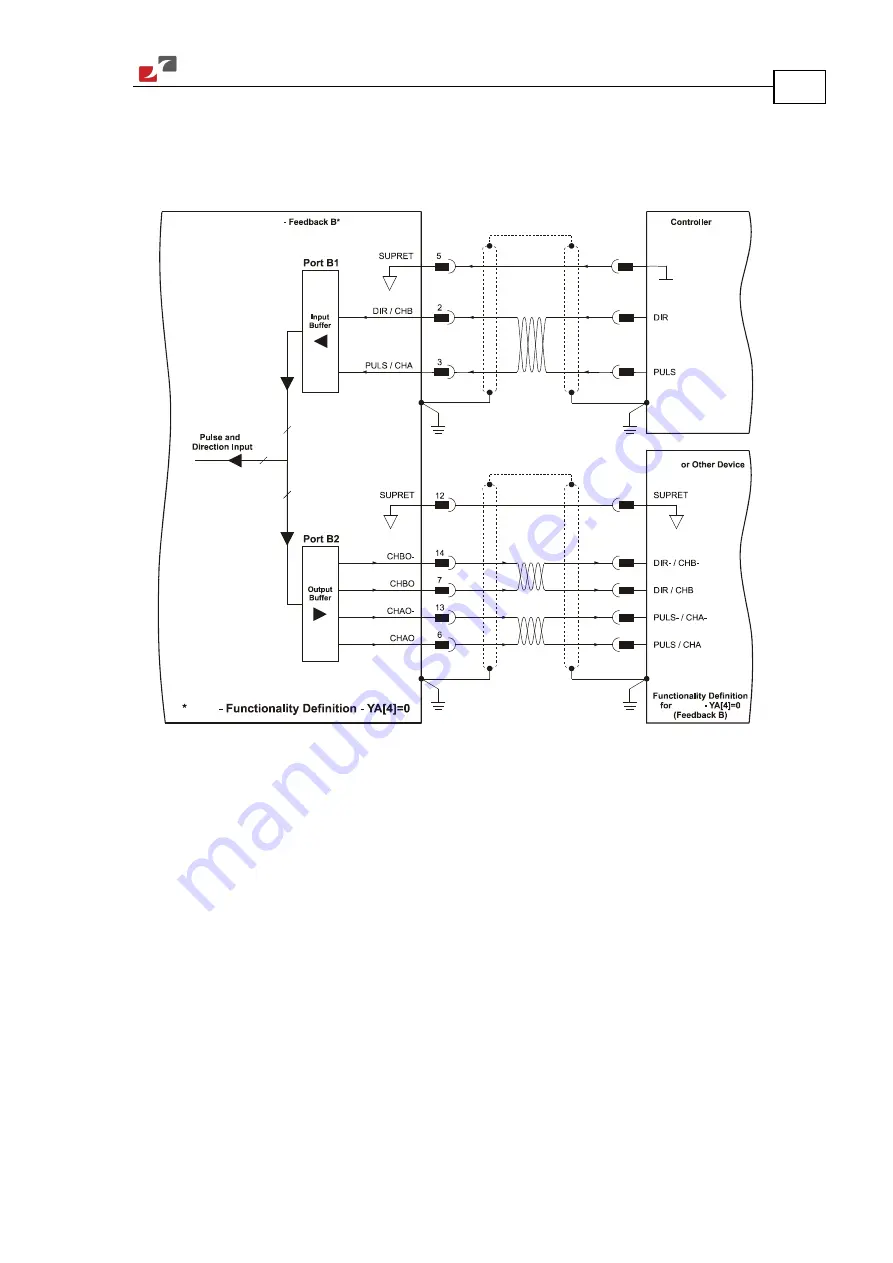
Tuba Installation Guide
Installation
MAN-TUBIG (Ver. 1.503)
48
FEEDBACK B on the front of the Tuba has a 15-pin D-Sub plug. Connect the Auxiliary Feedback
cable from the Pulse and Direction Controller to FEEDBACK B using a 15-pin D-Sub socket with a
metal housing. When assembling the Auxiliary Feedback cable, follow the instructions in
Section 3.4.4 (Feedback and Control Cable Assemblies).
Tuba
Tuba
Tuba
Tuba
Figure 27: Single-Ended Pulse-and-Direction Input Option on FEEDBACK B - Connection
Diagram