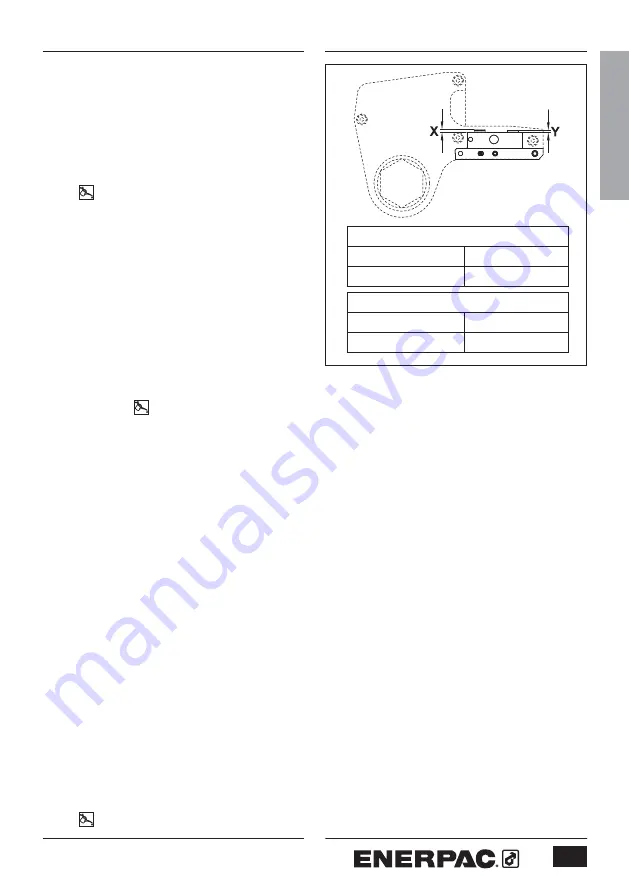
ENGLISH
11
• Remove
circlips (24) reaction rollers
(25) and roller pin (26).
•
Clean all exposed components with a
mild solvent.
•
Inspect all parts for damage.
•
Dry all components. Apply a thin coat
of molybdenum disulphide lubricant
as indicated.
5.2.2 The hydraulic drive unit
•
Check tightness of swivel manifold
post retaining screws (see 5.3.2) and
gland.
•
Pressurize the drive unit to maximum
pressure (
Advance
and
Retract
), and
check for any signs of leakage.
•
Any damaged components or seals
must be replaced.
•
Dry all components and apply a
thin coat of molybdenum disulphide
lubricant
as indicated.
5.3 Full
maintenance
Note:
Refer to the WCR4000 repair
parts sheet for detailed views of
components and subassemblies
referenced in sections 5.3.1 and 5.3.2.
5.3.1 The roller cassette
•
Strip down and clean all exposed
components with a mild solvent.
•
Drift out the spring pin holding the
cylinder retaining pin, and remove the
retaining pin.
•
Inspect all parts for damage.
•
Perform non destructive testing by
magnetic particle inspection on the
following components:
- Sideplates
- Cylinder locating plate
- Cylinder retaining pin
- Reaction roller bracket and pin
- Reaction rollers and roller pin
•
Dry all components. Apply a thin coat
of molybdenum disulphide lubricant
as indicated.
•
Check retaining pin height (X) and fail
safe pin height (Y). Refer to Fig. P.
•
Reverse the procedure to reassemble
the tool.
5.3.2 The hydraulic drive unit
•
Remove the circlip from the swivel
manifold block.
• Remove
the
hydraulic couplings.
• Remove
the
swivel manifold block
from the drive unit.
• Remove
the retaining screws and the
swivel manifold post.
•
Remove all ‘O’ rings from swivel
manifold post.
•
Carefully hold the cylinder body to
unscrew the cylinder gland.
•
Hold the two flat sides of the piston
rod with a spanner. The rod is located
at the spigot.
•
Remove the button head cap screw
from the piston.
•
Remove the piston rod from the
cylinder spigot end.
•
Remove the piston from the cylinder
gland end, using a suitable drift.
Retaining Pin Height - Dimension “X”
Metric
Imperial
5,00 mm
0.197 inch
Fail Safe Pin Height - Dimension “Y”
Metric
Imperial
3,00 mm
0.118 inch
Fig. P
Summary of Contents for WCR4000
Page 1: ...Instruction Sheet WCR4000 Roller Cassette L4021 English GB Rev B 09 2013...
Page 2: ...2...
Page 17: ...17 NOTES...
Page 18: ...18 NOTES...
Page 19: ...19 NOTES...