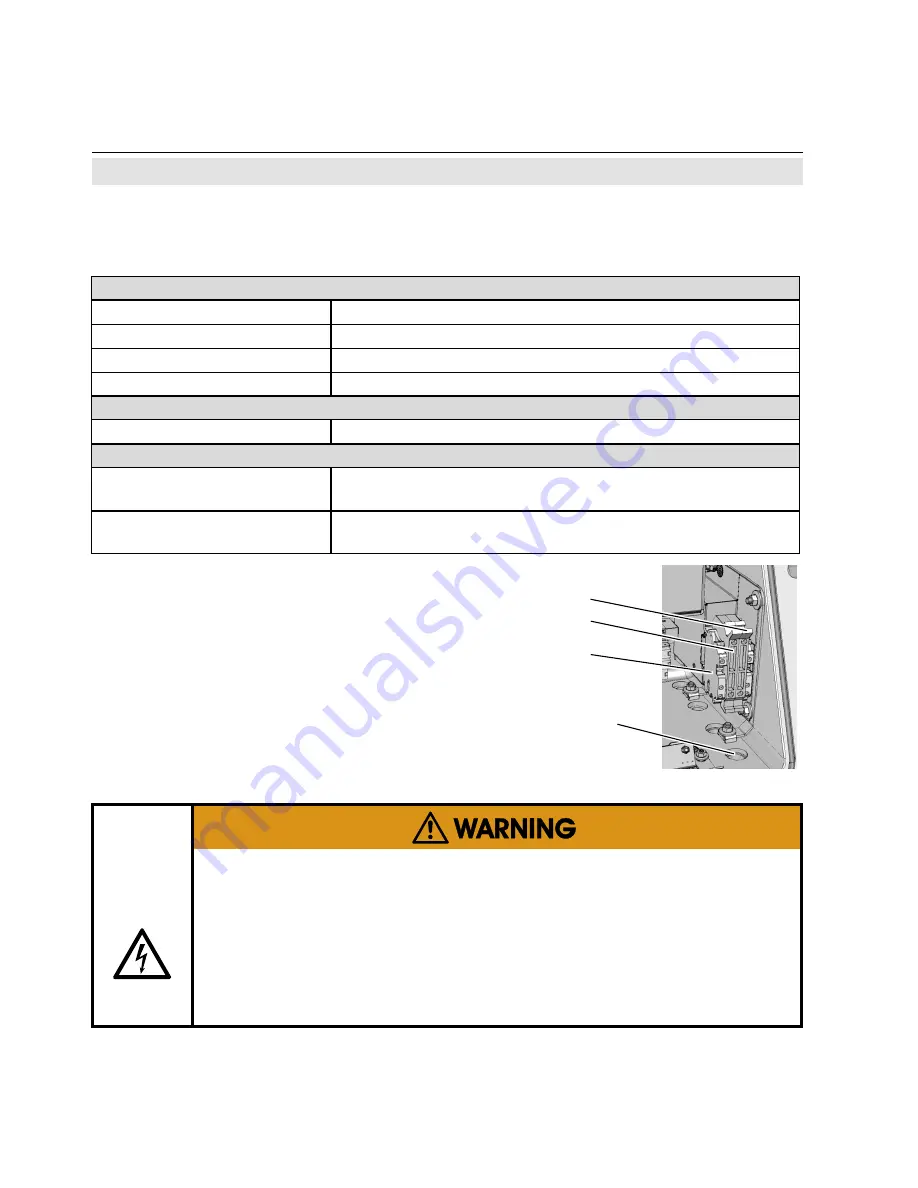
Emerson Process Management GmbH & Co. OHG
2-22
X-STREAM XEFD
Instruction Manual
HASXEDE-IM-EX
07/2017
Connecting the power cord
To install the cable proceed according to the
installation instructions for either conduits or
cable glands, given by the manufacturer.
Insert the power cord through the foremost
entry, strip the outer insulation, skin and
connect the conductors to the terminals (a
descriptive label is attached nearby the termi
-
nals), by inserting them from the bottom sides.
2.5 Installation – Electrical
The power cord is connected to screw-type terminals located inside the housing.
ELECTRICAL SHOCK HAZARD
Verify that the power supply at installation site meets the specification given
on the analyzer’s nameplate label, before installing the instrument!
Verify power cables are disconnected and/or instrument is de-energized
prior to working at the terminals!
Verify the power cord is layed with a distance of at least 1 cm (0.5") to any
signal cable to ensure proper insulation from signal circuits!
Electrical Connections
Power terminals
screw terminal with integrated fuse holders max 4 mm²
Supported wire cross sections 0.2 to 4 mm
2
(24 to 12 AWG) no need to use wire end sleeves
Cable skinning length
8 mm (0.315 inch);
Tightening torque, min .
0.5 Nm (4.4 in.lb)
Power Inlet Fuses
Data
AC 230 V / T 4 A / 5x20 mm
Cable Inlets
Variations
approved, M20 x 1,5, Cable glandes, min. IP 66, or
conduits with adaptors (metric-2-NPT)
Outer cable diameter
(cable glands)
depending on cable gland
Power cord entry
L= Line
N=Neutral
PE=Protective Earth
Fig. 2-16:
Power terminals
L
PE
N