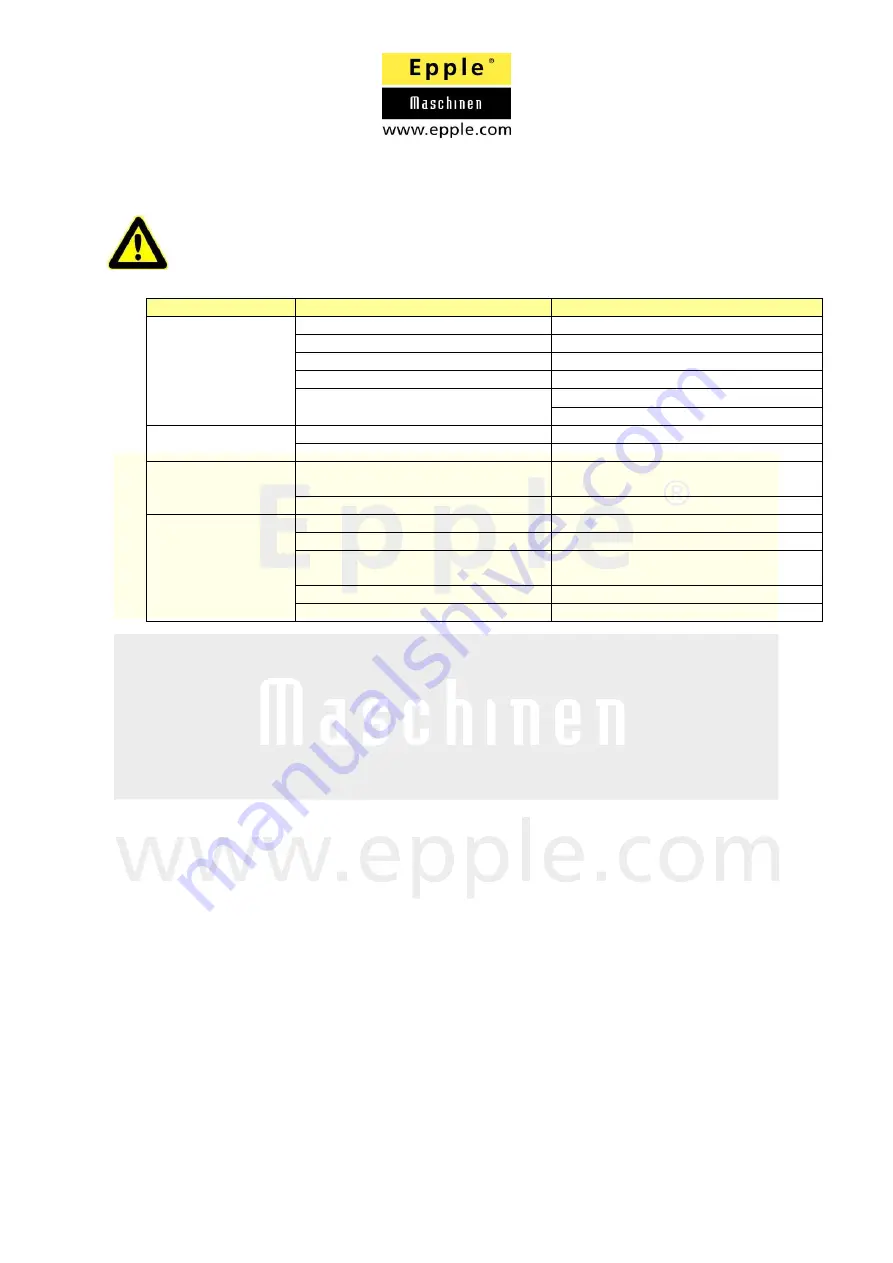
Stand 31.07.08, PW 30, PW 30 HV, Profile roll
Page 36 of 50
9 Failures
Attention!
Observe during the abatement of failures the safety regulations.
Failure
Possible causes
Corrective measure
Machine does not
get activated
Main switch deactivated
Activate main switch
Emergency Stop pushed
Release emergency Stop control
Overcurrent relay triggered
Reset overcurrent relay
Foot switch / cable defect
Renew control element/ cable
Block axes
Unload axle bearing
Change axle bearing
Machine only runs
in one direction
Foot switch / cable defect
Renew control element/ cable
Gate defect
Replace gate
Work part is not
bend constantly
Bending roller adjustment false
Approach in small Steps to the
requested bending radius
Bending rolls do not run centric
Use roller set with exact bore
Work part twists
during bending
False roller set
Use correct roller set
Roller profile worn out
Use new roller set
Fixing screws of the rolls loose, link
yields
Mount roller set orderly
Different roller profile
Use correct roller set
Different roller adjustment
Adjust roller set