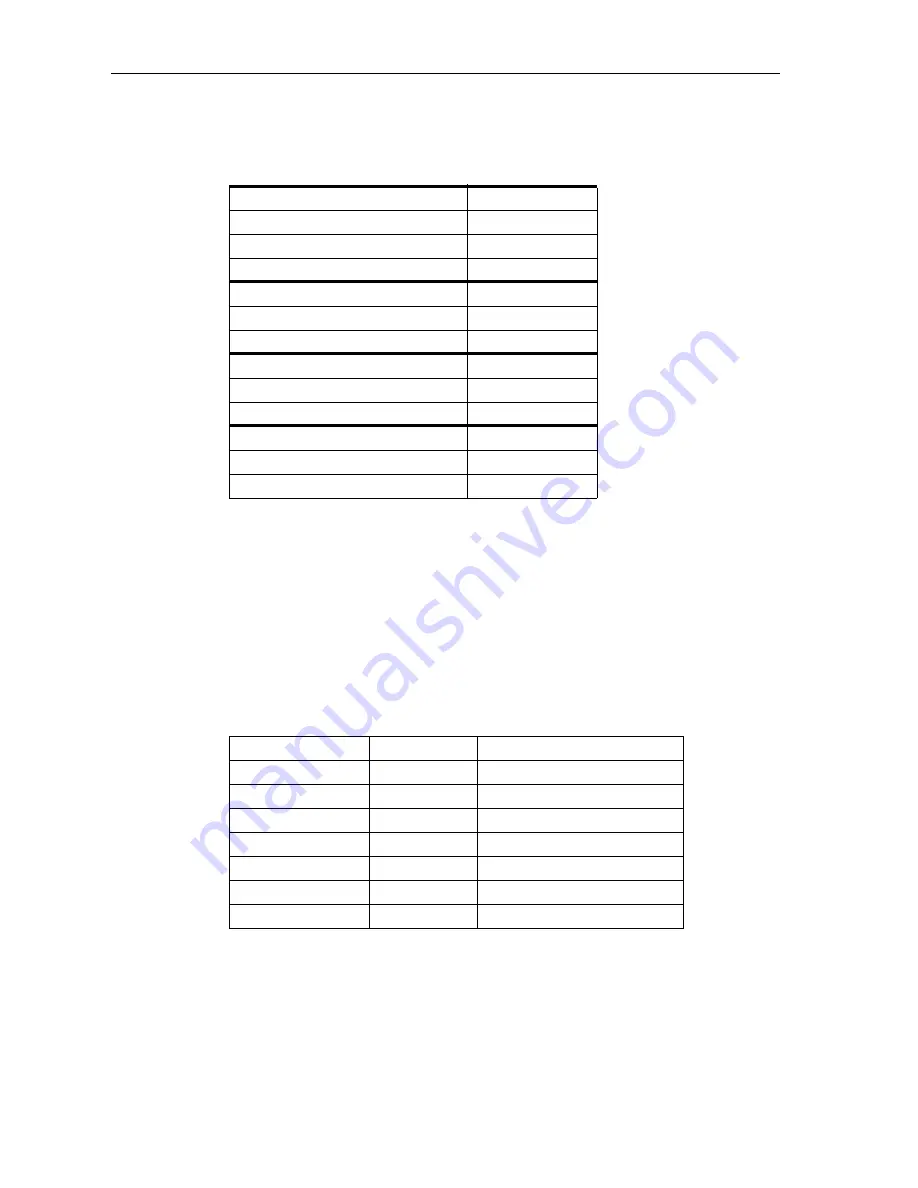
Testing Calibration and Relays
Entek IRD 6652 DSP Protection Monitor
43
The following table gives you example settings, inputs, and readings for a configuration.
Note:
Accuracy is ±2.5% of full scale for the display.
Alarm Relay Test
The following steps show you how to test the monitor relays. Most of the relays reflect the
alarm state (Alert or Danger) of an input channel. There is also a System OK relay that
responds to either channel 1 or channel 2 transducer fault, monitor system failure, or loss of
power. For the steps to test the System OK relay, see “Calibration and System OK Relay
Test” on page 42.
Note:
If the LATCHED option is set to YES, you may have to manually reset the relays by
pressing the
RES
button on the front panel of the monitor. The LATCHED option is on the
RELAYS submenu (page 31).
The relay contacts on the backplane of the 6652 DSP are:
Note:
Make sure you configure the monitor to use the second Danger relays for Danger alarms.
The relay testing procedure does not work for the second Danger relays (4, 7) if you
configure the monitor to use those relays for vector (eccentricity) alarms. Set the MON ECC
option on the ECCNTRY submenu to - RELAY or DISABLE. See “ECCNTRY submenu”
on page 30 for details.
Transducer native units (UNITS 1)
mil pp
Transducer sensitivity (TX1 SNS)
70.7 mVRMS/mil
Display units (same as UNITS 1)
mil pp
Full scale (SCALE 1) value
3 (mil pp)
Input signal (50% full scale)
106.1 mV
Front panel digital display
1.5 mil pp
4–20 mA recorder terminals
12 mA
Input signal (100% full scale)
212.1 mV
Front panel digital display
3.0 mil pp
4–20 mA recorder terminals
20 mA
Input signal 0 (zero)
0 mV
Front panel digital display
0.0 mil pp
4–20 mA recorder terminals
4 mA
Function
Relay
Terminals (N/C, Comm, N/O)
System OK
1
25, 26, 27
channel 1 Alert
2
28, 29, 30
channel 1 Danger
3
31, 32, 33
channel 1 Danger
4
34, 35, 36
channel 2 Alert
5
37, 38, 39
channel 2 Danger
6
40, 41, 42
channel 2 Danger
7
43, 44, 45