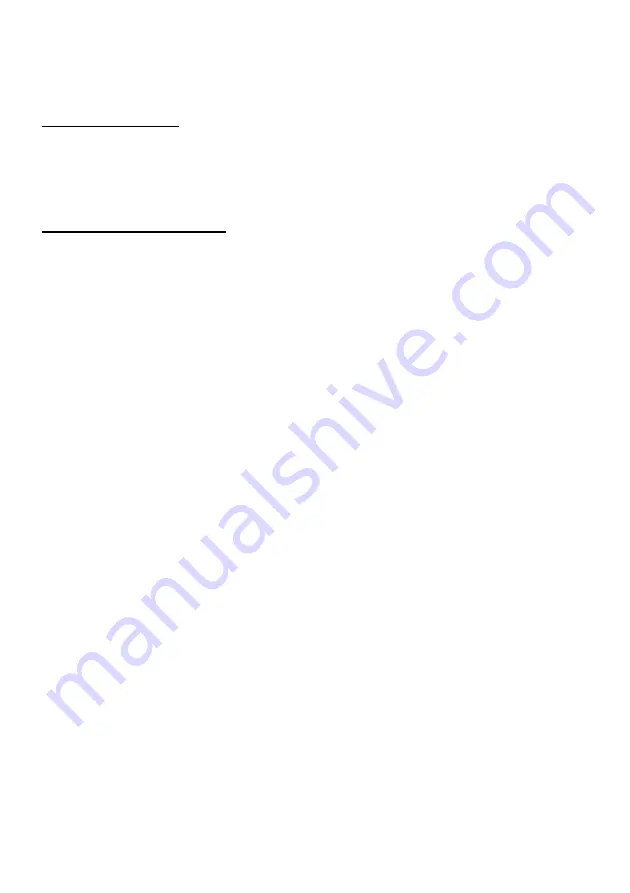
15
required. At any time during the spot welding time the torch switch is released, the machines will
immediately stop.
Burnback control
All
ergo
line sets have a built-in timer for controlled burnback switch-off. Burnback is the time
between motor stop and current switch off, so the length of the wire beyond the tip (after finishing
the welding process) is controlled. This adjustment is factory-set inside the set. If a different
adjustment is necessary, please contact your local dealer.
Maintenance Procedure
•
check periodically all cable connections are secure and undamaged
•
periodically clean and remove dust from inside of equipment
•
regularly inspect torch for damage or wear and replace worn or damaged parts as required
The welding plant has been designed and constructed to give trouble free service. Any faults which
may arise will most probably be the result of improper treatment or overloading.
Repair and servicing work should only be carried out by a competent electrician. If any doubt
consult the supplier of the equipment.
Faults and how to trace them
•
Unit does not function:
Mains fuse has blown. Replace fuse
•
Power source does not receive voltage
. Switch is off or defective. Switch to position 1.
Replace switch if defective.
•
No welding current:
Torch switch defective. Replace. Main contactor defective. Check and
replace.
•
Machine cuts out:
Overheated transformer. Allow to cool. Faulty Rectifier. Replace.
•
Poor wire feed, motor runs irregularly
. Contact tip or wire feed guide blocked or defective.
Clean or replace. Wire feed unit defective. Replace if faulty. Printed circuit card defective.
Replace if faulty.
•
Wire feeds irregularly:
Contact tips is clogged or deformed. Replace. Wire feed slipping on
drive roller. Increase wire feed tensioner arm. Damaged or blocked torch assembly. Check,
clean or replace.
•
Wire does not feed:
Loose connection on PCB. Check and tighten. Defective PCB. Replace
•
Fluttering arc:
Contact tip worn. Replace, Voltage to high. Reduce voltage or increase wire
feed speed.
•
Unstable arc:
Poor contact between earth and workpiece. Tighten and clean. Incorrect setting.
Readjust voltage and wire feed control. Dirty workpiece. Clean.
•
Porous weld:
Gas leak, check and tighten, Gas nozzle clogged. Clean or replace. Not enough
shielding gas. Increase gas flow (9-12 litres/min.). Gas shield deflected by draught. Screen off
welding area
The information given in the fault finding procedure are for general guidance purposes only and for
more detailed information consult the supplier of the equipment. Read safety advice prior servicing
the set.