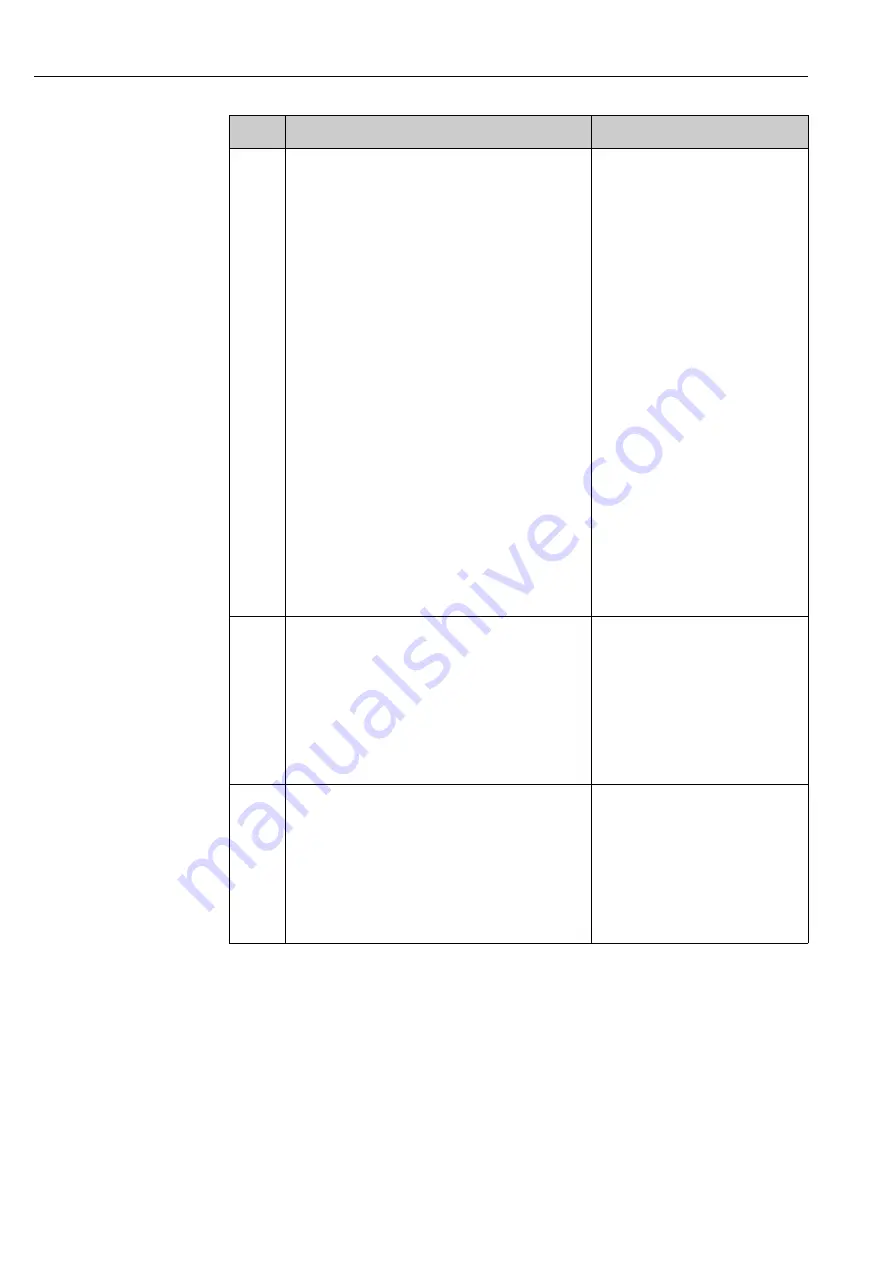
Maintenance
TOCII CA72TOC
78
Hauser
7
1.
Rinse the suction hose of the acid
pump.
2.
Guide the suction tube into the acid
feeder tank.
3.
Place the hose cassette into P3.
4.
Use the dosing nozzle of the injector
to expand the hose end.
5.
Press the [>] key until acid enters the
strip chamber.
6.
Make sure medium is being
conveyed evenly in the suction hose.
You can now check the contact pressure
of the hose cassette:
1.
Release the adjusting screw (item 6)
until no more medium is conveyed.
2.
Now tighten the adjusting screw
until the unit starts to pump medium
again. Even medium delivery should
be visible across all pump heads.
3.
Tighten the adjusting screw one
revolution.
Continue with Step 8 for versions "with
predilution".
Continue with Step 9 for versions
"without predilution".
8
Dilution stabilizes for 120 s.
9
Automatic filling of the strip chamber,
conditioning of the strip chamber with
active acid dosing
Measuring operation is started
automatically.
Step
Display
Description
REPLACE HOSE P3
[E] TO CONFIRM
INSERT ACID SUCT. HOSE IN ACID FEEDER;
INSERT HOSE CASSETTE IN P3
FILL HOSE
UNTIL ACID ENTERS STRIP CHAMBER
[>] START/STOP PUMP 3 (100%)
AND RE-CONNECT THE HOSE.
XXX
REPLACE HOSE P3
STABILIZE DILUTION
XX
REPLACE HOSE P3
FILL STRIP AND SEPARATION CHAMBERS
Summary of Contents for TOCII CA72TOC
Page 2: ...Endress Hauser...
Page 136: ...TOCII CA72TOC 136 Endress Hauser...
Page 139: ......
Page 140: ......