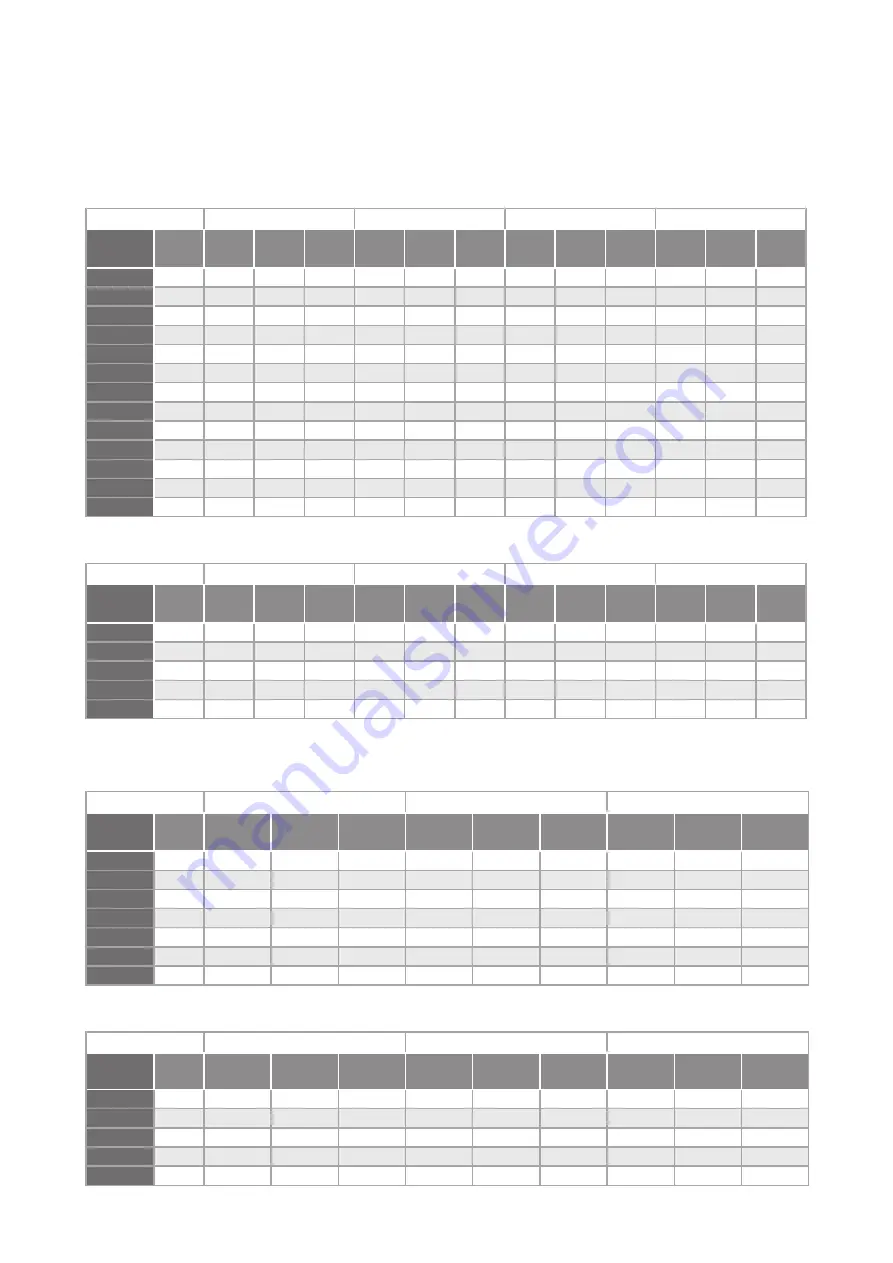
21
PRODUCTS
R404A
R449A
R452A
R134A
EMBRACO
MODEL
HP
Cooling
Capacity
(W)
Power
Input
(W)
COP
(W/W)
Cooling
Capacity
(W)
Power
Input
(W)
COP
(W/W)
Cooling
Capacity
(W)
Power
Input
(W)
COP
(W/W)
Cooling
Capacity
(W)
Power
Input
(W)
COP
(W/W)
SE6015GS-O
2
3689
1864
1.98
3565
1735
2.05
3560
1862
1.91
2081
1093
1.9
SE6018GS-O
2.5
4405
2105
2.09
4256
1960
2.17
4250
2103
2.02
2484
1236
2.01
SE6021GS-O
3
5016
2335
2.15
4847
2173
2.23
4840
2332
2.08
2829
1369
2.07
SE6026GS-O
3.5
6322
2951
2.14
6108
2747
2.22
6100
2948
2.07
3566
1731
2.06
SE6030GS-O
4
7172
3235
2.22
6930
3011
2.3
6920
3231
2.14
4045
1897
2.13
SE6036GS-O
5
8809
3895
2.26
8512
3625
2.35
8500
3890
2.19
4969
2284
2.18
SE6043GS-O
6
10467
4628
2.26
10114
4308
2.35
10100
4623
2.18
5904
2714
2.18
SE6053GS-O
7
12685
5609
2.26
12257
5221
2.35
12240
5602
2.18
7155
3289
2.18
SE6056GS-O
8
13362
5908
2.26
12911
5499
2.35
12893
5901
2.18
7536
3465
2.17
SE6067GS-O
9
16418
7259
2.26
15864
6757
2.35
15842
7251
2.18
9260
4257
2.18
SE6078GS-O
10
18505
8182
2.26
17881
7616
2.35
17856
8173
2.18
10437
4798
2.18
SE6085GS-O
12
20246
8863
2.28
19563
8250
2.37
19536
8853
2.21
11419
5198
2.2
SE6089GS-O
13
21291
9320
2.28
20573
8676
2.37
20544
9310
2.21
12009
5466
2.2
Table
7.1 MBP - 3PH – 380V 50HZ
Table
7.2 MBP - 1PH – 220V 50HZ
Table
7.3 LBP 3PH – 380V 50HZ
Table
7.4 LBP 1PH – 220V 50HZ
Testing conditions: EN12900 Te -10°C; Tc 45°C; Rg 20°C; No subcooling; Ta 35°C
7. TECHNICAL SPECIFICATIONS
PRODUCTS
R404A
R449A
R452A
R134A
EMBRACO
MODEL
HP
Cooling
Capacity
(W)
Power
Input
(W)
COP
(W/W)
Cooling
Capacity
(W)
Power
Input
(W)
COP
(W/W)
Cooling
Capacity
(W)
Power
Input
(W)
COP
(W/W)
Cooling
Capacity
(W)
Power
Input
(W)
COP
(W/W)
SE6015GK-C
2
3689
1897
1.94
3565
1766
2.02
3560
1895
1.88
2081
1112
1.87
SE6018GK-C
2.5
4405
2213
1.99
4256
2060
2.07
4250
2211
1.92
2484
1298
1.91
SE6021GK-C
3
5016
2464
2.04
4847
2294
2.11
4840
2461
1.97
2829
1445
1.96
SE6026GK-C
3.5
6322
3010
2.1
6108
2802
2.18
6100
3007
2.03
3566
1765
2.02
SE6030GK-C
4
7172
3300
2.17
6930
3072
2.26
6920
3296
2.1
4045
1935
2.09
PRODUCTS
R404A
R449A
R452A
EMBRACO
MODEL
HP
Cooling
Capacity
(W)
Power Input
(W)
COP (W/W)
Cooling
Capacity
(W)
Power Input
(W)
COP (W/W)
Cooling
Capacity
(W)
Power Input
(W)
COP (W/W)
SE2006GS-O
2
1261
1168
1.08
1171
1067
1.1
1241
1131
1.1
SE2008GS-O
2.5
1610
1480
1.09
1495
1352
1.11
1585
1434
1.11
SE2010GS-O
3
1891
1722
1.1
1756
1572
1.12
1862
1668
1.12
SE2012GS-O
3.5
2453
2233
1.1
2277
2040
1.12
2414
2163
1.11
SE2014GS-O
4
2861
2376
1.2
2656
2170
1.22
2817
2302
1.22
SE2017GS-O
5
3395
2729
1.24
3152
2492
1.26
3342
2643
1.26
SE2020GS-O
6
3977
3172
1.25
3692
2897
1.27
3915
3072
1.27
PRODUCTS
R404A
R449A
R452A
EMBRACO
MODEL
HP
Cooling
Capacity
(W)
Power Input
(W)
COP (W/W)
Cooling
Capacity
(W)
Power Input
(W)
COP (W/W)
Cooling
Capacity
(W)
Power Input
(W)
COP (W/W)
SE2006GK-C
2
1261
1178
1,07
1171
1076
1,09
1241
1141
1,09
SE2008GK-C
2,5
1610
1510
1,07
1495
1379
1,08
1585
1463
1,08
SE2010GK-C
3
1891
1762
1,07
1756
1609
1,09
1862
1707
1,09
SE2012GK-C
3,5
2453
2281
1,08
2277
2083
1,09
2414
2209
1,09
SE2014GK-C
4
2861
2427
1,18
2656
2216
1,2
2817
2351
1,2
Testing conditions: EN12900 Te -35°C; Tc 40°C; Rg 20°C; No subcooling; Ta 35°C
Figure 6.5 Sight glass