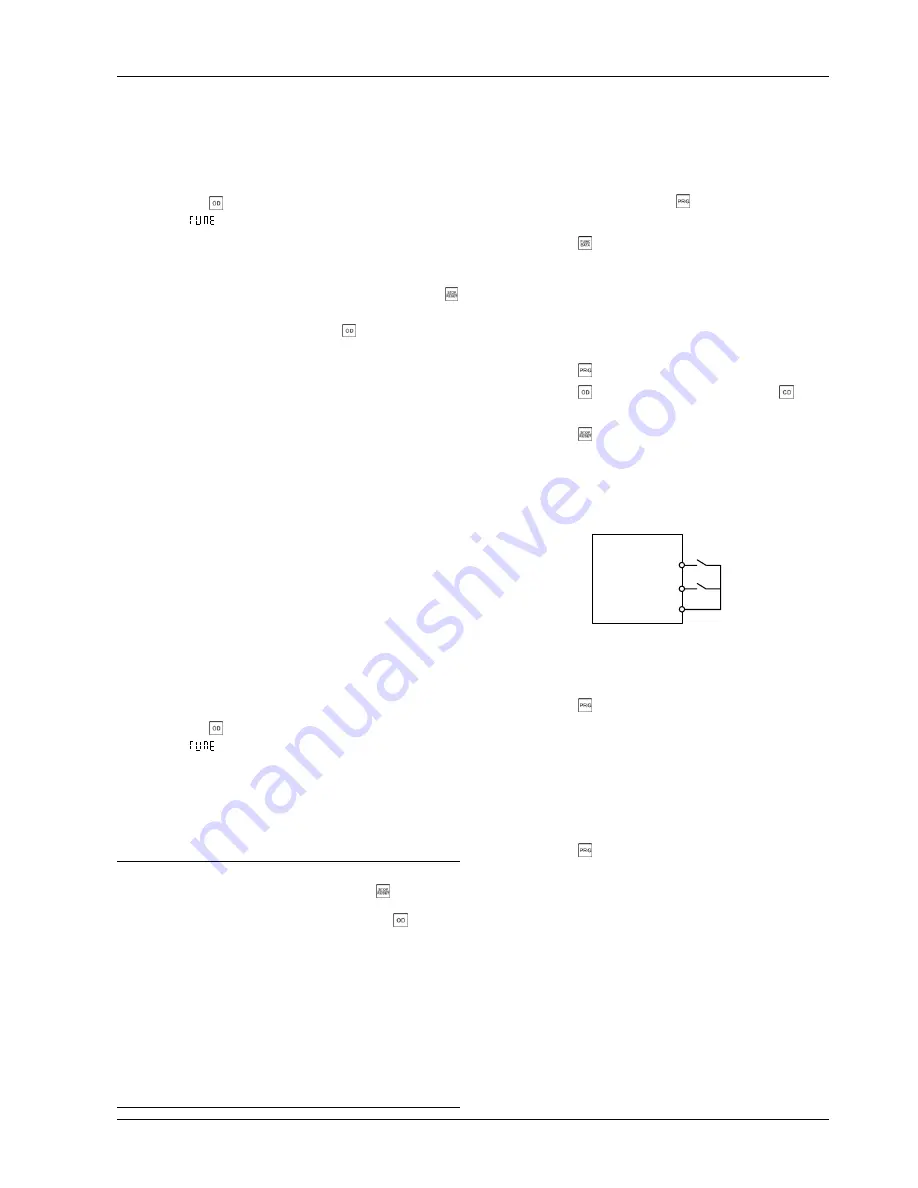
14 Chapter 4 Operation
EV3200 Door Control Inverter User Manual
3) Set motor type: Set F6.00 to 0 (asynchronous motor).
4) Input motor nameplate parameters: Input correct motor
nameplate parameters through parameters F6.01 ~
F6.03 and F6.05 ~ F6.06.
5) Set parameter tuning enable function: Set F6.07 to 1.
6) Press the
key to start motor tuning and the LED
displays "
". In the tuning state, the motor runs in a
fixed mode, so you need not interfere. After the tuning is
over, the inverter stops automatically, F6.07 will be
restored "0" and the settings of F6.08 ~ F6.13 will be
updated. If the tuning is obviously abnormal, press the
key to stop it. Check the connections and motor ratings,
then set F6.07 to 1 again. Press the
key to start
tuning.
A successful tuning can ensure correct control of the motor.
2. Tuning method in the case the load is synchronous motor.
The PG must be connected before synchronous motor
tuning.
Taking the inverter with default settings as an example:
1) Set general-purpose inverter keypad control mode: Set
F0.02 to 0.
2) Set the control mode as distance control 1 (close loop
vector control at this time): Set F0.01 to 1.
3) Set motor type: Set F6.00 to 1 (synchronous motor).
4) Input motor nameplate parameters: Input correct motor
nameplate parameters into F6.01 ~ F6.03 and F6.05 ~
F6.06.
5) Set the PG pulse No. per revolution: Set F4.01.
6) Set PG type. Set F4.00 to 1 (for UVW incremental
PG).
7) Set parameter tuning enable function: Set F6.07 to 1.
8) Press the
key to start motor tuning and the LED
displays "
". In the tuning state, the motor runs in a
fixed mode, so you need not interfere. After the tuning is
over, the inverter stops automatically, F6.07 will be
restored "0" and the settings of F6.08 ~ F6.13 and F4.03
will be updated.
A successful tuning can ensure correct control of the motor.
Note
1. If in tuning the keypad displays fault, press the
key to reset
the inverter, change the setting of F4.02, check the connections
and motor ratings, set F6.07 to 1 again, and press the
key to
start tuning.
2. In synchronous motor tuning, if the PG direction is reversed by
cable connection, the inverter will report E025 fault (PG fault). In
this case, exchange the connections of any two-phase cables of the
motor and restart the tuning.
3. For synchronous motors, you should conduct the tuning at least
twice, and see if the difference between the magnetic pole initial
angles (F4.03) obtained from the tuning is less than 10
°
. If
bigger than 10
°
, the error is unacceptable, you should restart the
tuning. If the difference is an integral multiple of 360
°
/motor
polarity pair number, the tuning result is acceptable.
4.2.2 Basic Operating Modes
1. Operating frequency settings, tuning and operating
control can be done via operation keypad.
1) In stopping state, press the key to enter
programming state and display parameter group F0.
2) Press the
key to enter the parameters in F0
parameter group.
3) Set the main parameters (other parameters can use
the defaults).
F0.01=0, speed control 1 (sensorless vector control)
F0.02=0, keypad control mode
4) Press the
key to return.
5) Press the
key for FWD running, press the
key
for REV running.
6) Press the
key , the inverter stops (decelerates to
stop).
7) Power-off.
2. Frequencies can be set and modified via the keypad and
operating control through control terminals.
EV3200
OD
COM
.
.
CD
.
k1
k2
Figure 4-3 Wiring
Connect power cables according to Figure 4-3, and switch
on after confirming the connection.
1) Press the
key to enter programming state.
2) Set the main parameters (other parameters can use
the defaults).
F0.01=0, speed control 1 (sensorless vector control)
F0.02=5, in terminal control mode, the operating
command is given via the control terminal. OD
controls FWD running and CD controls REV running
3) Press the
key to return to stopping status.
4) Switch on K1, the inverter runs forward.
5) Switch off K1 and switch on K2, the inverter runs REV.
6) Switch off K1 and K2, the inverter stops (decelerates
to stop).
7) Power-off.