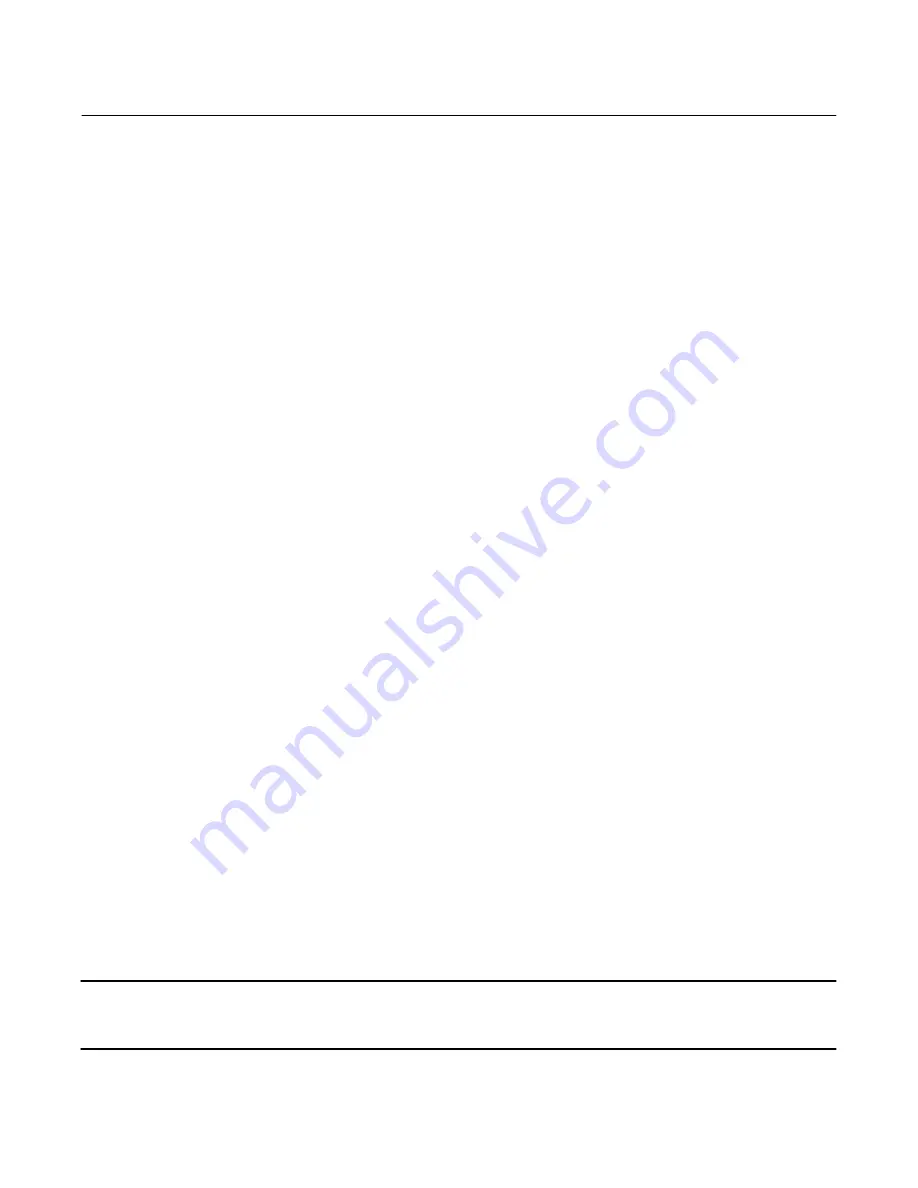
Instruction Manual
D200156X012
4194HA, HB, HC Controllers
July 2018
64
7. The process indicator should point out 50
±
3 percent of the input scale range. If not, loosen the screws in link 1 and
move the process indicator to 50
±
3 percent. Tighten the screws.
8. The controller output pressure should be:
c.
For 4194HA controllers
— 0.6
±
0.1 bar (9
±
1 psig) for a 0.2 to 1 bar (3 to 15 psi) output or 1.2
±
0.1 bar
(18
±
2 psig) for a 0.4 to 2 bar (6 to 30 psi) output.
d.
For 4194HB and HC controllers
— 0.0 bar (0 psig).
If necessary, adjust flapper leveling screw number 2 to obtain the required output pressure.
9. Adjust the process differential pressure to the differential pressure unit to 0 percent of the process differential
pressure scale range.
10. Adjust the process indicator to 0 percent on the process scale by loosening the zero adjustment locking screw and
turning the zero adjustment screw. Tighten the zero adjustment locking screw.
11. Adjust the process differential pressure to 100 percent of the scale range.
12. Note whether the process indicator is above or below 100 percent on the process scale.
13. Adjust the process indicator span adjustment as follows: clockwise to increase the span for a low indication and
counterclockwise to decrease the span for a high indication. To avoid overcorrection, only correct for
approximately
one‐half
of the error with the span adjustment screw.
100 percent marks. If the span adjustment screw is adjusted to its limit and the span is still too short or too long,
proceed with step 15. If proper span is achieved, proceed to step 16.
15. Within the process indicator subassembly, there are three holes for the connection of link 1. Use procedure (a.) or
(b.) below to make the coarse span adjustment with link 1.
a. If the span is short (process indication is low at 100 percent of input range), disconnect link 1 from the process
indicator subassembly, move the link to the lowest hole, and return to step 9.
b. If the span is long, (process indication is high at 100 percent of the input range), disconnect link 1 from the
process indicator subassembly, move the link to the highest hole, and return to step 9.
16. Adjust the process differential pressure to 50 percent of the process scale range. The process indicator should point
out 50
±
2 percent on the process scale range. If the process indicator error is
±
2 percent or less, proceed to step 19.
17. If the process indicator error is greater than
±
2 percent, loosen the two screws in the drive arm (key 322, figure 6‐2).
Then, lengthen or shorten the drive arm 6.3 mm (1/4 inch) and repeat steps 9 through 16.
18. Adjust the process indicator to within
±
1 percent of the 50 percent scale mark by loosening the zero adjustment
locking screw and turning the zero adjustment screw. Tighten the zero adjustment locking screw. This will
distribute the error over the entire process scale and keep all points within
±
1 percent of the process scale span.
19. Adjust the process differential pressure to 0 and 100 percent of the process scale range to make sure the process
indicator is still within
±
1 percent of the 0 and 100 percent scale marks.
20. Perform the flapper alignment procedure and, if necessary, the appropriate remote set point calibration procedure
Flapper Alignment
Note
Perform the process indicator zero‐and‐span calibration procedure and, if necessary, the remote set point calibration procedure
before the flapper alignment.