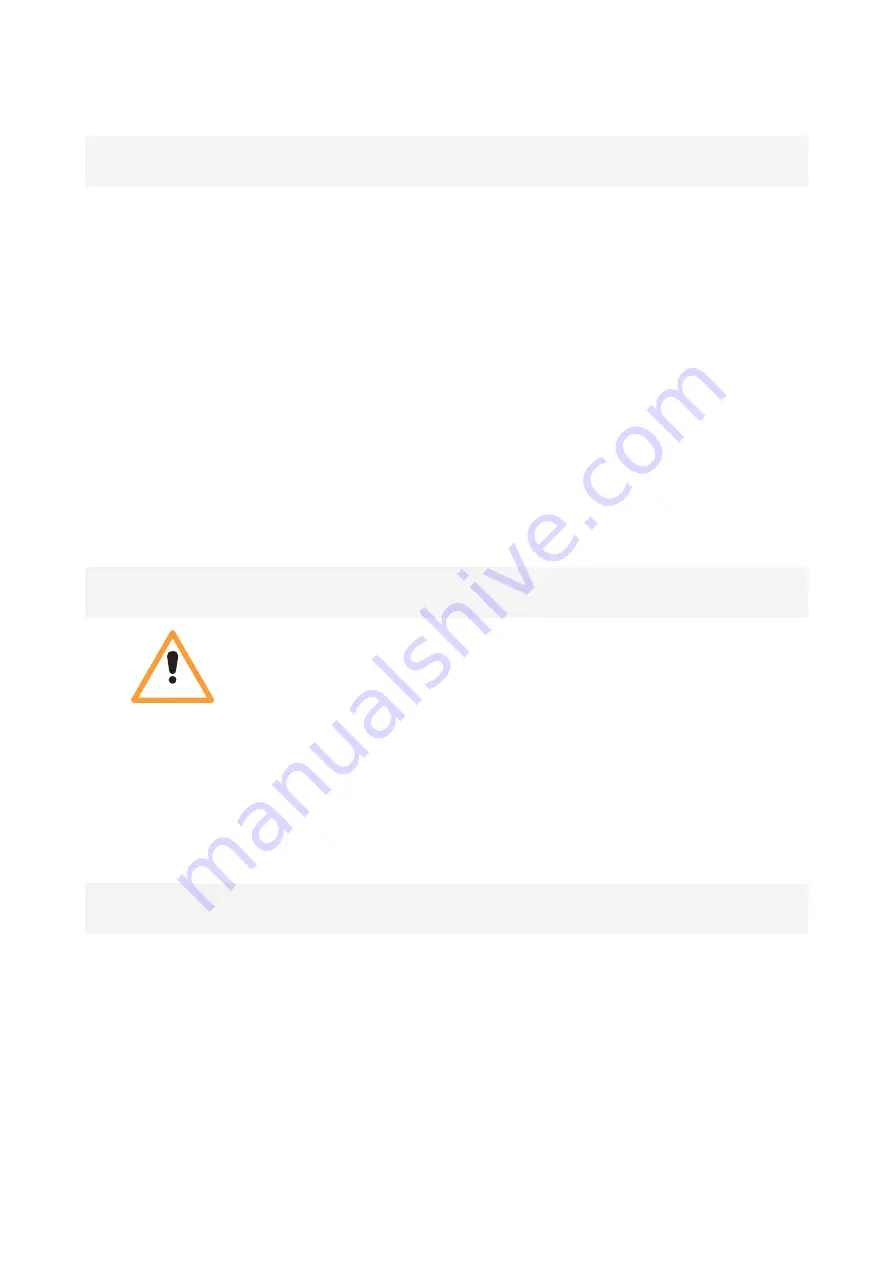
36
9.12.3 TUBE BRAZING
• Disconnect compressor from electrical wiring.
• The copper plated steel connectors on scroll compressors can be brazed in approximately the same
manner as any copper connector.
• Recommended: brazing material with a minimum of 5% silver.
• Use of a dry nitrogen purge to eliminate possibility of carbon buildup on internal connector surfaces is
recommended.
• Be sure process connector fitting I.D. and process connector O.D. are clean prior to assembly.
• Remove the discharge plug at first, and then remove the suction plug.
• Apply heat in copper connector. As connector approached brazing temperature, move torch flame to the joint.
• Heat the joint area until braze temperature is attained, moving torch up and down and rotating around
connector as necessary to heat connector evenly. Add braze material to the joint while moving torch
around circumference.
• After braze material flows around joint, move torch to heat fitting. This will draw the braze material down into
the joint. The time spent heating the compressor connector close to the compressor shell should be minimal.
• As with any brazed joint, overheating may be detrimental to the final result.
9.12.4 TUBE DISCONNECTS
Recover refrigerant from both the high and low side of the system. Failure to do
so may result in serious personal injury.
• Check the high and low pressure side with pressure gauge to make sure there
is no pressure inside.
• Heat joint area until the braze material softens and pull out the tube.
As there is a check valve close to discharge connector, take care to not overheat it and prevent brazing
material to flow into it.
Compressor mounting must be selected based on application. Consideration must be given to sound
reduction and tubing reliability. Some tubing geometry or “shock loops" may be required to reduce vibration
transferred from the compressor to external tubing.
WARNING
9.12.5 TUBING SELECTION
Proper tube design must be taken into consideration when designing the tubing connecting of the scroll to the
remaining system. The tubing should provide enough “flexibility” to allow normal starting and stopping of the
compressor without exerting excessive stress on the tube joints. In addition, it is desirable to design tubing with
a natural frequency away from the normal running frequency of the compressor. Failure to do this can result in
tube resonance and unacceptable tubing life, Figure
9.12 shows examples of acceptable tubing configurations.
The examples are intended only as guidelines to depict the need for flexibility in tube designs. In order to
properly determine if a design is appropriate for a given application, samples should be tested and evaluated
for stress under various conditions of use including voltage, frequency, and load fluctuations, and shipping
vibration. The guidelines above may be helpful; however, testing should be performed for each system designed.