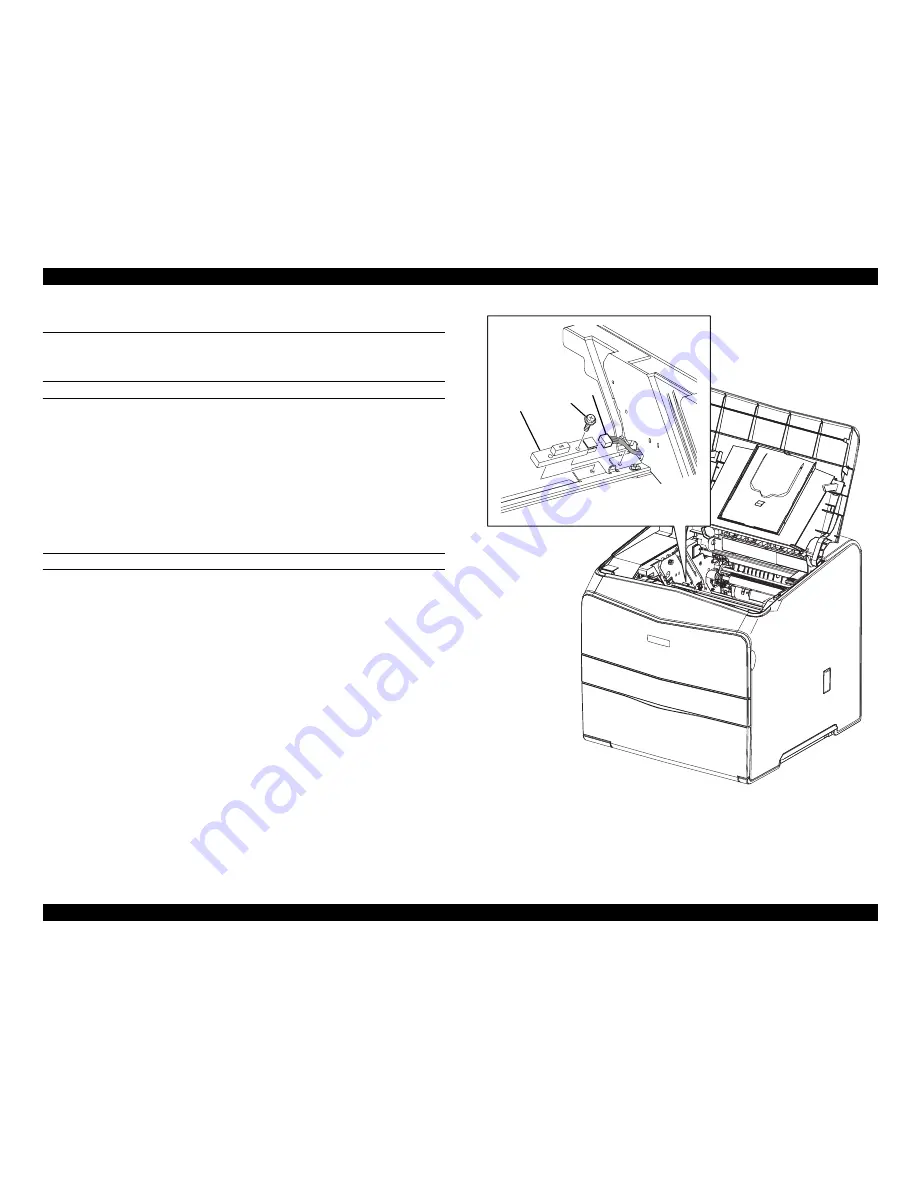
EPSON AcuLaser C1100
Revision B
DISASSEMBLY AND ASSEMBLY
XERO
361
4.6 XERO
4.6.1 SENSOR TR-0
REMOVAL
1.
Open COVER ASSY TOP.
2.
Remove Photoconductor Unit.
3.
Remove the screw (silver, with flange, 10mm) fastening SENSOR TR-0 to
PLATE-TR-0.
4.
Remove SENSOR TR-0 from PLATE-TR-0.
5.
Disconnect connector (P/J108) from SENSOR TR-0.
REINSTALLATION
1.
Connect connector (P/J108) to SENSOR TR-0.
2.
Match the hole on SENSOR TR-0 with the boss on PLATE-TR-0, and attach
SENSOR TR-0.
3.
Fasten SENSOR TR-0 to PLATE-TR-0 with the screw (silver, with flange,
10mm).
4.
Attach Photoconductor Unit.
5.
Close COVER ASSY TOP.
Figure 4-72. Removal of SENSOR TR-0
Leg_Sec03_076EA
3)
5)
4)
Summary of Contents for C1100 - AcuLaser Color Laser Printer
Page 1: ...EPSON AcuLaserC1100 A4 Full Color Laser Printer SERVICE MANUAL SEPG04002 ...
Page 12: ...Schematic Diagram of Safety System Leg_Sec001_025EA ...
Page 19: ...C H A P T E R 1 PRODUCTDESCRIPTION ...
Page 74: ...C H A P T E R 2 OPERATINGPRINCIPLES ...
Page 119: ...C H A P T E R 3 TROUBLESHOOTING ...
Page 276: ...C H A P T E R 4 DISASSEMBLYANDASSEMBLY ...
Page 485: ...C H A P T E R 5 ADJUSTMENT ...
Page 491: ...C H A P T E R 6 MAINTENANCE ...
Page 510: ...C H A P T E R 7 APPENDIX ...
Page 539: ...EPSON AcuLaser C1100 Revision B APPENDIX Exploded Diagrams 539 7 6 Exploded Diagrams ...
Page 562: ...Model AcuLaser C1100 LP V500 Board C567MAIN Sheet 1 of 4 Rev A ...
Page 563: ...Model AcuLaser C1100 LP V500 Board C567MAIN Sheet 2 of 4 Rev A ...
Page 564: ...Model AcuLaser C1100 LP V500 Board C567MAIN Sheet 3 of 4 Rev A ...
Page 565: ...Model AcuLaser C1100 LP V500 Board C567MAIN Sheet 4 of 4 Rev A ...