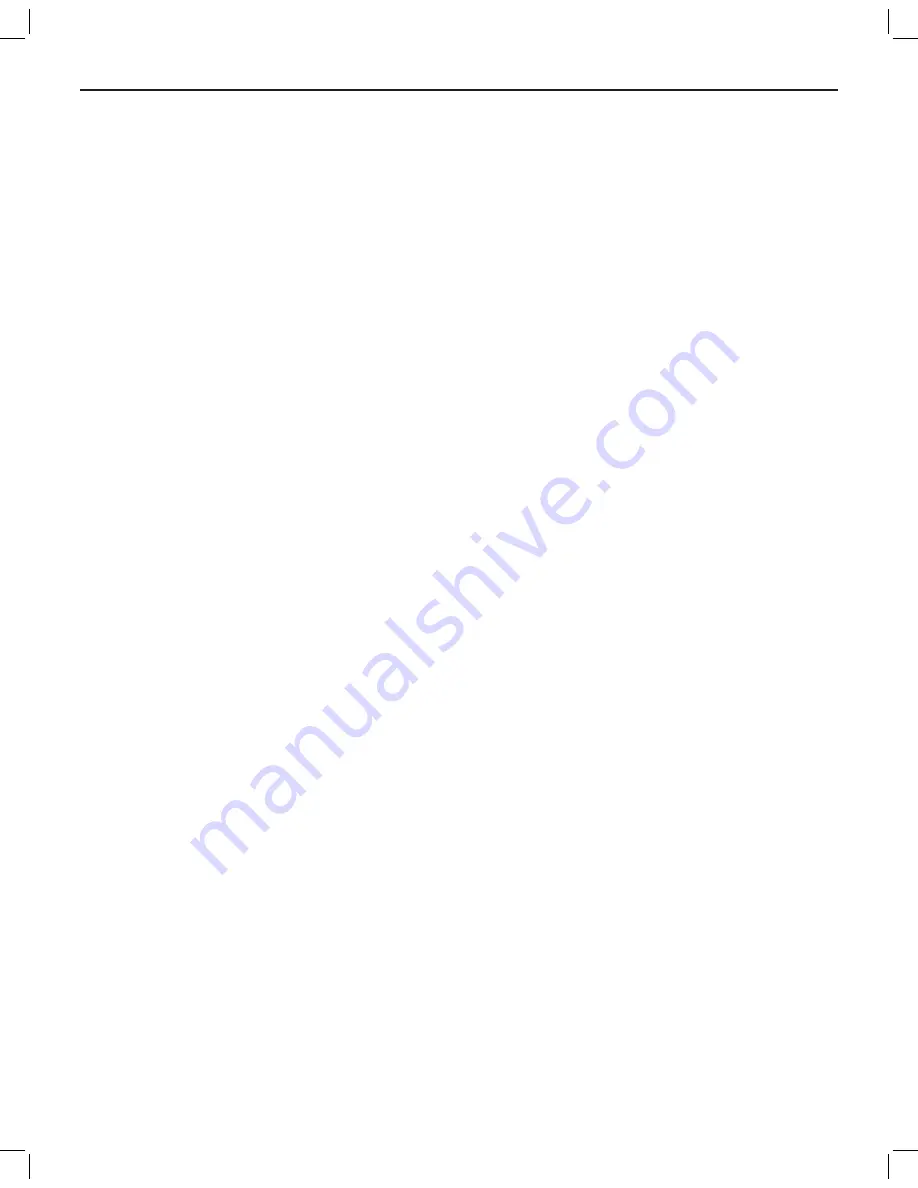
CM-2201 Troubleshooting
17
©2015 Nelson Heat Tracing Systems
www.nelsonheaters.com GA2497 Rev. 2
2. Temperature Verification Continued
To verify the Controller:
TURN THE POWER TO THE CONTROLLER OFF BEFORE
PROCEEDING!
a) Disconnect the RTD wiring from the input terminals.
b) Connect a 100 Ω resistor across the source or sense
terminal and common. Insert a jumper between the
source and sense terminals.
c) Apply power to the controller. The indicated or displayed
temperature should be about 32°F (0°C), depending on
the actual resistance of the test resistor if RTD TYPE is
set to 100Ω Platinum. Any resistor may have a +/- 10%
tolerance.
3. Unstable Temperature
An erratic indication of temperature can be caused by
several factors external to the controller. The controller’s
accuracy and resolution will result in an indicated
temperature change of a couple of degrees if the measured
resistance temperature falls between two discrete values
(this is sometimes referred to as quantization error).
If the instability is excessive, check:
a) Wire used for extension of the RTD should be three-wire,
twisted and shielded with the shield grounded at the
controller only. Each of the three lead wires must be of
the same gauge.
b) The ideal installation has a separate conduit for the
RTD leads (if they have been extended).It is not usually
a problem to run low signal levels in the same conduit
as the power leads even in high power applications, as
long as the RTD wire is a twisted, shielded type with an
insulation rating equal to or greater than the highest
voltage in the conduit. Follow the proper Electrical Code
requirements for your particular installation.
c) Check the specifications for the particular cable
being used to ensure that it does not have excessive
capacitance when used in long lengths. This can cause a
temperature offset between what the controller reads and
what the RTD actually measures. This again is normally
not a problem since the controller compensates for all
but the worst cases of this.
3. Unstable Temperature Continued
d) Check, one by one, if the all RTD leads are connected to
the connector.
e) Lastly, it is possible for the RTD itself to fail on an
intermittent basis but this failure mode should be
considered unusual. This kind of failure is probably the
most difficult to find, but fortunately, it is also the least
likely as a failure mechanism.
9.2 Ground Fault
Ground fault warning/alarms can be due to incorrect
installation as well as leakage resulting from wet system
components or faulted cables.
The CM2201 Controller detects ground faults by summing
the outgoing and return trace currents through an internal
current transformer. Under normal operating conditions (no
ground fault condition), this current will be zero. When there
is a flow of current from one of the trace supply wires to
ground, a ground fault condition occurs.
If a ground fault alarm is present on start-up of a new
installation, it is likely due to a wiring error or damaged
cable. To verify this condition:
a) Check that the heating circuit neutrals return to
the controller and are not connected directly to the
distribution panel. This can be a common problem if the
installation is a retrofit situation.
b) On paralleled circuits, be certain that ALL neutrals
return. The late addition of a circuit may not be obvious
.
Note:
The controller monitors the integrity of the ground
fault (GF) detection. If a fault is detected, the controller will
generate a GFI warning/alarm, depending on the settings.
9.3 Common Warnings/Alarms - What to Look for
The CM-2201 has a wide range of warning and alarming
features that may be selectively enabled or disabled to
allow the monitoring and indication of trouble conditions.
Described below are the different warning and alarm
conditions available on the CM2201, their meanings, and
possible causes. The warning settings must be below alarm
settings. If an alarm is activated, the two low power SSRs
will be activated.