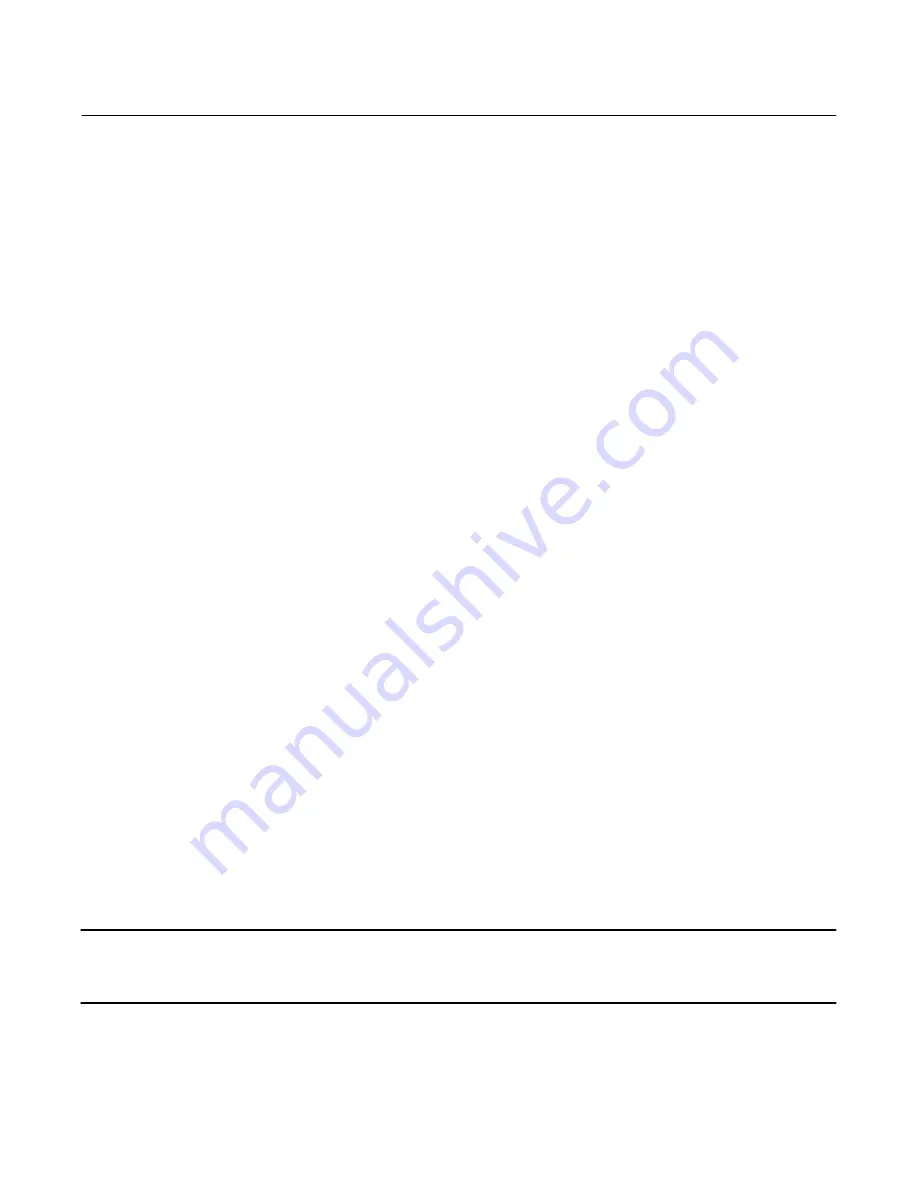
Instruction Manual
D200156X012
4194HA, HB, HC Controllers
July 2018
53
5. Inspect the O‐ring on the relay nozzle tubing assembly (key 18) and replace it if necessary. Apply a suitable lubricant
(key 318) to the O‐ring.
6. Install the relay nozzle tubing assembly (key 18) by pushing it into the bore in the set point beam assembly.
7. Adjust the proportional band between DIRECT and REVERSE. Do this by aligning the tab on the proportional band
knob with the hole in the set point beam assembly as shown in figure 5‐10.
8. Position the proportional band knob, nozzle pivot and the set point beam assembly on frame. Install the relay
nozzle tubing nut loosely into frame manifold while positioning the nozzle in the center of the flapper as shown in
figure 5‐11.
9. Secure the set point pivot assembly (key 17) to the frame as shown in figure 5‐9. Install the screw and washer
(keys 19 and 20) through the frame (key 3) into the set point pivot bracket. Do not tighten.
(keys 19 and 20) through the frame (key 3) and into the relay nozzle tubing pivot bracket. Tighten both this screw
and the screw installed in step 9.
Make sure the nozzle remains centered on the flapper with the set point beam assembly resting snugly down on the
relay nozzle tubing assembly.
11. Tighten the nut on the relay nozzle tubing assembly (key 18) and apply full supply pressure to check for leaks with
the controller developing full output pressure.
adjustable set point pivot assembly and back the set screw out slightly so the set point beam assembly falls under
its own weight when pivoted upward, with minimum set point beam sideplay between the pivots. Tighten the
locking nut.
13. Install the set point beam bias spring (key 28) into the bore of the frame (key 3) and onto the spring seat on the set
point beam assembly (see figure 5‐9).
14. Attach link 3 to the set point beam assembly (key 23). See figure 5‐9.
15. Tighten the nut on the relay nozzle tubing assembly (key 18). Apply full supply pressure with the nozzle capped and
check for leaks.
16. For controllers with reset or rate (4194HB or 4194HC controllers), disconnect the supply pressure. Then, adjust the
reset adjustment to the CLOSED (4194HB) or OFF (4194HC) position and adjust the rate adjustment to the OFF
position.
Controller output pressure must be 0 bar (0 psig). Set the reset adjustment to 0.01 minutes per repeat and wait 30
seconds. Then, turn the reset adjustment to the CLOSED position (4194HB) or to the OFF position (4194HC).
17. Connect supply pressure and a regulated process differential pressure to the controller. Also, provide a means of
measuring controller output pressure.
18. Perform the appropriate process indicator zero‐and‐span calibration procedure and, if necessary, the remote set
Note
The following procedure (steps 19 through 29) matches the process indicator motion to the set point indicator motion so the
controller will control at set point at all positions on the process scale.
19. Adjust the proportional band to 40 percent DIRECT or REVERSE (direct or reverse action) depending on the desired
controller action.