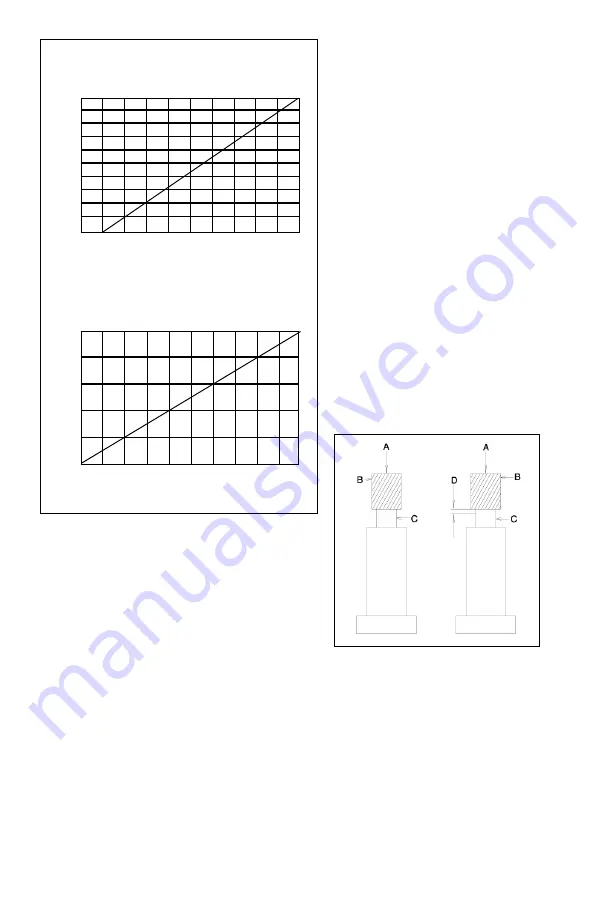
two-position manual air valve (VA-42) or a solenoid
operated air valve (VAS-42) to the supply line. This valve
will block the air supply and vent the work support in
one position and provide air supply to the work support
without venting in the other position.
NOTE:
When the air supply is removed from the work
support, the plunger will not retract by itself except
under gravity when mounted vertically. However, the
plunger will be free to move if bumped or contacted by
a workpiece being loaded or unloaded.
5.2 Modifications
If the work support is to be used without a contact
bolt, replace the bolt with the provided set screw.
Seal this set screw with Loctite 242 and position flush
with the top of the plunger.
6.0 OPERATION
1. Install work supports according to preceding
instructions.
2. Place the workpiece into the fixture and above the
work supports.
3. Activate hydraulic pressure to advance the
plunger against the workpiece. Work support
plunger position will be maintained until
hydraulic pressure is released.
4. Clamp the workpiece in position to facilitate
machining operations.
5. When machining is complete, release the
clamps and then release the work support
hydraulic pressure. The work supports will
now be released and the plungers will retract.
6. Remove workpiece from the fixture.
NOTE:
Do not exceed the specified maximum load
on the support plunger. This load is the result of
clamping forces from other hydraulic components
such as swing clamps and machining forces. Table
1 shows the maximum applied load versus the
pressure which locks the plunger. Table 2 shows
the deflection of the support plunger when
applying a load on the cylinder.
6.1 For Spring Advanced Work
Supports Only:
Operation is similar for a work support using air
as the spring. If air is used to advance the
plunger, then the air valve must be shifted to
advance the plunger after the workpiece is
mounted in its final position in the fixture. The air
valve can be released after the support is
hydraulically locked.
Figure 3
A - Load
B - Workpiece
C - Support Plunger
D - Deflections
7.0 MAINTENANCE AND SERVICE
Maintenance is required when wear and/or leakage is
noticed. Occasionally inspect all components to
detect any problem requiring service and
maintenance. Enerpac offers Repair Part Kits for
equipment maintenance. Repair Part Sheets are also
available. Contact your Enerpac representative.
4
TABLE 1
MAXIMUM HOLDING FORCE VS. HYDRAULIC
OPERATING PRESSURE
Operating Pressure (PSI)
TABLE 2
SUPPORT PLUNGER DEFLECTION VS. APPLIED LOAD
(AT 5000 PSI OPERATING PRESSURE)
Applied Load (LBS.)
MAXIMUM HOLDING FORCE (LBS
.)
2500
2000
1500
500
1000
0
1000
2000
3000
4000
5000
.0025
.0020
.0015
.0005
.0010
0
500
1000
1500
2000
2500
ELASTIC DEFLECTION (IN.)
Summary of Contents for WFL111
Page 36: ...WFL 111 112 WSL 111 112 08 02...
Page 37: ...37 P 4X...