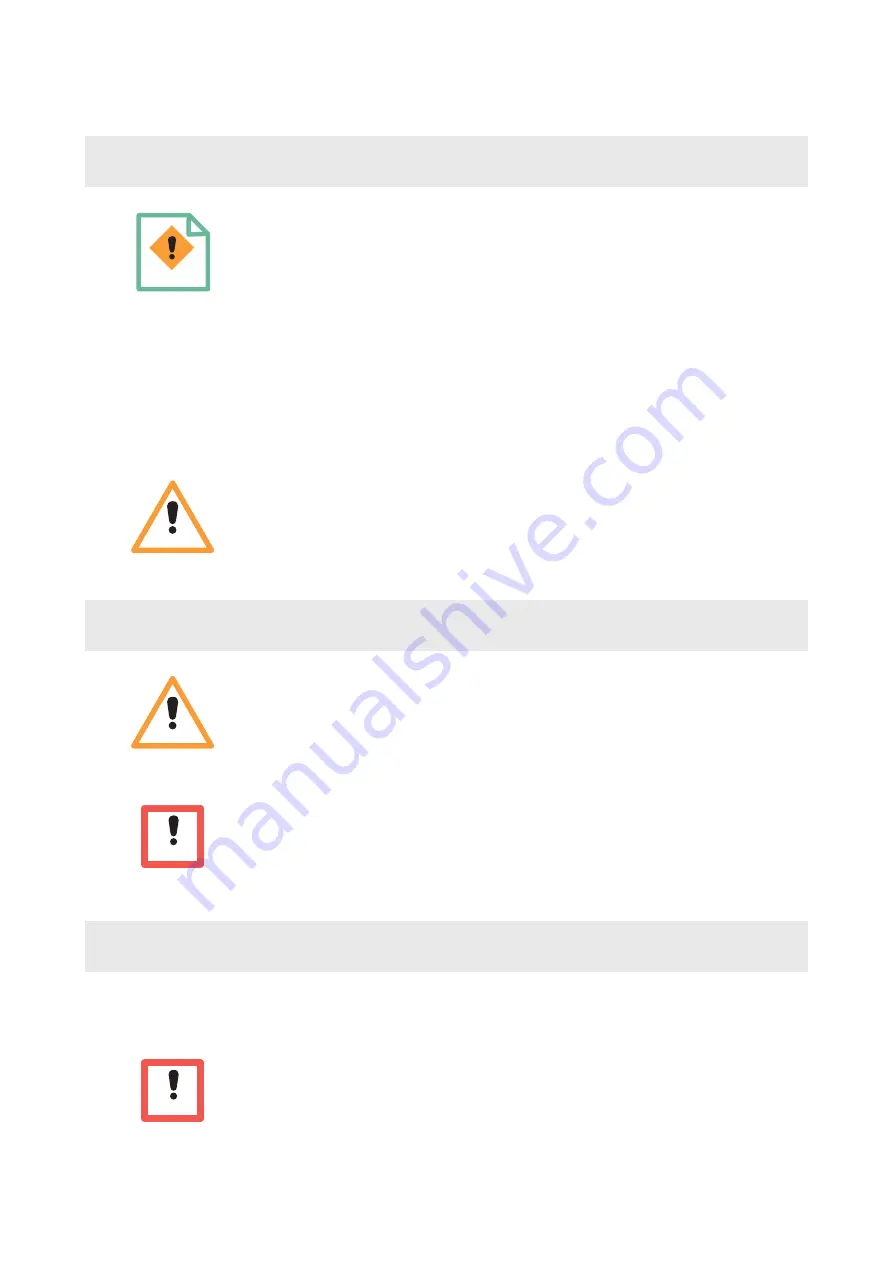
28
8.10 COMPRESSOR CYCLING
System normal cycling is 6-12 cycles per hour (depending on application);
with sufficient continuous run time to ensure the proper return of the oil to the
compressor and enough motor cooling.
The suggested minimum continuous running time is 3 minutes. To avoid frequent
start/stop, the minimum interval between the stop and next start is 3 minutes.
It is recommended to use delay timer to limit compressor cycling.
Compressor pumps oil in the system (small weight percentage of the pumped refrigerant) during running.
At compressor starting oil may be pumped in higher amount; after each start the compressor has to
run for an enough long time (depending on system design) to assure the oil returns to the compressor.
Contact
Embraco Technical support team if more info is needed.
Significant increase of cycling may impact oil circulation and overheat the motor.
It results in early damage of the compressor motor and in single phase application
to demage of its components - relay, start and run capacitor.
8.11 SHELL TEMPERATURE
System component failure may cause the top shell and discharge line to briefly
reach temperatures above 150°C. Materials (e.g. wires), which could be damaged
by these temperatures, should not come in contact with the shell.
The plastics used on the installation bases where the compressor is installed must
be self-extinguishing.
8.12 MAXIMUM DISCHARGE GAS PRESSURES AND TEMPERATURES
Systems shall be designed for Maximum operating pressures according to applicable standards (EN 378 or
similar applicable standards) that must not be exceeded.
In any case, for Embraco compressors the maximum pressure peak, during "Pull-
Down”, the maximum pressures under continuous running and the maximum
discharge gas temperature under continuous running, shall be kept below the
values indicated in follow Table:
WARNING
WARNING
CAUTION
CAUTION
IMPORTANT