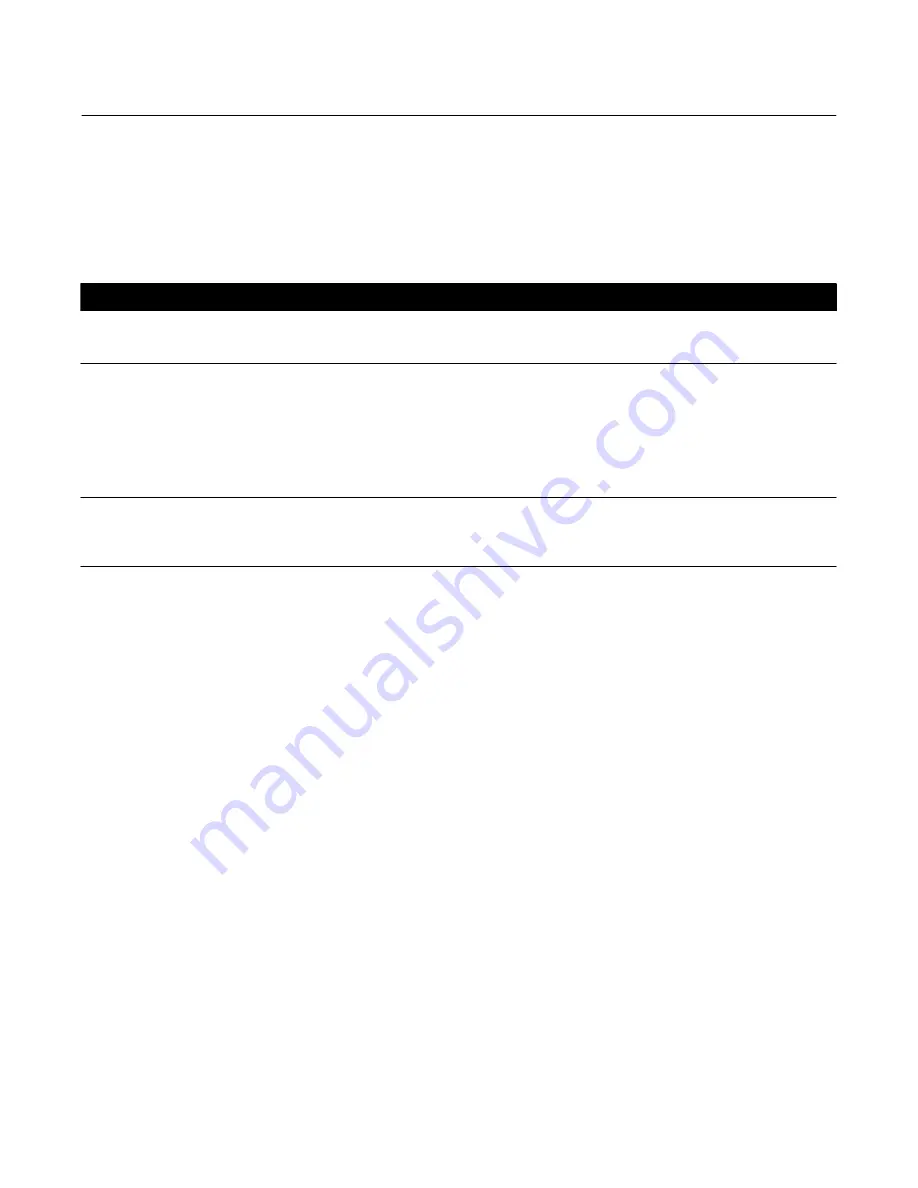
Instruction Manual
D200156X012
4194HA, HB, HC Controllers
July 2018
71
6. Attach links A and B (keys 116 and 126) to the arms of the replacement pivot assembly B in the positions noted in
7. Perform the remote set point maintenance calibration procedure in this section. Also, perform the appropriate
controller calibration procedure in Section 3 or 4.
Drive Flexure
CAUTION
Avoid bending or kinking the drive flexure during this procedure. Bending or kinking the drive flexure can result in product
damage and impaired performance.
1. Disconnect the flexure (key 79) from the drive bracket (key 121) and from the adjustment arm of pivot assembly A.
Remove the screws and washers (key 12 and 13); remove the flexure.
2. Set remote set point pressure at 50 percent of input span.
Note
The adjustment arm of the pivot assembly turns on a bushing at each end of the shaft supporting the adjustment arm. In the next
step, position the shaft so both bushings ”float” inside the bearings and do not rest against the end of either bearing.
3. Connect the new flexure making sure it stays straight and horizontal. Before tightening down the drive flexure, set
pivot A in the middle of the bushing end play. Tighten down the drive flexure to hold the pivot in that position. Do
not kink or twist the flexure when tightening the screws.
4. Decrease the remote set point pressure to 0 psig.
5. After replacing parts, refer to the various maintenance calibration procedures (process zero‐and‐span adjustment,
flapper alignment).
Remote Set Point Tubing
1. Decrease the remote set point pressure to 0 psig.
2. Disconnect the pressure connection (key 93) into the pedestal assembly (key 105) and the connection to the case
exterior at the top of the case.
3. Remove the tubing (key 104).
4. Install the replacement tubing and reconnect the two pressure connections.
5. Apply full remote set point pressure and check for leaks.
Link A
1. Note where link A (key 116) is connected (figure 6‐3). Disconnect both ends of the link from the lever arms on the
two pivots.
2. Loosen the screw in the replacement link and adjust the length to match the link being replaced. Tighten the screw.
Refer to figure 6‐3 for correct orientation of the link.
3. Attach the replacement link to the two lever arms in the same position as noted in step 1.
4. After replacing parts, refer to the various maintenance calibration procedures (process zero‐and‐span adjustment,
flapper alignment).