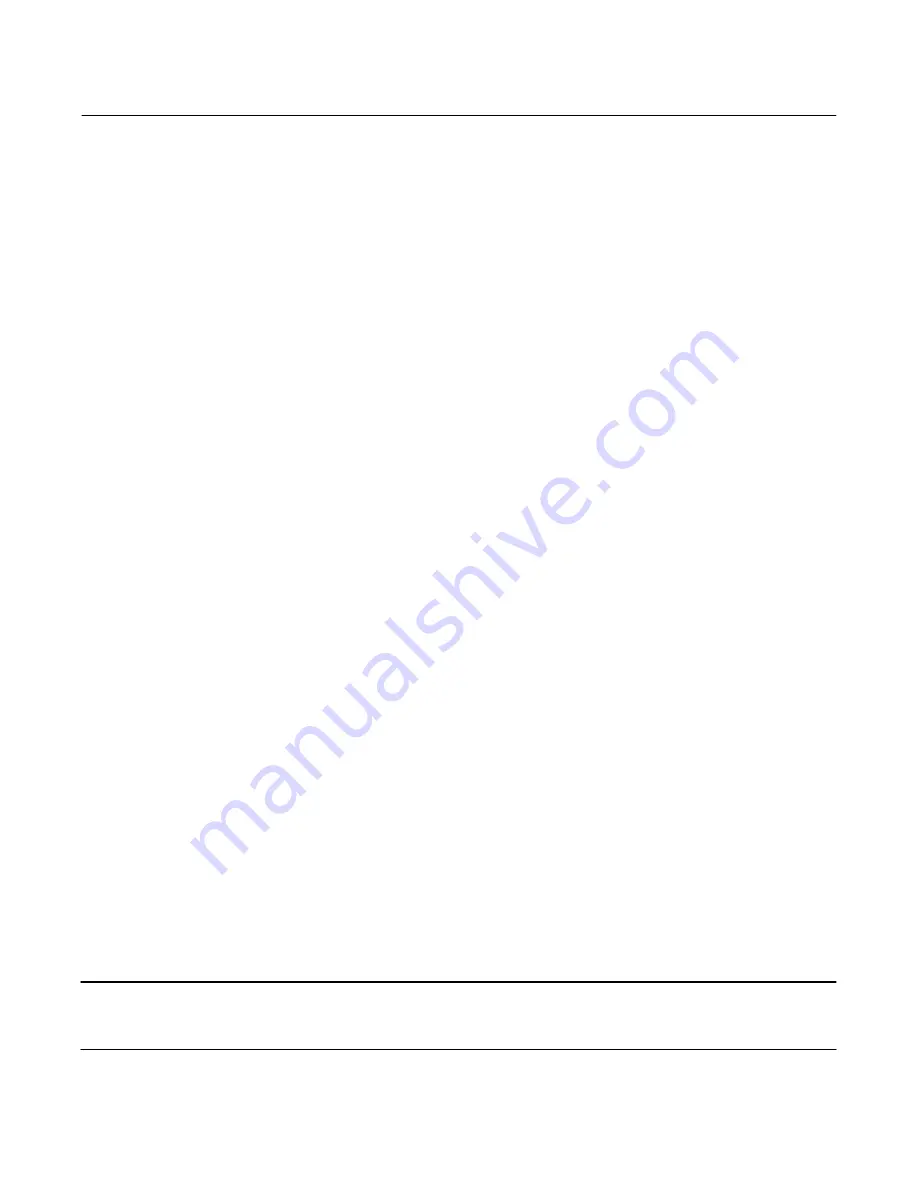
Instruction Manual
D200156X012
4194HA, HB, HC Controllers
July 2018
18
Refer to figure 3‐1 for location of adjustments.
1. Remove two screws (key 6) and lift off the proportional band indicator cover (key 36).
2. Set the proportional band between DIRECT and REVERSE.
3. The process indicator should be aligned with the indicator subassembly as shown in figure 5‐6. If not, loosen the
zero adjustment locking screw and adjust the fine zero adjustment to align the process indicator and indicator
subassembly. See figure 6‐4.
4. Adjust the process differential pressure until the controller indicates 50 percent of the input range.
5. The process indicator should point to 50 percent of the process scale range. If not, loosen the drive arm locking
screw (key 331, figure 6‐2) that holds the drive arm (key 322) to the shaft extension (key 321) and readjust the drive
arm on the shaft until the process indicator points to 50 percent of the process scale range. Tighten the drive arm
locking screw.
6. Adjust the process differential pressure to the lower limit of the input span. Note the position of the process
indicator.
7. If necessary, adjust the process indicator to the lowest limit of the input scale by loosening the zero adjustment
locking screw and turning the zero adjustment screw.
8. Adjust the process differential pressure to the upper limit of the input span. Note whether the process indication is
above or below the upper limit of the process scale.
9. Adjust the span screw as follows: Clockwise to increase span for a low indication or counterclockwise to decrease
span for a high indication. Adjust the span screw to correct one‐half the error.
10. Repeat steps 6 through 9 until the error is eliminated.
11. Adjust the process differential pressure to 50 percent of the input range. The process indicator should point to the
mid‐scale value within
±
1 percent of the input span. If the process indicator does not point to the proper value,
select the appropriate instructions, below:
D
If the process indicator error at mid‐range is greater than
±
1 percent but not greater than
±
2 percent, turn the
zero adjustment screw to bring the process indicator within
±
1 percent at mid‐range. Then, check the process
indicator accuracy at the lower and upper scale limits, to verify it is within
±
1 percent of the input span.
After adjusting the process indicator to
±
1 percent at the low, mid‐range, and upper scale limits, proceed with
D
If the process indicator error at mid‐range is greater than
±
2 percent, loosen the two screws in the drive arm (key
322, figure 6‐2) and lengthen or shorten the drive arm approximately 6.3 mm (1/4‐inch). Then, repeat steps 6
through 11.
After adjusting the process indicator to
±
1 percent at the low, mid‐range, and upper scale limits, proceed with
12. Perform the flapper alignment procedure.
Install the proportional band indicator cover (key 36) and tighten the two
screws (key 6).
Remote Set Point (suffix letter M) Zero‐and‐Span Adjustment
Refer to figure 3‐1 for location of adjustments. Refer to figures 6‐1 and 6‐2 for key number locations.
Note
Any adjustment of the set point span adjustment screw will require readjustment of the set point zero adjustment screw. Refer to
figure 3‐1.