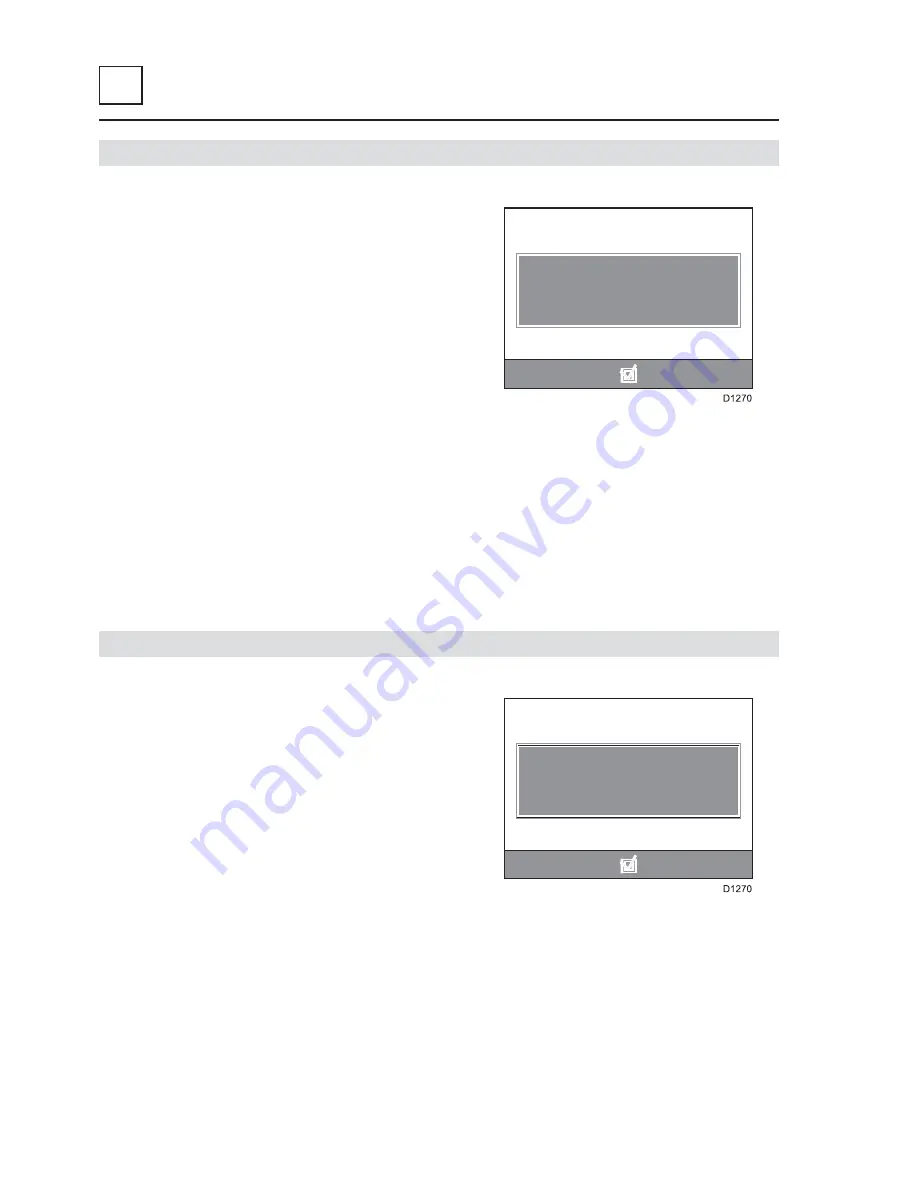
10
51
Service
Manual
Troubleshooting
04102011/GB
06.2009
LENGTH FOLDING ERROR
This screen is not activated yet.
09. FOLDING TRANSFER ERROR
Read instructions in the manual
or contact your technician
10. CROSS FOLD 1 JAMMED
Remove item according to instructions
in manual or contact your technician
CROSS FOLD 1 JAMMED
A linen is jammed in the 1
st
cross folding.
1. Remove the rear frame of the machine.
2. Remove the jammed linen in the cross.
3. Put the frame.
4. Press ‘
Validation
’ button to start again
the machine.
Summary of Contents for IC4 4819 FFS
Page 1: ...Service manual IC4 4819 4825 4832 FFS Feeder Ironer Folder Stacker 04102011 GB 43 2015 ...
Page 2: ...This page is left blank on purpose ...
Page 4: ...This page is left blank on purpose ...
Page 5: ...1 04102011 GB 06 2009 Service Manual Safety ...
Page 6: ...This page is left blank on purpose ...
Page 10: ...This page is left blank on purpose ...
Page 12: ...This page is left blank on purpose ...
Page 16: ...This page is left blank on purpose ...
Page 18: ...This page is left blank on purpose ...
Page 26: ...This page is left blank on purpose ...
Page 55: ...10 27 Service Manual Installation 04102011 GB 51 2010 This page is left blank on purpose ...
Page 56: ...This page is left blank on purpose ...
Page 58: ...This page is left blank on purpose ...
Page 66: ...This page is left blank on purpose ...
Page 68: ...This page is left blank on purpose ...
Page 71: ...20 3 Service Manual Operation 04102011 GB 06 2009 This page is left blank on purpose ...
Page 72: ...This page is left blank on purpose ...
Page 74: ...This page is left blank on purpose ...
Page 114: ...This page is left blank on purpose ...
Page 178: ...This page is left blank on purpose ...
Page 180: ...This page is left blank on purpose ...
Page 192: ...This page is left blank on purpose ...
Page 194: ...This page is left blank on purpose ...
Page 200: ...This page is left blank on purpose ...
Page 202: ...This page is left blank on purpose ...
Page 209: ...25 7 Service Manual Gas heating 04102011 GB 50 2011 This page is left blank on purpose ...
Page 222: ...This page is left blank on purpose ...
Page 224: ...This page is left blank on purpose ...
Page 227: ...26 3 Service Manual Steam heating 04102011 GB 06 2009 This page is left blank on purpose ...
Page 230: ...This page is left blank on purpose ...
Page 232: ...This page is left blank on purpose ...
Page 236: ...This page is left blank on purpose ...
Page 238: ...This page is left blank on purpose ...
Page 244: ...This page is left blank on purpose ...
Page 246: ...This page is left blank on purpose ...
Page 256: ...This page is left blank on purpose ...
Page 258: ...This page is left blank on purpose ...
Page 267: ...30 9 Service Manual Feeding Motion 04102011 GB 21 2012 This page is left blank on purpose ...
Page 268: ...This page is left blank on purpose ...
Page 270: ...This page is left blank on purpose ...
Page 278: ...This page is left blank on purpose ...
Page 280: ...This page is left blank on purpose ...
Page 296: ...This page is left blank on purpose ...
Page 298: ...This page is left blank on purpose ...
Page 303: ...33 5 Service Manual Cross folding 04102011 GB 06 2009 This page is left blank on purpose ...
Page 310: ...12 33 KM12 Service Manual Cross folding 04102011 GB 06 2009 FC510 switch left casing support ...
Page 312: ...This page is left blank on purpose ...
Page 314: ...This page is left blank on purpose ...
Page 322: ...This page is left blank on purpose ...
Page 324: ...This page is left blank on purpose ...
Page 330: ...This page is left blank on purpose ...
Page 332: ...This page is left blank on purpose ...
Page 335: ...36 3 Service Manual Electrostatic bar 04102011 GB 43 2015 This page is left blank on purpose ...
Page 338: ...This page is left blank on purpose ...
Page 340: ...This page is left blank on purpose ...
Page 348: ...This page is left blank on purpose ...
Page 350: ...This page is left blank on purpose ...
Page 365: ...51 15 Service Manual Troubleshooting 04102011 GB 06 2009 This page is left blank on purpose ...
Page 366: ...This page is left blank on purpose ...
Page 367: ...This page is left blank on purpose ...
Page 368: ...www electrolux com laundrysystems Share more of our thinking at www electrolux com ...