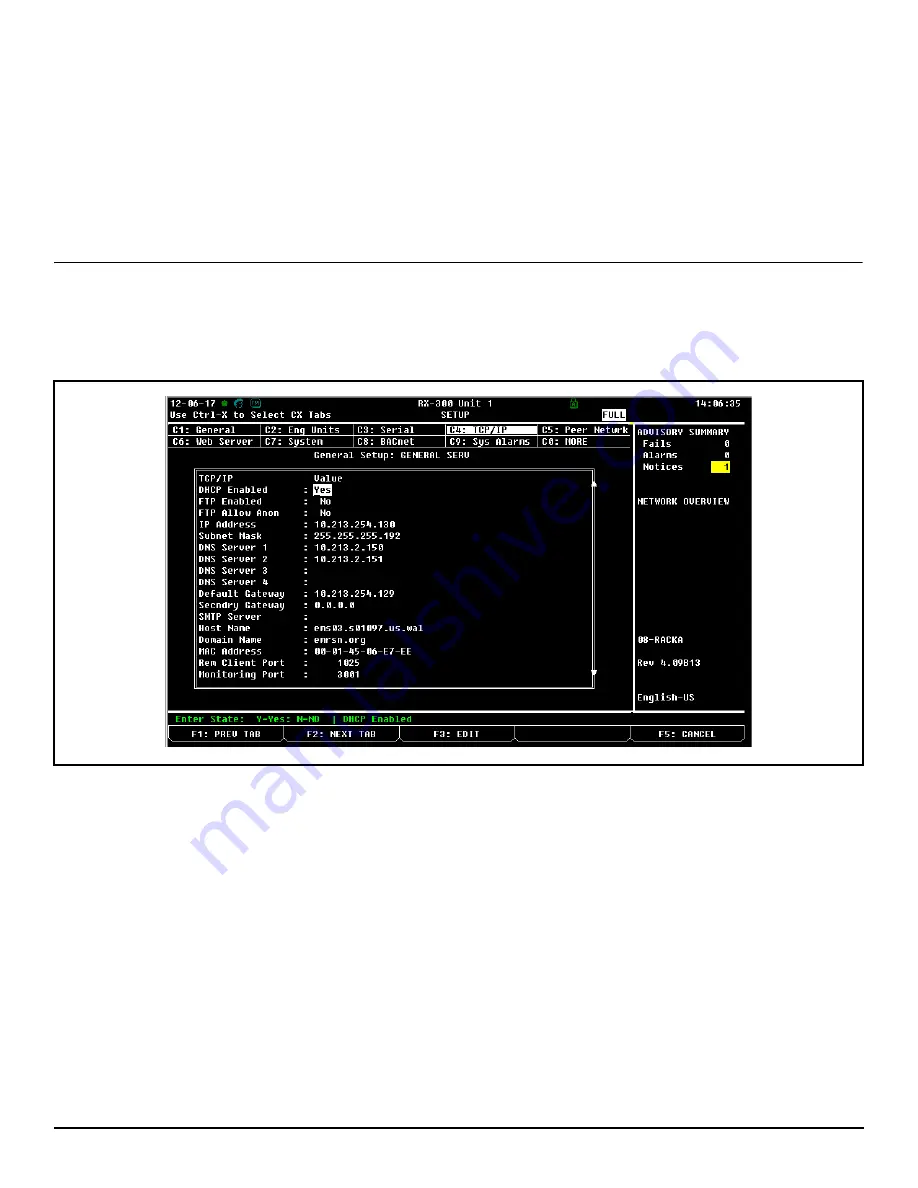
Configure E2E BACnet Settings
E2 Setup • 55
4. Three fields will become visible underneath the COM4 Connection that pertain to the way the device communicates:
•
COM4 DevId -
This is the E2E BACnet Device ID; set this to a unique number from all other BACnet nodes on the network in
the range of
0-4194303
. Usually setting the E2E Device ID the same number as the MSTP MAC is sufficient.
•
COM4 MSTP MAC -
This is the E2E BACnet MSTP MAC address; set this to a unique number for E2E in the range of
1-127
.
Each BACnet device on the network must have its own unique MSTP MAC in order to communicate.
•
COM4 Baud
-
Default setting is 9600; this must be changed to
19.2k
(all devices connected to the same COM port should be set
to the same baud rate)
15.2. Configure E2E BACnet Settings
After setting up the BACnet MS/TP port then the BACnet network settings must be configured.
1. From the Home screen on E2E press
Alt-T
on the keypad to navigate to this screen:
2. Press
Ctrl-8
to reach the
BACnet
tab:
Figure 15-2
- E2E TCP/IP Settings
Summary of Contents for iPro
Page 1: ...iPro Case Controller Installation and Operation Manual FW Version 1 01 026 1738 Rev 1 ...
Page 2: ......
Page 4: ......
Page 8: ......
Page 78: ...70 iPro Case Controller I O Manual FM V1 01 026 1738 Rev 1 17 Appendix iPro Connection Detail ...
Page 79: ......