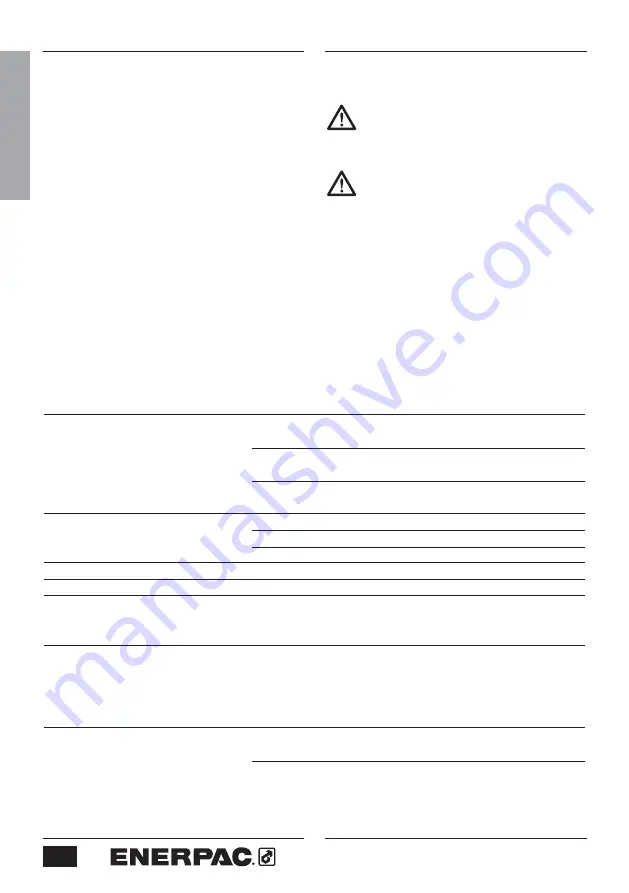
•
Reverse the procedure to reassemble.
When reassembling the drive unit make
sure that the piston rod is inserted
through the cylinder spigot end.
When reassembling the drive unit
make sure that the piston is inserted
through the gland end. Tap the piston
gently into place against the piston
rod.
•
Pressurize the assembled drive unit to
max pressure (
Advance
and
Retract
),
and check for any signs of leakage.
ENGLISH
•
Clean all exposed components with a
mild solvent.
•
Inspect all parts for damage.
•
Perform non destructive testing by
magnetic particle inspection on the
following components:
- Cylinder body
- Piston rod
•
Apply a small amount of Loctite 243
to the threads of the button head
capscrew before reassembly.
•
Apply a small amount of Loctite
243 to the threads in the drive unit,
assemble the swivel manifold post
and tighten the degreased retaining
screws to 5,1 Nm (3.76 Ft.lbs).
5.4 Troubleshooting
5.4.1 Drive Unit
Symptom Cause
Remedy
Cylinder does not advance or retract. Quick-connect coupling
Replace the coupling.
is
damaged.
Quick connect coupling is
Reconnect the hoses
not connected.
and couplings securely.
Dirt in the direction control
Disassemble the unit and
valve on the pumping unit.
clean the valve.
Cylinder does not build pressure.
Piston seal leaks.
Replace the seals.
Pump does not build pressure.
Adjust the pressure.
Pump is defective.
Refer to the pump manual.
Cylinder leaks.
Seal failure.
Replace the cylinder seals.
Cylinder operates backwards.
Connections are reversed.
Reconnect hoses correctly.
5.4.2 Cassette
Symptom Cause
Remedy
Drive unit operates
Spanner broken
Replace the spanner.
but spanner does not move.
or damaged.
Note:
Top of spanner
contains fail-safe area
that is designed to
break in event of overload.
Spanner operation
Fasteners loose.
Check tightness of all
rough or erratic.
screws and other fasteners.
Parts bent, worn
Disassemble and inspect
or
damaged.
roller cassette. Clean,
lubricate and replace
parts as needed.
12
Summary of Contents for WCR4000
Page 1: ...Instruction Sheet WCR4000 Roller Cassette L4021 English GB Rev B 09 2013...
Page 2: ...2...
Page 17: ...17 NOTES...
Page 18: ...18 NOTES...
Page 19: ...19 NOTES...