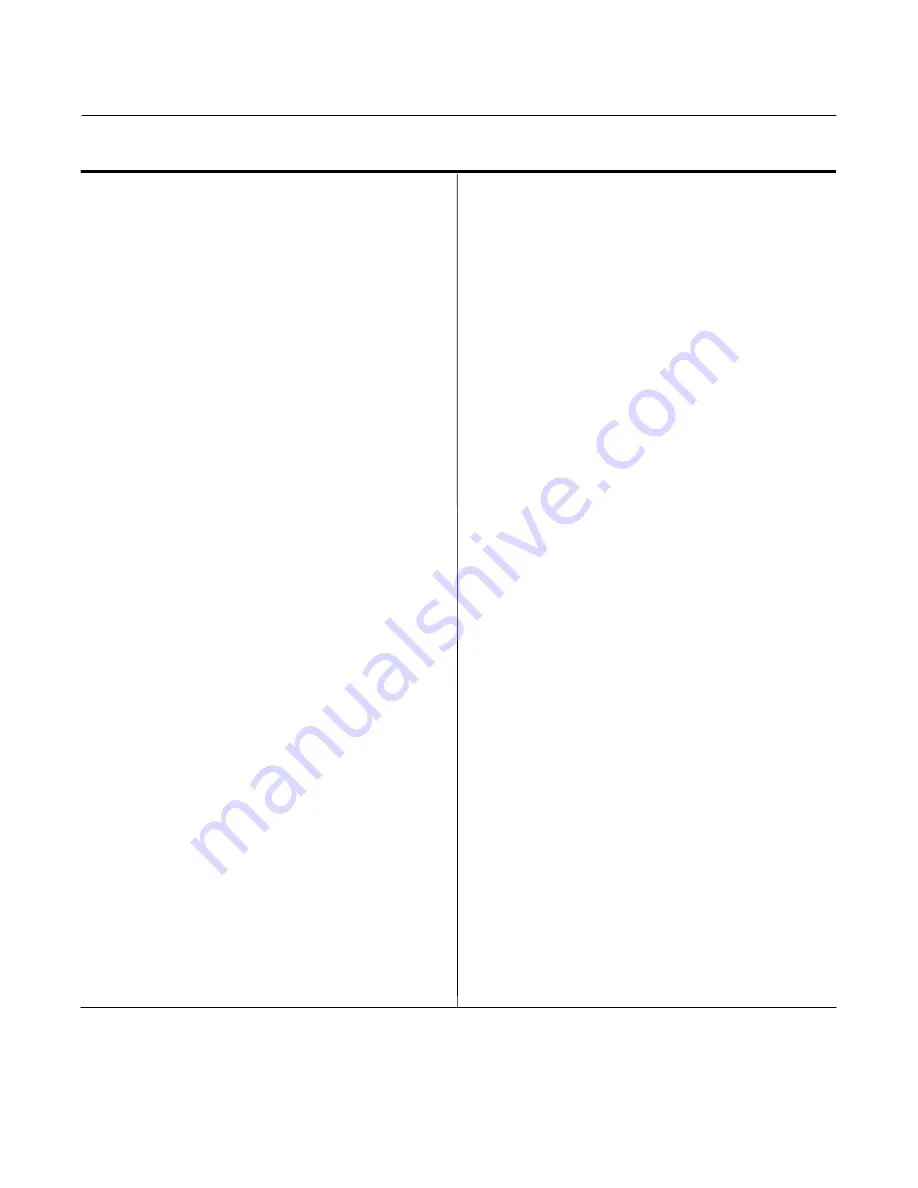
Instruction Manual
D103785X012
Introduction
June 2017
5
Table 1‐2. Specifications
Available Mounting
DVC6000 HW2 digital valve controllers can be
mounted on Fisher and other manufacturers rotary
and sliding‐stem actuators
DVC6005 HW2:
Base unit for 2 inch pipestand or wall
mounting
J
DVC6015:
Remotely mounted feedback unit for
sliding‐stem applications
J
DVC6025:
Remotely mounted feedback unit for
rotary or long‐stroke sliding‐stem applications or
J
DVC6035:
Remotely mounted feedback unit for
quarter‐turn rotary applications
Mounting kit required for mounting feedback unit on
actuator
Mounting the instrument vertically, with the vent at
the bottom of the assembly, or horizontally, with the
vent pointing down, is recommended to allow
drainage of moisture that may be introduced via the
instrument air supply.
Communication Protocol
J
HART 5 or
J
HART 7
Input Signal
Point
-
to
-
Point
Analog Input Signal:
4-20 mA DC, nominal; split
ranging available
Minimum Voltage Available at Instrument Terminals
must be 9.5 VDC for analog control, 10 VDC for HART
communication
Minimum Control Current:
4.0 mA
Minimum Current w/o Microprocessor Restart:
3.5 mA
Maximum Voltage:
30 VDC
Overcurrent protected
Reverse Polarity protected
Multi
-
drop
Instrument Power:
11 to 30 VDC at 10 mA
Reverse Polarity protected
Supply Pressure
Minimum Recommended:
0.3 bar (5 psig) higher
than maximum actuator requirements
Maximum:
10.0 bar (145 psig) or maximum pressure
rating of the actuator, whichever is lower
Medium:
Air or Natural Gas
Supply medium must be clean, dry and non-corrosive
Per ISA Standard 7.0.01:
A maximum 40 micrometer
particle size in the air system is acceptable. Further
filtration down to 5 micrometer particle size is
recommended. Lubricant content is not to exceed 1
ppm weight (w/w) or volume (v/v) basis.
Condensation in the air supply should be minimized.
Per ISO 8573-1
:
Maximum particle density size:
Class 7
Oil content:
Class 3
Pressure Dew Point:
Class 3 or at least 10
_
C less than
the lowest ambient temperature expected
Output Signal
Pneumatic signal as required by the actuator, up to
full supply pressure.
Minimum Span:
0.4 bar (6 psig)
Maximum Span:
9.5 bar (140 psig)
Action:
J
Double,
J
Single Direct or
J
Reverse
Steady‐State Air Consumption
Standard Relay
At 1.4 bar (20 psig) supply pressure:
Less than 0.38 normal m
3
/hr (14 scfh)
At 5.5 bar (80 psig) supply pressure:
Less than 1.3 normal m
3
/hr (49 scfh)
Low Bleed Relay
At 1.4 bar (20 psig) supply pressure:
Average value 0.056 normal m
3
/hr (2.1 scfh)
At 5.5 bar (80 psig) supply pressure:
Average value 0.184 normal m
3
/hr (6.9 scfh)
Maximum Output Capacity
At 1.4 bar (20 psig) supply pressure
:
10.0 normal m
3
/hr (375 scfh)
At 5.5 bar (80 psig) supply pressure:
29.5 normal m
3
/hr (1100 scfh)
Operating Ambient Temperature Limits
-40 to 85
_
C (-40 to 185
_
F) for base unit
-52 to 85
_
C (-62 to 185
_
F) for base unit utilizing the
Extreme Temperature option (fluorosilicone
elastomers)
-52 to 125
_
C (-62 to 257
_
F) for remote‐mount
feedback unit
Independent Linearity
Typical Value:
±
0.50% of output span
-continued-