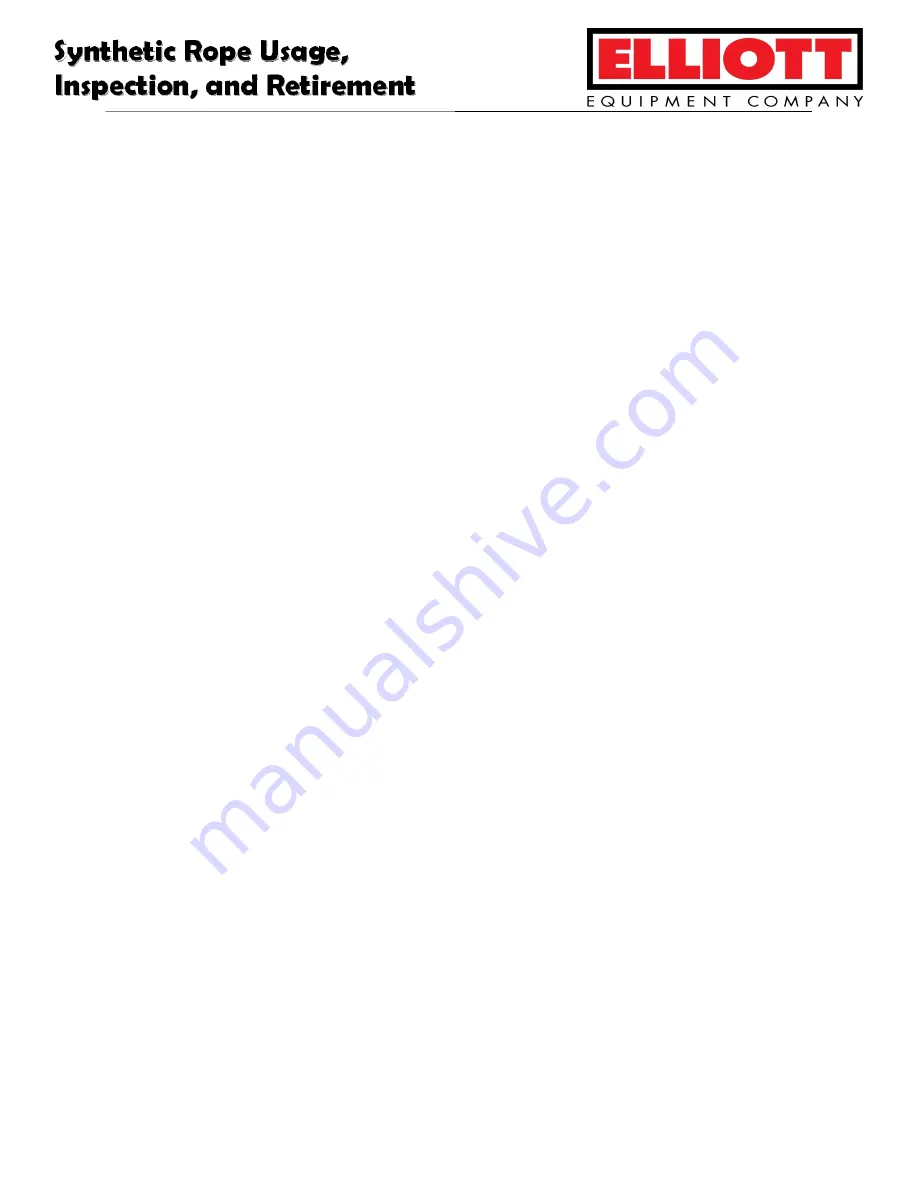
Synthetic Rope Usage EEC-0060
V1.2
Synthetic Rope Usage,
Inspection, and Retirement
End-For-Ending
It is recommended that every winch line be rotated end-for-end on a periodic
basis. This will vary high stress and wear points and extend useful life. The
recommended end-for-ending period is six months, at which time visual inspection and
washing can also be done.
Bending Radius
Any sharp bend in a road under load decreases its strength substantially, and
may cause premature damage or failure. In sizing the radius of bits, fairleads and
chocks for best performance the following guidelines are offered:
When a rope bends more than 10 degrees around bitts or chocks, or is bending
across any surface, the diameter of that surface should not be less than three
times the diameter of the rope. That is, whatever is the diameter of the surface
should be no less than three times the diameter of the rope. Using a ratio of 4:1
or greater is better because the durability of the rope increases substantially as
the diameter of the surface of which it is worked increases.
On a cleat when the rope does not bend radially around, the cleat’s barrel can
only be one-half of the rope’s circumferences at a minimum.
The ratio of the length of an eye splice to the diameter of the object over which
the eye placement (i.e. bollard, bitt, etc.) should be at least 3:1, but preferably
5:1. So, for example, bollard that is 2 feet in diameter should have the eye splice
to be no less than 6 feet in length, preferably 10 feet in length.
Boom-Sheave Recommendations
To assure maximum efficiency and safety, sheaves for braided ropes should be
no less than eight times the rope’s diameter, and the sheave groove diameter should be
no less than 10 percent greater than the rope’s diameter. The sheave groove should be
round in shape, and sheaves with a “V”-shape groove should be avoided, as they tend
to pinch and damage the rope excessive friction and crushing rope fibers. Sheave
Summary of Contents for Digger Derrick
Page 2: ......
Page 37: ...Nomenclature EEC 0169 V1 0 Nomenclature...
Page 39: ...Platform Safety EEC 0061 V1 1 Platform Safety...
Page 54: ...Platform Safety EEC 0061 V1 1 Platform Safety...
Page 116: ...Jib Operation EEC 0044 V1 1 Jib Operation E C B A C2 C1 B...
Page 161: ...Digger Derrick Labels EEC 0171 V1 0 Digger Derrick Labels...
Page 163: ...Digger Derrick Labels EEC 0171 V1 0 Digger Derrick Labels 12 20 22 23 24 28 29...
Page 164: ...Digger Derrick Labels EEC 0171 V1 0 Digger Derrick Labels 30 38 39...
Page 170: ...Digger Derrick Specs EEC 0170 V1 2 Digger Derrick Specifications...
Page 172: ......
Page 173: ......
Page 174: ......
Page 175: ......
Page 176: ......
Page 179: ...3 2 1 4 6 5 3 2 1 4 6 5 3 2 1 4 6 5 TITLE...
Page 180: ......
Page 181: ......
Page 182: ......
Page 183: ......
Page 193: ...Bolt Torque EEC 0016 V1 2 Bolt Torque...
Page 199: ...Four Section Boom Operation common EEC 0021 V1 3 Four Section Boom Operation...
Page 227: ...4 HYDRAULIC SCHEMATIC...
Page 240: ...17 EXPLODED ISOMETRIC ASSEMBLY DRAWING...
Page 245: ...4 5200S...
Page 246: ...5 6000S...
Page 247: ...Elliott Operating Manual...
Page 277: ...Elliott Calibration and Troubleshooting Manual...
Page 312: ...36 W450321A 09 12...
Page 362: ......
Page 375: ...Appendix B Parts Index ELLIOTT Built for You Digger Derrick Truck B 1...