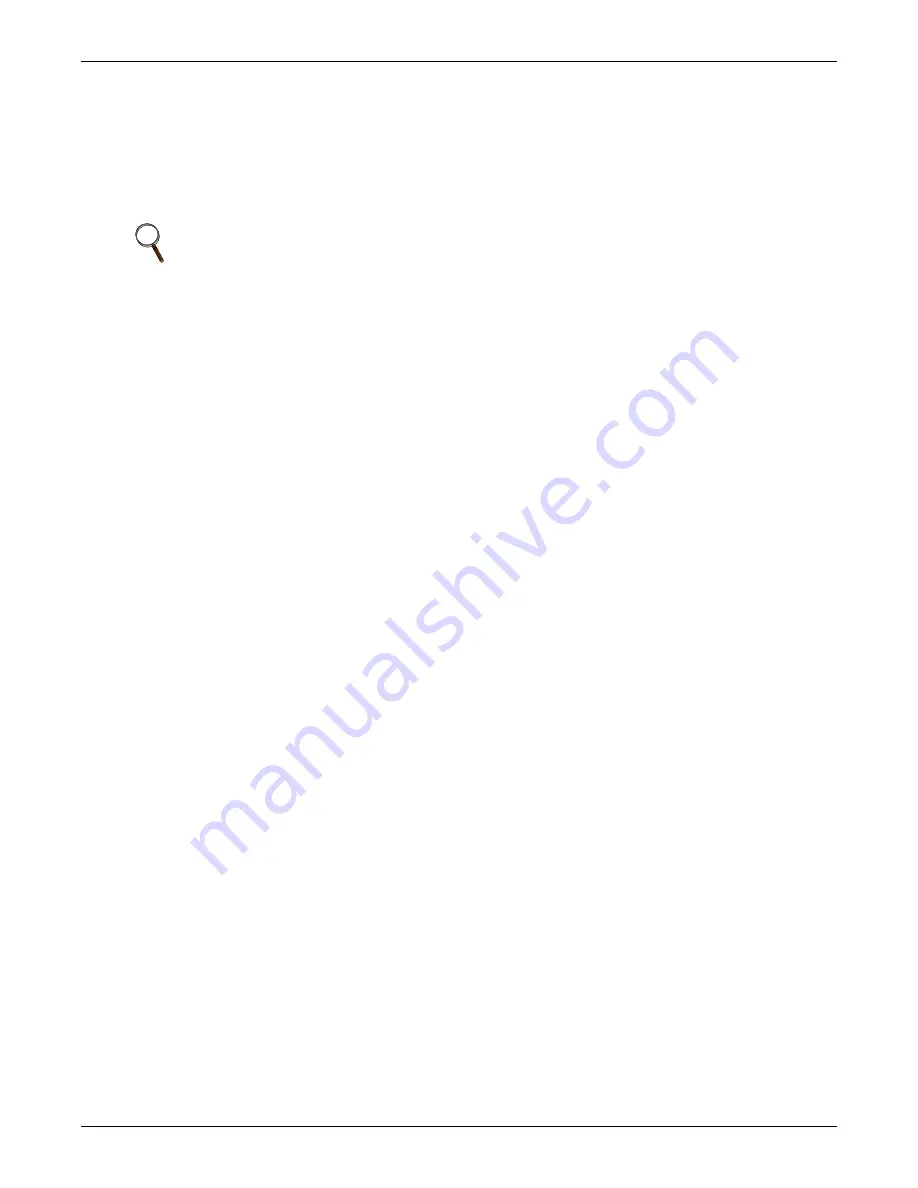
System Testing And Maintenance
Liebert
®
Mini-Mate2
™
60
Replace a Failed Compressor
Proper procedures to remove and replace the failed compressor are:
1. Disconnect power
2. Attach suction and discharge gauges to access fittings.
3. Recover refrigerant using standard recovery procedures and equipment. Use a filter-drier when
charging the system with recovered refrigerant.
4. Remove failed compressor.
5. Install replacement compressor and make all connections. Use a flow of dry nitrogen through the
piping during brazing to prevent formation of copper oxide scale inside the piping. Copper oxide
forms when copper is heated in the presence of air. POE oil will dissolve these oxides from inside
the copper pipes and deposit them throughout the system, clogging filter driers and affecting
other system components.
A pure dry nitrogen flow of 1-3 ft
3
/min (0.5-1.5 l/s) inside the pipe during brazing is sufficient to
displace the air. Control the flow using a suitable metering device.Pressurize and leak test the
system at approximately 150 psig (1034kPa) pressure.
6. Follow manufacturer's instructions for clean out kits.
7. Evacuate the system twice to 250 microns. Break the vacuum each time with clean, dry nitrogen.
8. Evacuate the system a third time to 250 microns.
9. Charge the system with refrigerant (R-407C) based on requirements of the evaporator,
condensing unit and lines. Refer to the unit nameplate.
10. Apply power and operate the system. Check for proper operation. Refer to
9.3.3 Steam Generating Humidifier—Operation Procedures
Steam generating humidifiers operate efficiently over a wide range of water quality conditions and
automatically adjust to changes in the conductivity of water. The system will automatically drain and
refill to maintain an amperage setpoint and alert the operator when the humidifier canister needs to
be replaced.
The humidifier RUN/DRAIN switch is located in the humidifier assembly. This switch should be in
the RUN position when the humidifier is in normal operation, and in the DRAIN position when a
manual drain sequence is required. The electronic control board for the humidifier is also located in
the humidifier assembly. When the unit is energized, power is available to humidifier. Operations
involves the following steps:
1. During startup, when the humidity control calls for humidification, the fill valve will open,
allowing water to enter the canister. When the water level reaches the electrodes, current flows
and the water will begin to warm. The canister fills until the amperage reaches the setpoint and
the fill valve closes. As the water warms, its conductivity increases and the current flow, in turn,
rises. If the amperage reaches 115% of the normal operating amperage, the drain valve opens and
flushes some of the water out of the canister. This reduces electrode contact with the water and
lowers the current flow to the amperage setpoint. Boiling soon commences and the canister
operates normally.
2. If the conductivity of the water is low, the canister fills and the water level reaches the canister
full electrode before the amperage setpoint is reached. The humidifier stops filling to prevent
overflow. Boiling should commence in time. As water is boiled off, the mineral concentration in
the canister increases and current flow also increases. The canister eventually reaches full output
and goes to normal operation. No drain is permitted until then.
3. When full output is reached the circuit board starts a time cycle which is factory set at 60 seconds.
During this repeating time cycle, the fill valve will open periodically to replenish the water being
boiled off and maintain a “steady state” output at the setpoint. The amperage variance will
depend on the conductivity of the water.
NOTE
Release of refrigerant to the atmosphere is harmful to the environment and unlawful.
Refrigerant must be recycled or discarded in accordance with federal, state and local
regulations.
Summary of Contents for PFH020A-L
Page 3: ......
Page 74: ...Liebert Prop Fan Condensing Unit 50 Hz and 60 Hz Installer User Guide ...
Page 77: ...5 Troubleshooting 37 Vertiv Liebert PFH Installer User Guide ii ...
Page 86: ...Figure 2 6 General piping arrangement Vertiv Liebert PFH Installer User Guide 9 ...
Page 105: ...Vertiv Liebert PFH Installer User Guide 28 This page intentionally left blank ...
Page 109: ...Vertiv Liebert PFH Installer User Guide 32 This page intentionally left blank ...
Page 116: ......