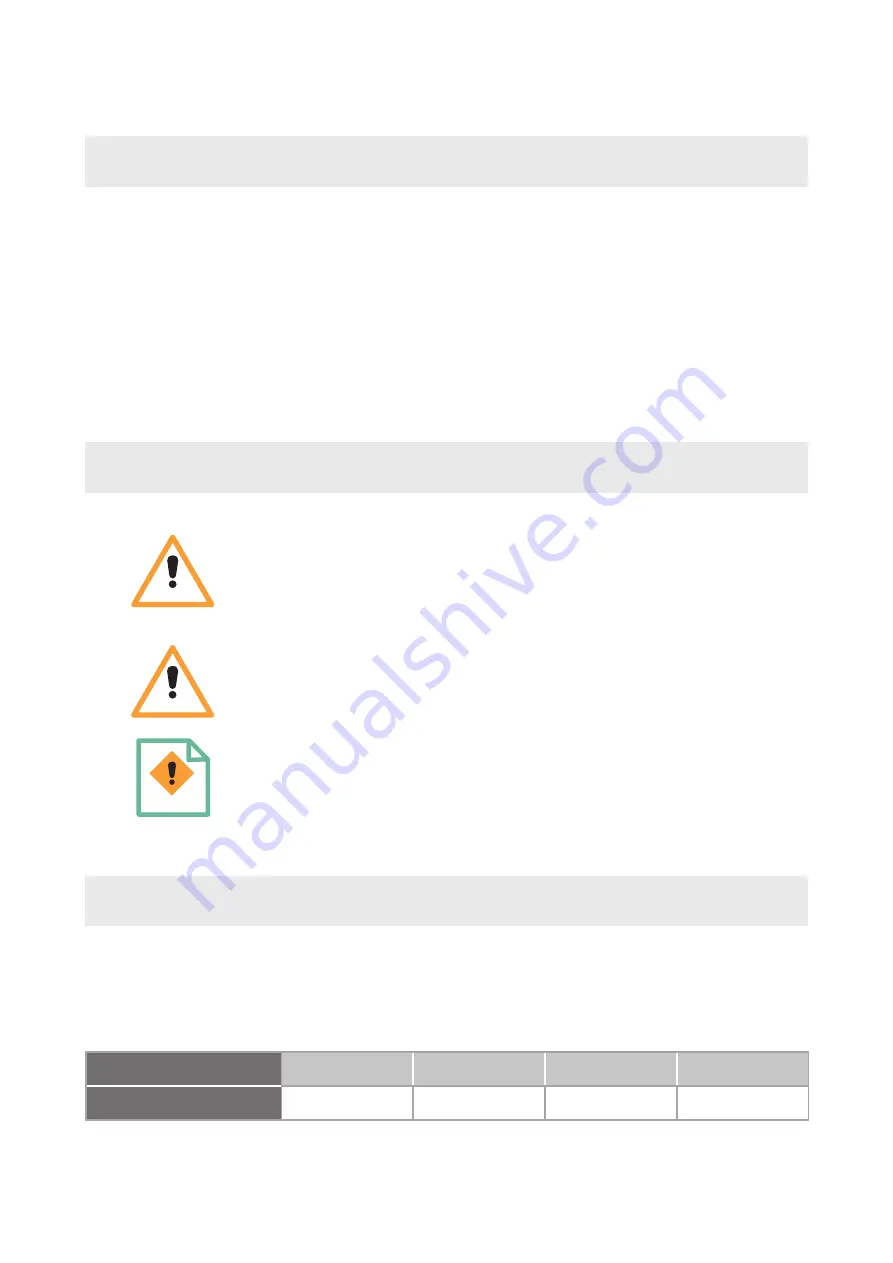
50
11.5 DEHYDRATION
The scroll compressors have a drying process on their production line, before receiving the oil charge.
The residual humidity after drying is indicated in below table.
11.3 SYSTEM EVACUATION
An important step in effectively cleaning a system before operation is proper evacuation. Air is very detrimental
to refrigeration systems and must be removed before start up and after field service. Blowing out lines with
dry nitrogen may remove a major part of the air from a system, but if air is trapped in the compressor during
installation it is practically impossible to remove from the compressor by purging with nitrogen.
Triple evacuation of the system or compressor, as required, is strongly recommended (twice to 1500 microns and
finally to 500 microns), breaking the vacuum each time with 2.07bar (rel) (30 PSIG) dry nitrogen. The vacuum
pump must be connected to both - the high and low sides of the system through properly sized coactions,
since restrictive service connections may make the process so slow as to be unacceptable, or may lead to false
readings because of pressure drop through the fittings.
11.4 DEEP VACUUM OPERATION
Do not run a refrigeration scroll compressor in a vacuum.
Do not carry out any evaluation or test of insulation (dielectric strength or hi-pot
test) with compressor under vacuum. It may result in damages of the insulation
system and, consequently, in shortening the insulation life.
Do not run a compressor before the refrigerant charge. Failure to follow these
advices can result in permanent damage to the compressor. A low-pressure control
is required for protection against vacuum operation. See the section on pressure
controls for the proper set points.
Scroll compressors should never be used to evacuate refrigeration or air
conditioning systems.
WARNING
WARNING
IMPORTANT
Table
11.5 Dehydration process
RATED POWER
≤2.2 KW
2.2~4.5 KW
4.5~6.0 KW
> 6.0 kW
MOISTURE
80 mg
100 mg
120 mg
140 mg