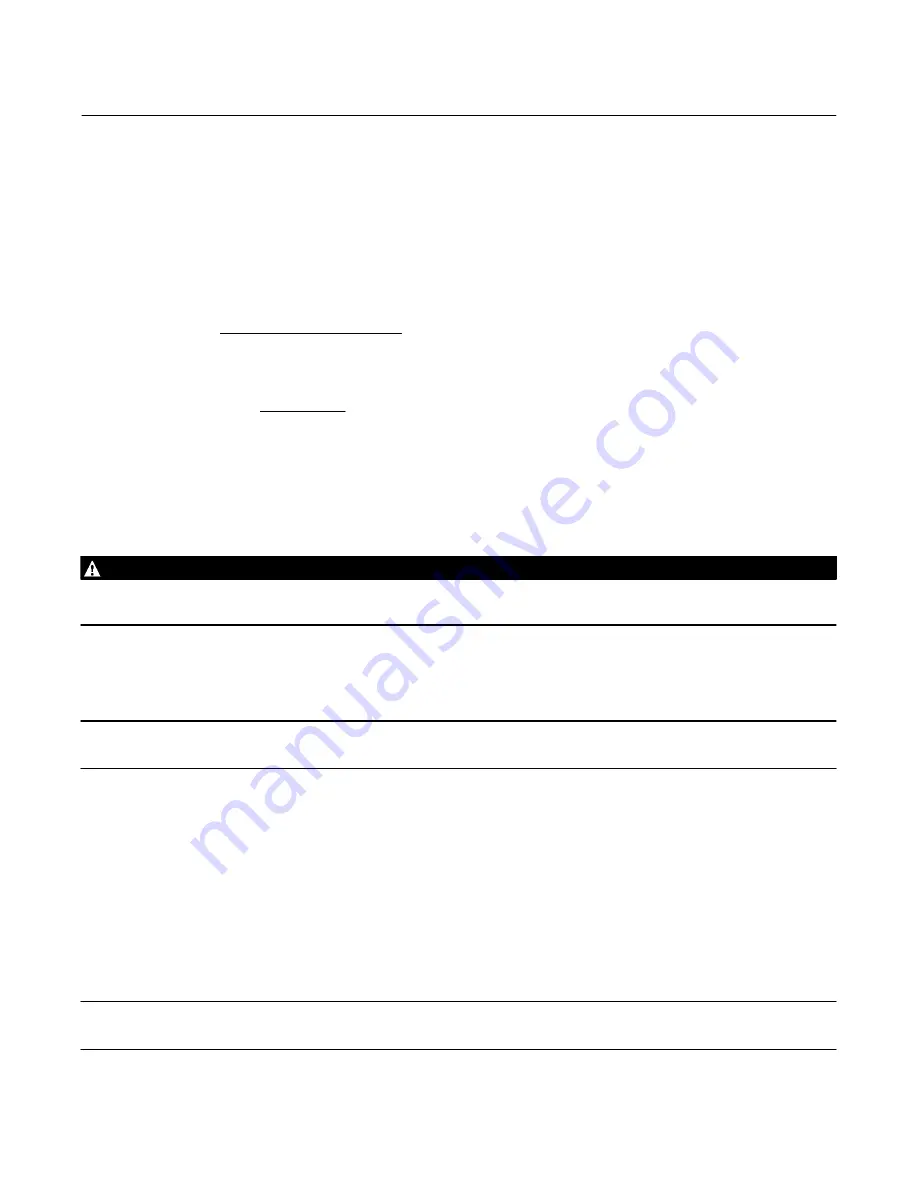
Instruction Manual
D200156X012
4194HA, HB, HC Controllers
July 2018
17
D
remote set point:
the remote set point connection.
b. Adjust the pressure source until the set point indicator reaches the desired set point. Remember: Increasing
the remote set point pressure increases the set point of direct‐acting controllers.
3. Set the proportional band adjustment to 100 percent for fast processes. For slow processes, calculate the
proportional band percentage from the equation below:
Proportional
Band
Adjustment
+
200
AllowableOvershoot
PressureSpan
For example:
200
2Psig
30Psig
^
13%
4. Create a load upset by momentarily changing the set point. Check for system cycling. If the system does not cycle,
lower the proportional band setting (thus raising the gain) and disturb the system again by changing the set point.
Continue this procedure until the system cycles. At this point, double the proportional band setting (proportional
band setting X 2).
Calibration for 4194HA Controllers
WARNING
To avoid personal injury or property damage resulting from the sudden release of pressure, do not exceed the operating
limits given in this manual.
General Calibration Instructions
Note
If the controller has the auto/manual option, be sure the controller is in the automatic mode before performing calibration.
If the prestartup checks revealed faulty controller operation, perform the calibration described in this section. These
instructions are valid for either shop or field calibration, provided open process loop conditions exist. Unless otherwise
noted, key numbers are found in figure 6‐1.
Process Indicator Zero‐and‐Span Calibration
Before starting this procedure:
D
Provide a regulated process differential pressure to the differential pressure unit.
D
Note
Any change in process indicator span will require readjustment of the process indicator zero adjustment screw.