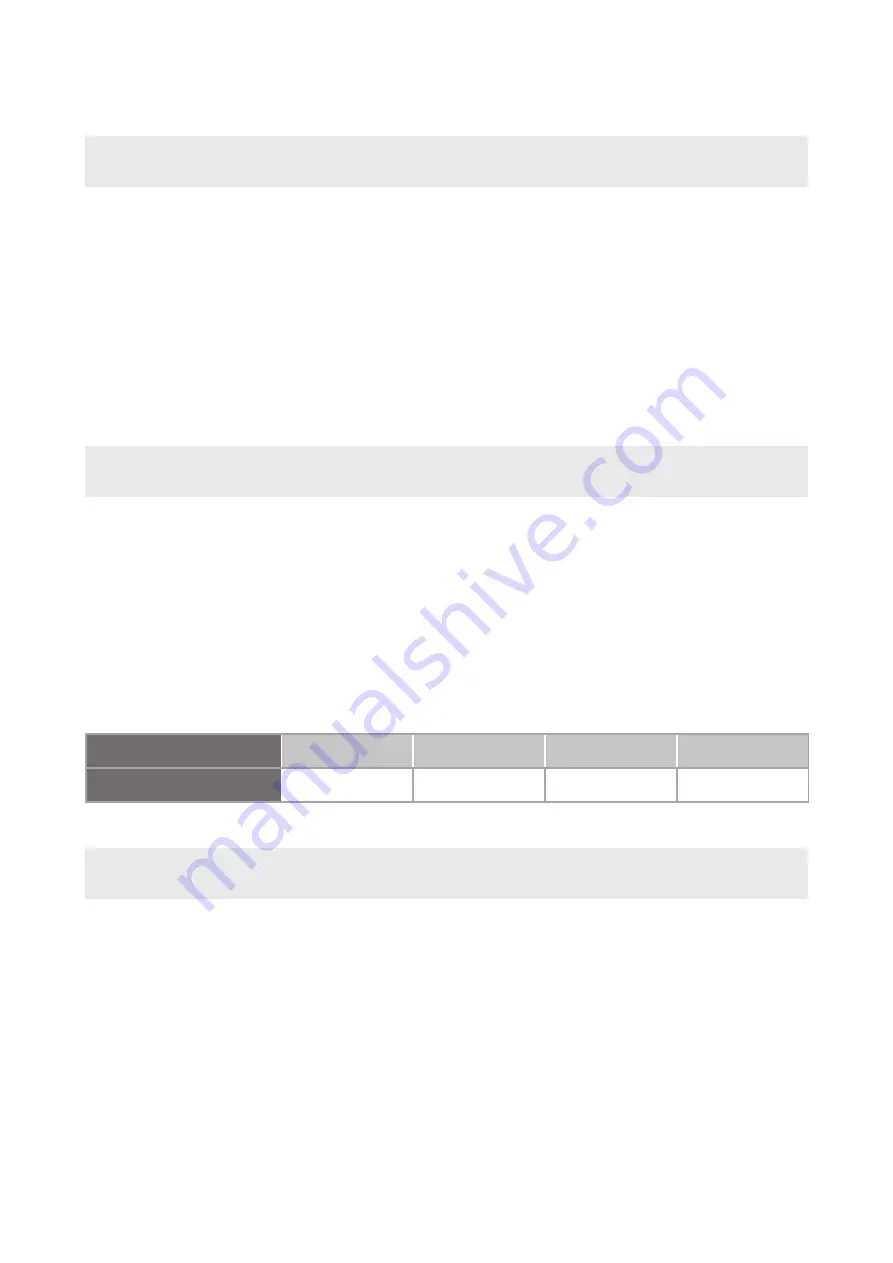
49
11.1 SYSTEM CLEANLINESS
Cleanness and reduced humidity level in all the components of the refrigeration system are the primary
concerns for the compressor good running and life. Many of contaminants are small to pass through a mesh
screen and can cause damage within a bearing assembly.
During the manufacturing process, circuit contamination can be caused by:
• brazing oxides and flux
• particles from burrs of piping
• moisture and air
Recommended impurity level of the circuit after vacuum dehydration:
10.18 ELECTRICAL INSULATION
All compressors are tested for dielectric strength and electrical insulation to ground according to requirements
IEC/EN 60335-2-34 (to be used with IEC/EN 60335-1) (latest edition).
Note: dielectric strength and compressor insulation to ground are different when the compressor is tested
in the air or in a system charged with refrigerant, due to the dielectric characteristics of the refrigerant.
11. STARTING PROCEDURE
RATED POWER
≤2.2 Kw
2.2~4.5 Kw
4.5~6.0 Kw
> 6.0 Kw
IMPURITY
500 mg
500 mg
600 mg
1100 mg
11.2 MOISTURE REMOVAL
One of the disadvantages of polyolester oil (POE) is that it is hygroscopic. Only brief exposure to ambient air can
cause moisture absorbation, to make it unacceptable for use in a refrigeration system. As it holds moisture, it
is more difficult to remove it through the use of vacuum. Compressors supplied contain oil with low moisture
content, and it may rise during the assembly process. Therefore it is recommended to use properly sized filter-
drier in whole system, which uses POE oil. This will maintain the moisture level in the oil less than 50 ppm.
If moisture content of the oil in refrigeration system reaches unacceptably high levels, corrosion and copper
plating may occur. The system should be evacuated down to 0.3 mbar or lower. If there is uncertainty of the
moisture content in the system, an oil sample should be tested for moisture.
Oil sight glass can help to indicate of moisture of refrigerant.